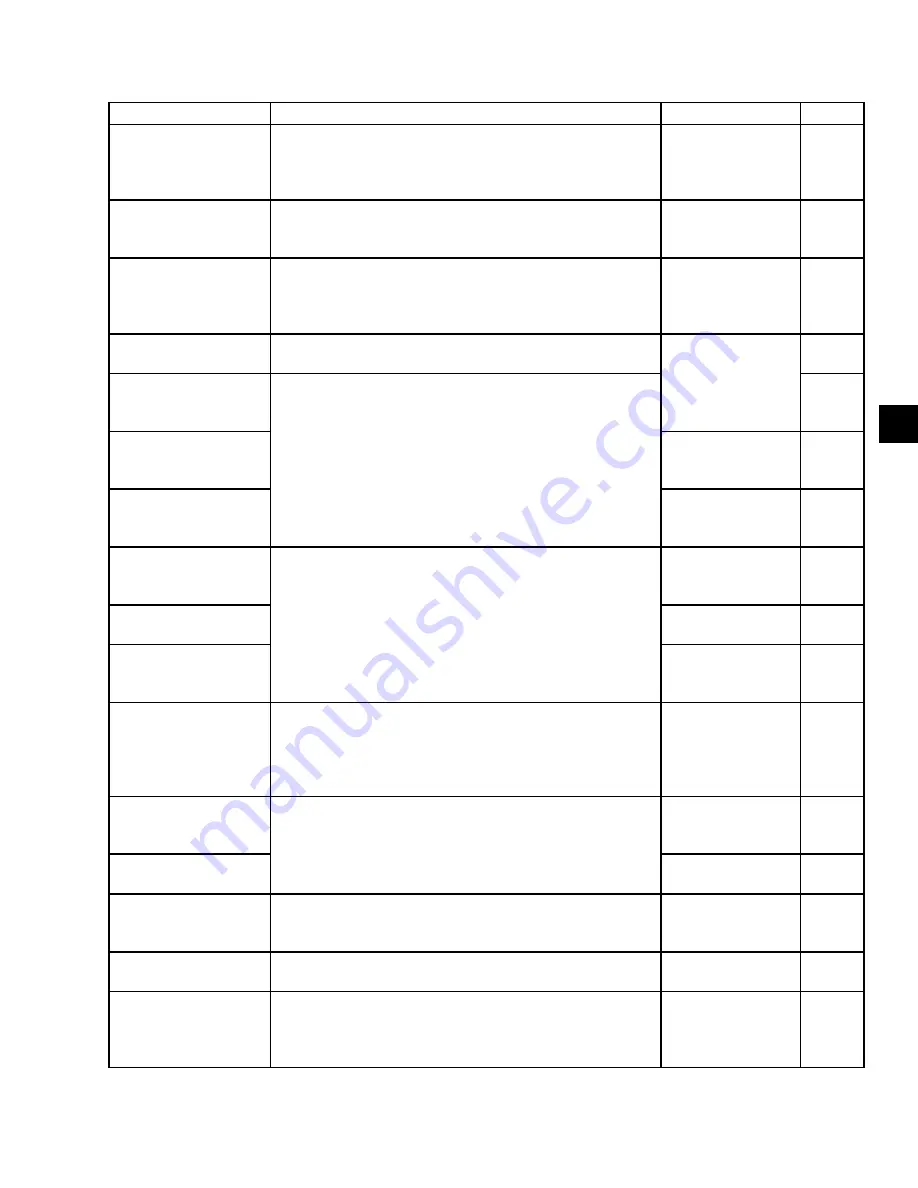
JOHNSON CONTROLS
141
SECTION 7 – MAINTENANCE
FORM 155.31-ICOM2.EN.UL
ISSUE DATE: 12/21/2018
7
TASK
CONTENTS
FREQUENCY
SCOPE
Repair of paint (tar epoxy
paint) of inside wall of
chilled water and cooling
waterboxes
Repair the paint of the inside wall.
Chilled water: 2 years
Cooling water: \1 year
S
Analysis of solution and
addition of inhibitor
The concentration of the inhibitor must be kept proper to
prevent corrosion of inside parts. Analyze the solution to detect
leakage in the early stage of running the machine
Every 6 months
S
Filtration and refining of
solution
As the inside of the chiller is corroded, corrosion particles are
increased. Particles accumulated on the heat exchange tube
surfaces lower the heat exchange rate, that is, the performance.
Accordingly, filter the solution.
5-6 years
S
Check of operation of
various safety relays
Check the operation of the safety relays.
Yearly
S
Cleaning of tubes
with brush or water jet
(Absorber, condenser)
If foreign matter sticks to the inside of the tubes of the chiller,
refrigerating performance is lowered and the tubes become
corroded. Accordingly, remove slime, soft scales, and other
foreign matter from the inside of the tubes.
S
Cleaning of tubes
with brush or water jet
(Evaporator)
Every 2 years*
S
Cleaning of tubes with
brush or water jet (High
temperature generator)
Every 4 years
S
Chemical cleaning
of tubes (Absorber,
condenser)
Since hard scales sticking to the tubes cannot be removed with
a brush or water jet, remove them chemically, depending on the
condition.
S
Chemical cleaning of
tubes (Evaporator)
Every 4 years*
S
Chemical cleaning of
tubes (High temperature
generator)
Every 8 years*
S
Check for slight leakage
Vacuum and airtightness must be maintained to ensure the
reliability and performance of the absorption chiller. Accordingly,
recommend that the machine should be checked for slight
leakage with a special vacuum and airtightness diagnostic
device.
Every 2 years
S
Eddy current test
on tubes (Absorber,
condenser)
Check the inside of the tubes for corrosion caused by bad
quality chilled water, and cooling water.
Every 4 years
S
Eddy current test on
tubes (Evaporator)
Every 6 years
S
Eddy current test on
tubes (High temperature
generator)
Check the inside of the tubes for corrosion caused by bad
quality steam.
Every 4 years or
10,000 hours
S
Check of steam control
valve seat
Check the steam control valve seat for leakage while the chiller
is stopping.
Yearly
S
Check of the steam
control valve regulator
filter (pneumatic type
steam control valve only)
Check the air filter of the steam control valve regulator for
clogging.
Yearly
S
C = Customer, S = Johnson Controls Service
NOTE:
*If water quality analysis indicates necessity.
TABLE 28 -
MAINTENANCE AND INSPECTION (CONT'D)