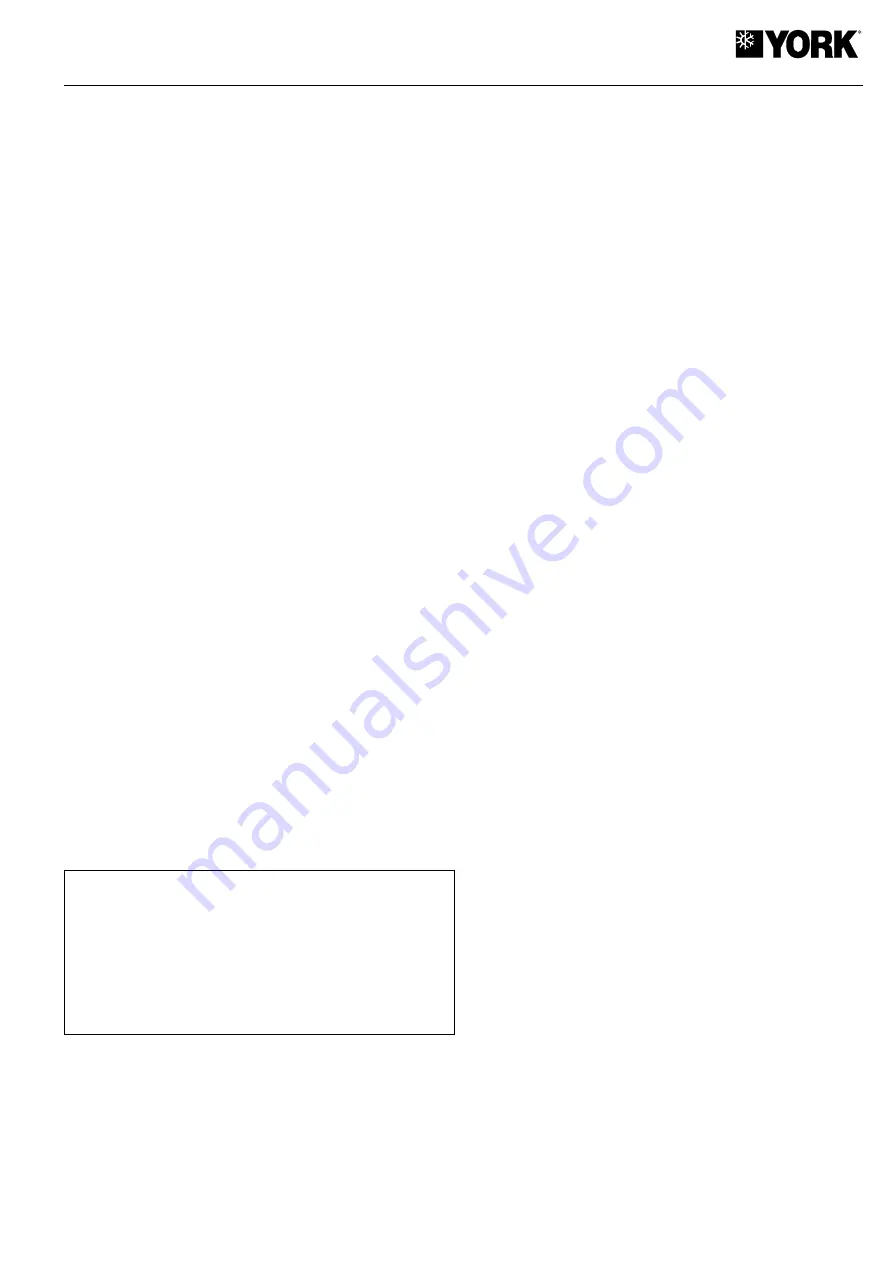
5
17.3.- Low gas pressure (models D4IG)
If gas supply pressure falls below the gas pressure switch
(GS) set point, power supply to the ignition control circuit is
cut off, and this circuit becomes inoperative. The gas equip-
ment will reset automatically once the gas supply pressure
goes above the pressure switch set point, and the start-up
sequence will begin once again. See table 18.6 for gas valve
and thermal switch adjustments.
17.4.- Heating lock-out (electric heaters)
Should any of the electric heater phases not operate, check
heat protection devices F12 and F15 (105° C, manual re-
set heat switch). If F1 or F16 (77° C, automatic reset) fail
three times, the control board will detect this, turn off the
corresponding heater and display the failure on thermostat
DPC-1.
Also check short circuit and overload protection automatic
switches F21 and F22 (1
st
and 2
nd
stages). The heat switches
and automatic switches can be accessed through the external
access panel of the electric heater.
17.5.- Motor overload protection
All motors of the hermetic compressors and fan motors are
protected against overloads by
means of an internal heat line cut-off switch. This protection
will reset automatically once the motor has cooled off suf-
ficiently. Externally, they are protected against short circuits
and overloads by means of automatic switches, curve K (DIN,
VDE 0660-104).
The indoor fan motor is protected by a motor-guard, adjusted
to the maximum amperage of the fan motor. In the case of
excessive power consumption in the three phases, the mo-
tor-guard opens, interrupting the electric power supply to the
Indoor Fan Contactor.
The motor-guard auxiliary contact opens and the control
board detects this, turns the entire unit off and displays the
failure on thermostat DPC-1.
18- Start-up of gas heating, models
D4IG
1. Check the type of gas to be used. Make sure it is the same
as shown on the identification plate located on the burner
assembly access door.
2. Make sure both the combustion air intake and the gas
discharge have no obstructions.
. Make sure the gas supply line is in compliance with safety
regulations and is prepared to supply adequate gas flow
and pressure. (See technical specifications in sections
4.1 and 18.8.)
Gas supply pipes to the unit must be air purged
18.2.- Turning on
This burner is equipped with automatic ignition systems.
Do not attempt to ignite it manually.
18.3.- Start-up, without the YKTOOL portable
test tool (accessory)
1. Connect power supply to the unit.
2. Open the gas supply tap to the unit.
. Set the ambient thermostat to its maximum temperature
in heat.
4. The burner assembly will ignite. (It could take a few
minutes, depending upon the mode established on the
thermostat.)
18.4.- Start-up, with YKTOOL (accessory)
1. Disconnect power supply to the unit.
2. Set the Yktool on connector J9 of the Yklon board A1.
. Connect power supply to the unit.
4. Open the gas supply tap to the unit.
5. On the main menu, select Test heat (No. 7). Select
Auxiliary 1 and activate (ON). Repeat with Auxiliary 2,
and 4.
6. The 4 stages of the burner assembly will go on.
18.5.- Check list after start-up
After having activated the entire control circuit and the gas
heating is in operation, check the following:
1. Make sure there are no leaks in the unit and supply
pipes.
2. Check gas supply pressure with all gas units in the build-
ing operating at full capacity.
In no case should the pressure in the gas auxiliary line
above 25 mbar, nor the incoming pressure in the burner
assembly below 12.5 mbar.
. Make sure the gas pressures in the manifold are correct.
(See section 18.6 and Fig. 18.)
4. Visually check the flame at the burners (Fig. 19).
5. Using a combustion gas analyzer, check the CO and CO
2
content at both smoke discharges.
With the 4 heat stages in operation, the carbon monoxide
(CO) content should be below 0.1% (1000 ppm), and the
CO/CO
2
ratio should be below 0.02.
Caution:
To avoid possible damage to the gas valves,
the burner assembly of the unit should be disconnected
from the gas pipe system during the pressure test of said
system.
All work on the gas system must be carried out by qualified
personnel only.
18.1.- Check list prior to start-up
Caution:
Prior to this operation, make sure unit impulse air
flow is correct, in accordance with the minimum flow stipu-
lated in the technical specifications in section 4.1.
Summary of Contents for D4IC-360
Page 2: ......
Page 43: ...43 20 Wiring diagrams 20 1 Cool only models D4IC 360 D4IC 360G50 400 3 50 1 of 3 ...
Page 44: ...44 D4IC 360G50 400 3 50 2 of 3 ...
Page 45: ...45 D4IC 360G50 400 3 50 3 of 3 ...
Page 46: ...46 20 2 Cool only models D4IC 480 D4IC 480G50 400 3 50 1 of 3 ...
Page 47: ...47 D4IC 480G50 400 3 50 2 of 3 ...
Page 48: ...48 D4IC 480G50 400 3 50 3 of 3 ...
Page 49: ...49 20 3 Heat pump models B4IH 360 400 3 50 1 of 3 ...
Page 50: ...50 B4IH 360 400 3 50 2 of 3 ...
Page 51: ...51 B4IH 360 400 3 50 3 of 3 ...
Page 52: ...52 20 4 Heat pump models B4IH 480 400 3 50 1 of 3 ...
Page 53: ...53 B4IH 480 400 3 50 2 of 3 ...
Page 54: ...54 B4IH 480 400 3 50 3 of 3 ...
Page 55: ...55 20 5 Cool only gas heating models D4IG 360 400 3 50 1 of 4 ...
Page 56: ...56 D4IG 360 400 3 50 2 of 4 ...
Page 57: ...57 D4IG 360 400 3 50 3 of 4 ...
Page 58: ...58 D4IG 360 400 3 50 4 of 4 ...
Page 59: ...59 20 5 Cool only gas heating models D4IG 480 400 3 50 1 of 4 ...
Page 60: ...60 D4IG 480 400 3 50 2 of 4 ...
Page 61: ...61 D4IG 480 400 3 50 3 of 4 ...
Page 62: ...62 D4IG 480 400 3 50 4 of 4 ...
Page 63: ...63 Configuration of switches Data and dimensions are subject to change without prior notice ...
Page 64: ...www johnsoncontrols com ...