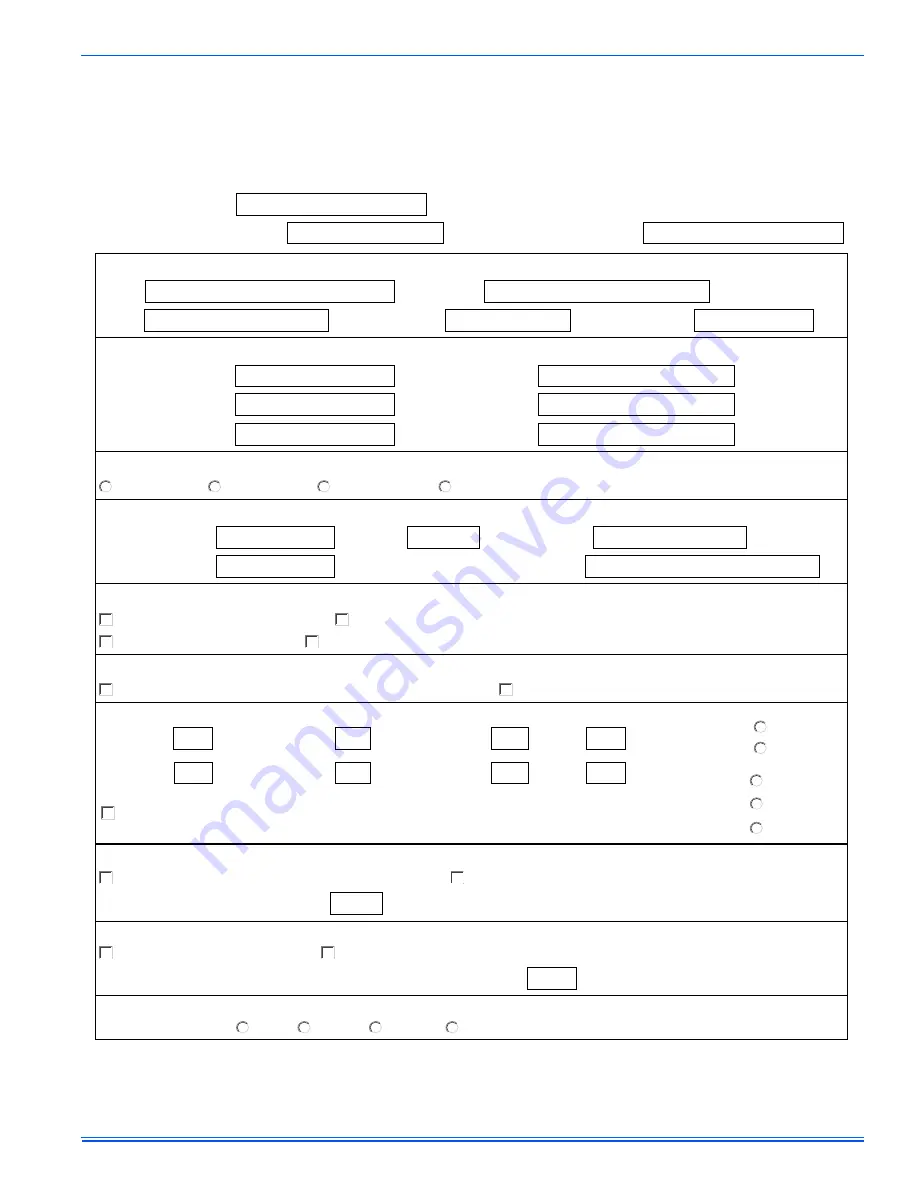
1034868-UIM-A-0513
Johnson Controls Unitary Products
45
33" 96% AFUE Two Stage Gas Furnace Start Up Sheet
Proper furnace start up is critical to customer comfort and equipment longevity
Name
Address
City
State or Province
Zip or Postal Code
Furnace Model
Furnace Serial
Evaporator Coil Model
Evaporator Coil Serial
Upflow
Downflow
Horizontal Left
Horizontal Right
Unit is level or tilted slightly forward
Filter Type
Thermostat Type
Other System Equipment and Accessories
Owner Information
Equipment Data
Furnace Configuration
Outdoor Unit Model
Outdoor Unit Serial
Filter, Thermostat, Accessories
Filter Location(s)
Connections -- All Per Installation Instructions and Local Code
Gas piping is connected (including drip leg)
Supply plenum and return air are connected
Filter Size
Vent system is connected
Technician Performing Start-Up
Installing Contractor Name
Start-Up Date
Continued on next Page
OFF
10 MIN
15 MIN
20 MIN
Thermostat Staging:
Staging:
Venting system is the proper size, within the limitations of the chart in the installation
instructions, properly connected to the furnace, and properly pitched
Condensate drain is connected
Intake Size
Exhaust Size
# of 90 Degree Ells
# of 45 Degree Ells
Length
Length
# of 45 Degree Ells
# of 90 Degree Ells
Polarity is correct (black is L1 (hot), white is N (neutral)
Ground wire is connected from the furnace to electrical panel
Line voltage value to furnace (volts AC)
Low voltage value between "R" and "C" on furnace control board (volts AC)
Condensate Management
Venting
Electrical: Line Voltage
Thermostat wiring is complete
Electrical: Low Voltage
Condensate tubing is correctly installed for the furnace position
Sidewall
Roof
Sidewall
Roof
Attic
Exhaust
Termination
Intake
Termination
Thermostat heat anticipator set to .4 or (6 cycles per hour for electronic thermostats)
SECTION XIII: START UP SHEET