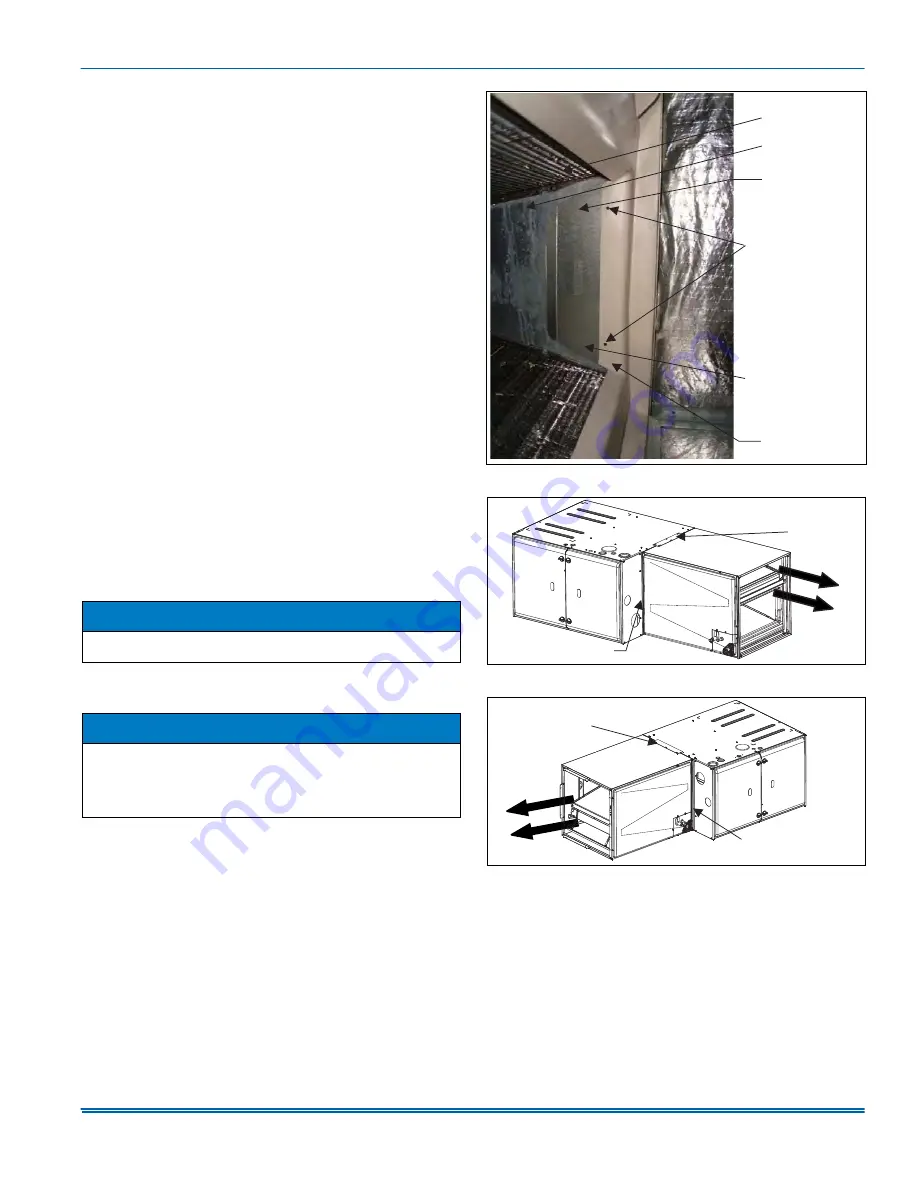
5292154-UIM-A-0317
Johnson Controls Unitary Products
5
Upflow or downflow applications (CF/CM Models):
These coils are factory shipped for installation in either upflow or down-
flow applications with a minor conversion.
1.
Position the coil cabinet on the furnace or modular air handler
opening (or the coil cabinet under the furnace or modular air han-
dler opening for appropriate air flow) as shown in Figure 5 or 6.
2.
Use the three tie plates and screws (included in bag with coil) to
secure the coil cabinet to the furnace or modular air handler.
3.
Seal mating surfaces to prevent air leakage between the coil cabi-
net and the furnace or modular air handler.
4.
Place the three duct flanges (from bag with coil) in mounting posi-
tions of the upper air flow opening on the coil, and secure with
screws from the bag as shown in Figure 4.
5.
See sections on “Refrigerant Line Connections” and “Condensate
Drain Connections” for further installation instruction.
Horizontal applications (CM Models only):
CM model coils are supplied ready to be installed in a horizontal left
position. A horizontal drain pan is factory installed. If horizontal right
application, refer to the horizontal right conversion before proceeding.
1.
Position the coil cabinet against the furnace or modular air handler
opening as shown in Figure 8, 9, 11, or 12.
2.
Use the three tie plates and screws (included in bag with coil) to
secure the coil cabinet to the furnace or modular air handler.
3.
Seal mating surfaces to prevent air leakage between the coil cabi-
net and the furnace or modular air handler.
4.
Install the three duct flanges with screws (from bag with coil) in
positions shown in Figure 4.
5.
See sections on “Refrigerant Line Connections” and “Condensate
Drain Connections” for further installation instruction.
Horizontal right conversion (CM Models only):
1.
Remove coil access panel.
2.
Slide coil/drain pan assembly out of coil cabinet.
3.
Install the front and the back coil blow off wings (apply only to “N”
coils) in accordance with the following:
a.
Locate 4 screws (2 front side and 2 back side) securing the
coil delta plates to the coil drain pan.
b.
Loosen each screw.
c.
Slide each coil blow off wing between the drain pan and the
coil delta plate.
d.
Tighten screw to secure coil blow off wings. See Figure 7.
4.
Slide the coil back into the cabinet. Be sure to engage the side coil
slide into the slide rail on the coil cabinet.
5.
Install coil access panel. The horizontal right conversion is now
complete. Return to and accomplish the horizontal application
installation.
SECTION IV: DIRECT DUCT
INSTALLATION (CF MODELS)
In cases where the coil is being removed from the provided casing and
installed directly into the ductwork, the shroud (a Source 1 part), must
be installed. The top right blow off shield is removed, and the shroud is
installed by attaching it to the top of the coil and to the front and aft seal
plates. See Figure 10 for details.
NOTICE
Convert coil to correct orientation prior to installation. Conversion
must be made before brazing the refrigerant connections to the coil.
NOTICE
When installing a coil blow off wing, make sure that each notch in the
coil blow off wing slides around the anchor screw with the bottom of
the notch fully set against the screw.
Ensure that coil blow off wing is installed with the flange bending
away from the coil delta plate. blow off wings only apply to “N” coils.
FIGURE 7:
Coil Blow Off Wing Installation
FIGURE 8:
CM Horizontal Right Application with Furnace
FIGURE 9:
CM Horizontal Left Application with Furnace
,167$//&2,/%/2:
2)):,1*21)5217
$1'%$&.2)&2,/
&2,/
'(/7$3/$7(
'5$,13$1
6&5(:6
SHUEORZRIIZLQJ
%/2:2)):,1*
$
)851$&(
&2,/
$
7,(3/$7(
75$16,7,21$1*/(
)851$&(
&2,/
$
7,(3/$7(
75$16,7,21$1*/(