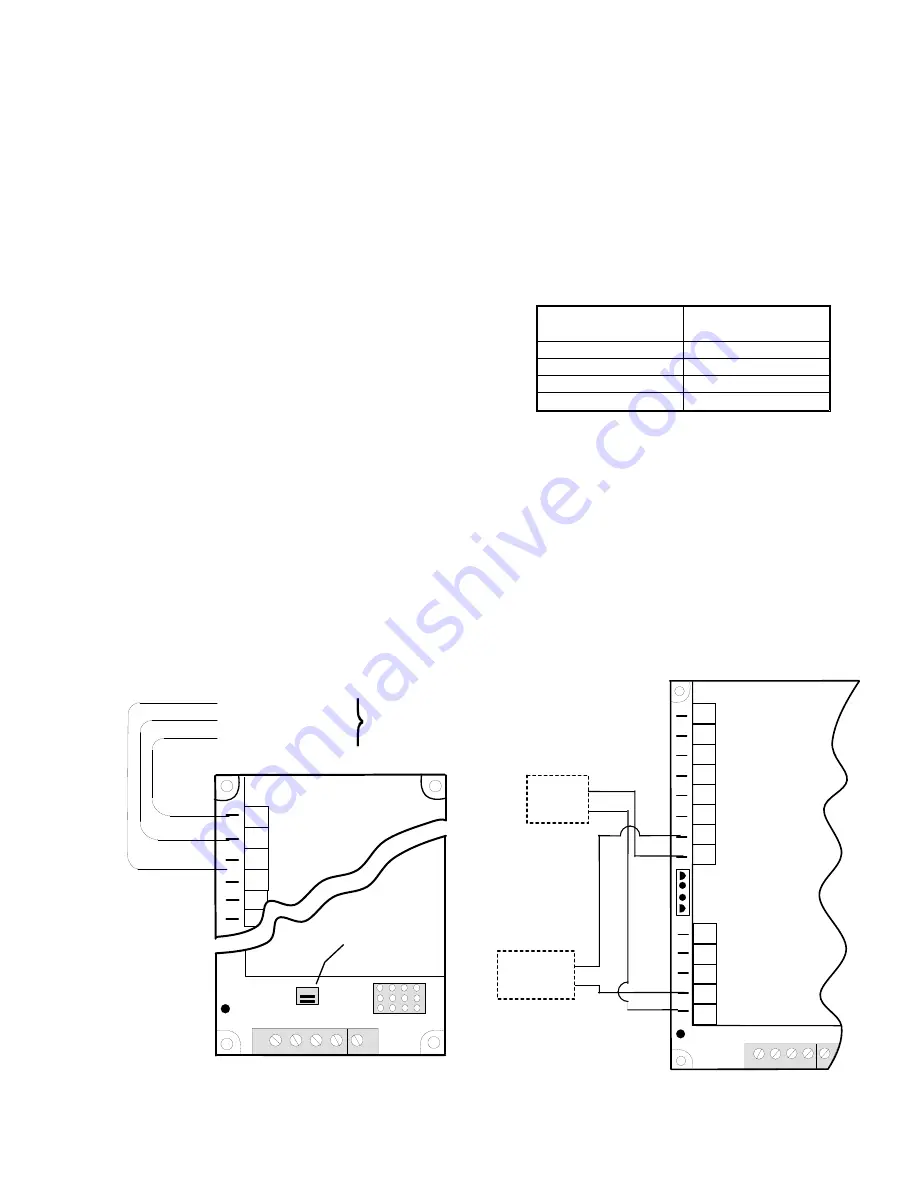
WARNING: If manifold pressure is too high, an over-fire con-
dition exists which could cause heat exchanger failure. If
the manifold pressure is too low, sooting and eventual
clogging of the heat exchanger could occur.
5. Once the correct gas pressure to the burners has been
established, turn the gas valve knob to OFF and turn the
electrical supply switch OFF; then, remove the pressure
tap at the gas valve and re-install the plug using a com-
pound (on the threads) resistant to the action of LP gases.
6. Turn the electrical and gas supplies back on, and, with the
burners in operation, check for gas leakage around the
plug with a soap and water solution.
WARNING: Be sure that the gas valve pressure regulator cap
is replaced.
ADJUSTMENT OF TEMPERATURE RISE
The temperature rise, or temperature difference between the
return air and the heated air from the furnace, must be within
the range shown on the furnace rating plate and within the
application limitations shown in Table 1. After the temperature
rise has been determined, the cfm can be calculated.
After about 20 minutes of operation, determine the furnace
temperature rise. Take readings of both the return air and the
heated air in the ducts, about six feet from the furnace where
they will not be affected by radiant heat.
Increase the blower speed to decrease the temperature rise;
decrease the blower speed to increase the rise.
All direct-drive blowers have multi-speed motors. The blower
motor speed taps are located in the control box in the blower
compartment. Refer to Figure 15 and the unit wiring label to
change the blower speed.
You may select a heating speed and a cooling speed. They may
be the same speed or a different speed.
To use the same speed tap for heating and cooling, the "heat"
terminal and "cool" terminal must be connected using a jumper
wire and connected to the desired motor lead. Place all unused
motor leads on "Park" terminals. Two are provided.
CAUTION: Do not energize more than one motor speed at a
time or damage will result.
ADJUSTMENT OF FAN-OFF CONTROL SETTINGS
This furnace is equipped with a time on/time off heating fan
control. The fan "on" is fixed at 30 seconds. The fan "off" is field
adjustable from 60 to 180 seconds. The fan "off" is factory set
to 60 seconds.
The fan-off setting must be long enough to adequately cool the
furnace, but not so long that cold air is blown into the heated
space. The fan-off timing may be adjusted by setting the option
switches located (refer to Figure 15) on the control board as
follows:
ACCESSORY CONNECTIONS
The furnace control will allow power switching control of various
accessories. See Figure 16 for connection details.
Electronic Air Cleaner Connection
Two 1/4" spade terminals (AC and AC N) for electronic air
cleaner connections are located on the control board. The
terminals provide 120 VAC (1.0 amp maximum) during circu-
lating blower operation.
Humidifier Connection
Two 1/4" spade terminals (HUM and HUM N) for humidifier
connections are located on the control board. The terminals
provide 120 VAC (1.0 amp maximum) during heat speed
operation of the circulating blower.
COOL
HEAT
PARK
PARK
XFMR
LINE
HUM
EAC
XFMR
EAC
LINE
CIR
HUM
120 VOLT
ELECTRONIC
AIR CLEANER
EAC HOT
HUM HOT
BLK
BLK
WHI
WHI
120 VOLT
HUMIDIFIER
FIGURE 16 - ACCESSORY CONNECTIONS
COOL
HEAT
PARK
XM
BLK - HIGH SPEED
BLU - MEDIUM SPEED
RED - LOW SPEED
BLK
BLU
RED
MOTOR LEADS
FAN OFF
ADJUSTMENT
SWITCHES
ON
OFF
1
2
LINE
PARK
FIGURE 15 - TYPICAL HEAT/COOL SPEED TAP
CONNECTIONS
To Delay Fan-Off By:
Set Switch
1 2
60 Sec.
On On
90 Sec.
On Off
120
Sec.
Off On
180
Sec.
Off Off
650.69-N3
Unitary Products Group
13