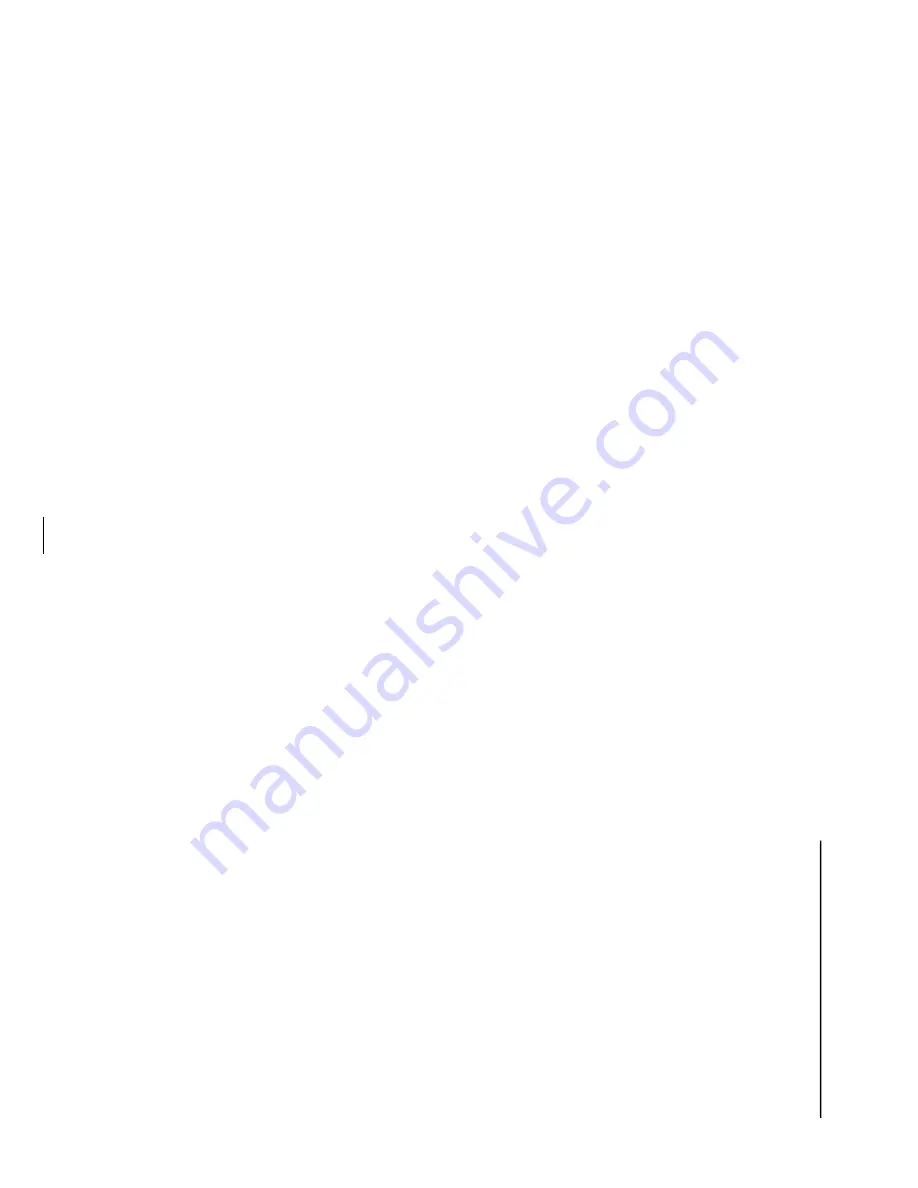
JOHNSON CONTROLS
136
FORM 160.78-O2
ISSUE DATE: 5/22/2017
SECTION 3 - VSD OPERATION
light weight solution by replacing heavy copper or alu-
minum cooling blocks, while providing direct liquid
cooling for the rectifier and inverter IGBT’s. They also
provide a method for mounting the IGBT assemblies to
the bus capacitor within the power unit.
The power unit contains all of the items needed for the
output of the OSCD in a highly integrated, but modular
design. The bus capacitor is the core of the assembly.
All of the other items are attached to the bus capaci-
tor. On top of the bus capacitor is the laminated bus
structure and the gate driver board. The rectifier and
inverter assemblies are attached to each side of the bus
capacitor. The rectifier or inverter assemblies can be
replaced in the field.
Ease of maintenance is provided by using the com-
munications link between the OptiView panel and the
OSCD. The cooling pumps and fans can be turned on
from the OptiView panel. This provides for a safer an-
nual coolant changes. The gate driver test is also start-
ed from the OptiView panel.
OPTISPEED COMPRESSOR DRIVE DETAILS
(490 AND 744 AMP DRIVES)
An electronic circuit breaker or disconnect switch con-
nects the three phase input power to input fuses and
then onto the AC line inductor, and input filter. Three
phase power continues onto the rectifier IGBT’s to the
bus capacitor to the inverter, then onto the output filter
and the compressor motor.
The AC line inductor provides isolation between the 3
phase power source and the input to the drive. The AC
line inductor improves the input current waveform so
that it appears more like a sine wave. The input filter
reduces the effects of the high frequency switching of
the rectifier and provides the inductance for boosting
the bus voltage above the peak of the line voltage.
The higher bus voltage is required for harmonic current
correction at the input of the OSCD, and to provide the
correct output voltage for high speed operation of the
compressor motor.
The AC to DC rectifier uses several power devices.
Each phase has one or more modules arranged in a par-
allel connection depending on the amount of input cur-
rent required. Each rectifier module contains 3 power
devices that are called the Upper, Lower, and Aux. de-
vice. All three devices are required to rectify and boost
the 3 phase input AC voltage into DC voltage in a mod-
ified new three-phase bridge configuration. The use of
the modified new three-phase bridge configuration in
the rectifier permits pre-charge of the DC bus filter
capacitors when the chiller enters the start mode, and
provides a fast disconnect from the AC line when the
chiller enters the stopped mode. This new bridge con-
figuration also provides the harmonic filtering without
the need of separate power unit, precharge circuit, and
control board.
The DC to AC inverter also uses several power devic-
es. Each phase has one or more modules arranged in a
parallel connection depending on the amount of output
current required. Each inverter module contains an Up-
per and Lower device. The Aux. device is not need in
the inverter.
The permanent magnet motor used on the YMC
2
chiller
requires a near sine wave of voltage. Typically, drives
provide a pulse of voltage at the amplitude of the bus
voltage for a varying period of time. This waveform
is typically known as a square wave. This OSCD con-
tains a direct water cooled output filter.
A new drive logic board was designed to provide all
of the logic required to turn on and turn off all of the
power devices, turn on and off the cooling fans and
pumps, evaluate data from the input and output current
sensors, evaluate data about the input and output volt-
age, and communicated to the OptiView panel.
Other sensors and boards are used to convey informa-
tion back to the OSCD Logic board, and provide safe
operation of the OSCD. Each power module contains
a temperature sensor that provides temperature infor-
mation back to the OSCD logic board. Three Current
Transformers monitor the output current from the
OSCD power unit and are used to protect the drive and
motor from overcurrent conditions. Another 3 Current
Transformers monitor the input current to the OSCD to
provide current limit, and harmonic current filtering.
OPTISPEED COMPRESSOR DRIVE DETAILS
(0490A AMP DRIVE)
The 0490A amp drive has the same basic function as
the 490 and 744 amp drives, but the precharge of the
drive is different.
The precharge is now completed through a precharge
and supply contactor, which are control by the drive
logic board. During the precharge period the drive log-
ic board will command the precharge contactor to close
for 12 seconds. During this time, the voltage will in-
crease across the bus capacitors, and the current will be
limited by the precharge resistors. This 12 second pe-
riod is called the precharge time. After 12 seconds has