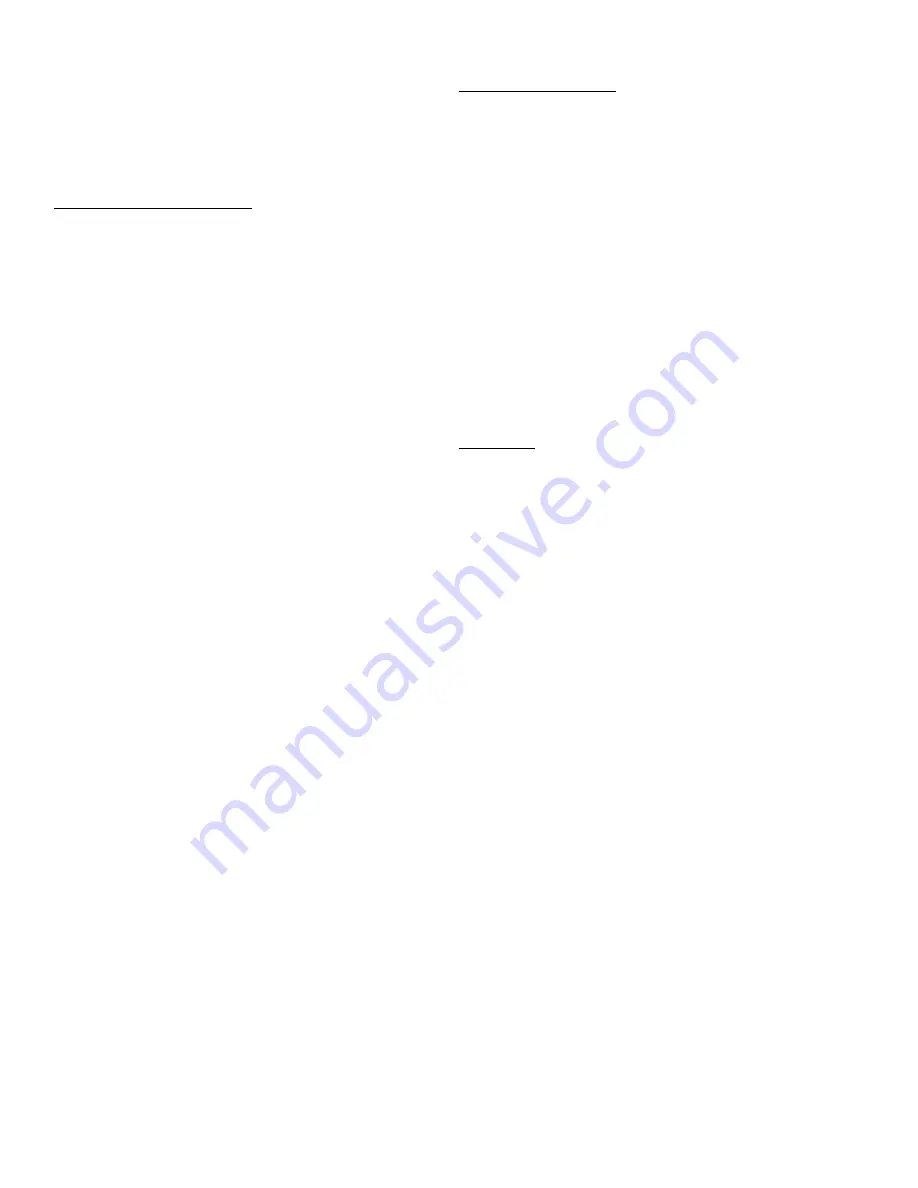
5331896-YTG-C-1017
6
Johnson Controls Unitary Products
Outdoor Fan Assembly -
The outdoor fan shall be of the
direct-driven propeller type, discharge air vertically, have
aluminum blades riveted to corrosion resistant steel spider
bracket and shall be statically balanced for smooth operation.
The outdoor fan motor shall be totally enclosed with
permanently lubricated bearings and internally protected
against overload conditions.
REFRIGERANT COMPONENTS
•
Protected Compressor -
The compressor shall be a fully
hermetic type, direct drive compressor, that is internally pro-
tected against high pressure and temperature. This is
accomplished by the simultaneous operation of high pres-
sure internal relief valve and a temperature sensor which
protect the compressor if undesirable operating conditions
occur. The hermetic motor shall be suction gas cooled and
have a voltage range of +/- 10% of the unit nameplate volt-
age. Compressors shall have internal isolation and sound
muffling to minimize vibration and noise, and be externally
isolated on a dedicated, independent mounting.
•
Indoor Coils -
Indoor coils shall be of the direct expansion,
draw through design and have aluminum plate fins mechani-
cally bonded to seamless internally enhanced tin-coated
copper tubes with all joints brazed.
•
Condensate Pan -
A corrosion-resistant, long-lasting, water-
tight pan is positioned below the indoor coil to collect and
drain all condensate, preventing build-up of stagnant con-
densate. The condensate pan conforms to ASHRAE 62-89
standards (Ventilation for Acceptable Indoor Air Quality).
•
Condensate Drain -
The 3/4 inch NPT female connection is
rigidly mounted to assure proper fit and leak tight seal.
•
Outdoor Coils -
Outdoor coils shall have aluminum plate
fins mechanically bonded to seamless internally enhanced
copper tubes with all joints brazed, and be a draw through
design.
Refrigerant Circuit and Refrigerant Safety Components
shall include:
Thermal expansion devices (TXVs) shall be
factory mounted and provided, Filter/strainer to eliminate any
foreign matter, reversing valves to control refrigerant flow.
GAS HEATING SECTION
Heat exchanger and exhaust system shall be constructed of
corrosion-resistant materials and shall be designed with
induced draft combustion with post purge logic and redundant
main gas valve. The heat exchanger shall be of the tubular
type, constructed of stainless steel for corrosion resistance and
allowing minimum mixed air entering temperature of 40 °
F.
Burners shall be of the in-shot type, constructed of
aluminumized steel. All gas piping shall enter the unit cabinet at
a single location through either the side or bottom, without any
field modifications. An integrated control board shall provide
timed control of indoor fan functioning and burner ignition.
Heating section shall be provided with the following minimum
protection:
a. Primary high-temperature limit switch.
b. Induced draft pressure switch.
c. Flame roll out switch(s) (manual reset).
d. Flame proving controls.
All gas heat models will meet California requirement for
emissions of less than 40 nanograms per Joule (California
requirement on single phase models only).
CONTROLS
•
Simple Control Circuit -
Field thermostat wiring connects to
color coded leads using twist on wire connections. Cooling
controls use contactor and relays for simple application and
troubleshooting. Mate-n-lock plug connectors are used.
Heating controls consist of direct spark ignition control and
demand defrost heat pump control. The electrical control box
is not located in the compressor compartment. The controls
are mounted to allow the separate access panel to be
removed for trouble shooting and maintenance without
affecting the normal system operating pressures. All wiring
internal to the unit is color/number coded.
•
Pressure Switches -
A high pressure switch is standard in
all units. When abnormal conditions are sensed through the
pressure switch, the unit will lock out preventing any further
operation until reset or problem is corrected.
•
Factory Testing -
Installation time and costs are reduced by
easy power and control wiring connections. All units are
completely wired, charged with R-410A and tested prior to
shipment. Test stations using a state-of-the-art computerized
process system shall be used to insure product quality.
Refrigerant charge and component part numbers are verified
via computer bar code scans during assembly. Vital run test
statistics such as system pressure, motor currents, air veloc-
ity and temperature, unit vibration, and gas system safeties
are monitored and recorded by the system to insure unit per-
formance. This data could be provided by serial number
tracking if requested.
Spark To Burner Ignition -
No pilot assembly required, which
provides more consistent ignition in gas heating mode. This
ignition is highly reliable, durable and eliminates nuisance
lockouts.