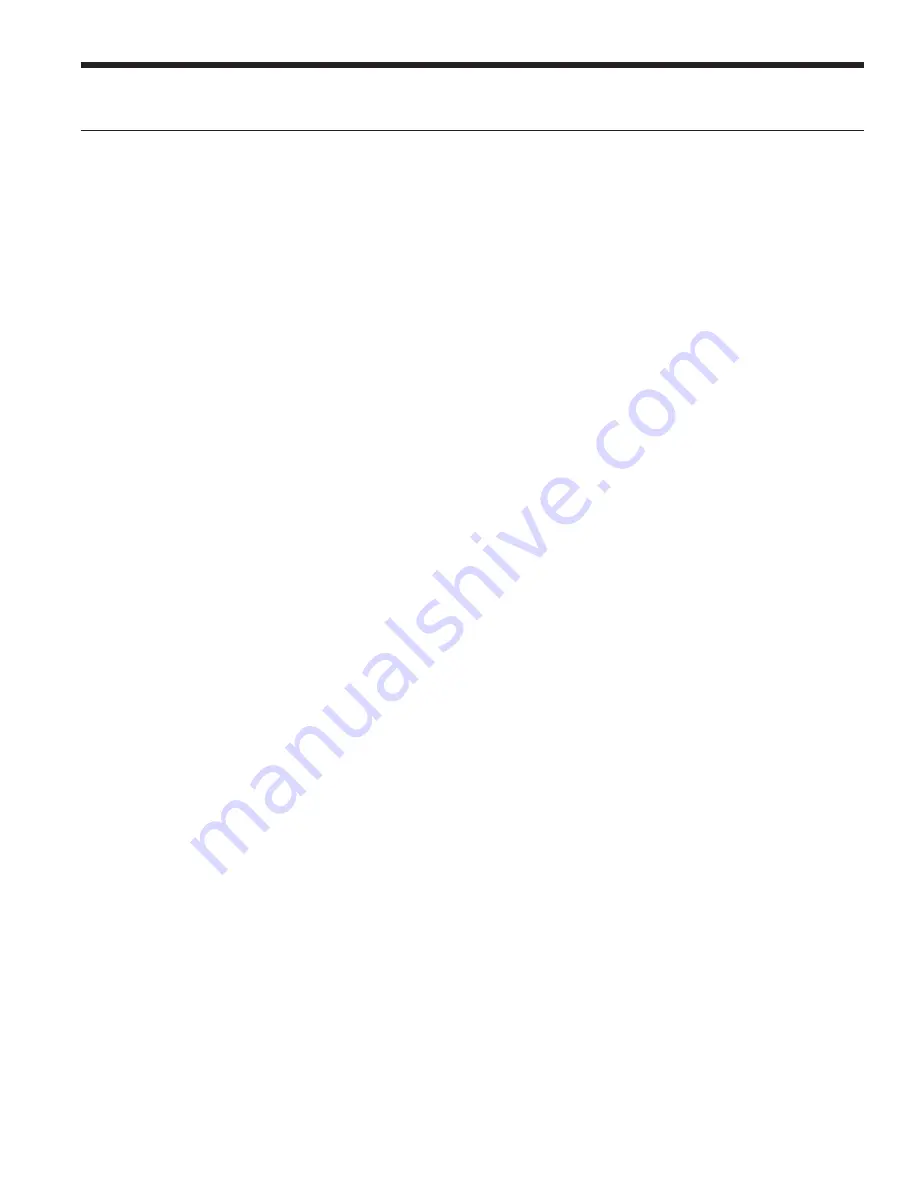
25
Unit Startup cont.
f. Energy monitoring can be read on any of the
following
components:
i. AID Tool – instantaneous information only
ii. Symphony Web Portal via AWL
device connected to Aurora (if available)
Performance and Refrigerant Monitoring (optional
sensor kit)
The optional Performance and Refrigeration Monitoring
Kits includes a pressure sensor, temperature sensors, and
a source side water flow rate rensor. The temperature
sensors monitor entering and leaving source, leaving load
water, heating liquid line and existing cooling liquid line
(FP1). The pressure sensor monitors the system’s discharge
pressure. With this kit, heat of extraction and rejection will
be calculated. This requires configuration using the AID
Tool for selection of water or antifreeze. These sensors
also allow for the subcooling to be displayed on the AID
Tool or Symphony via AWL (if available).
NOTE: Superheat
displayed on the AID Tool is not true superheat, it is the
superheat of the vapor injection circuit.
Ensure the Performance and Refrigeration Kit has been
enabled by accessing the “Sensor Kit Setup” in the AID Tool
and complete the following:
a. Select “Brine” - and then choose Water or Antifreeze for
the proper factor.
b. Select “Flow Meter” - to activate the flow sensor choose
1
in.
c. Turn on the Unit in Heating or Cooling.
d. Use the AID Tool to view the refrigerant performance in
the “Refrigerant Monitor” screen.
e. Use the AID Tool to view the performance in the
“Performance Monitor” screen.
f.
Performance and Refrigerant monitoring can be read on
any of the following components:
i.
AID Tool - Instansaneous information only
ii.
Symphony Web Portal via AWL device
connected to Aurora. (If available)
Configuring the Sensor Kits
Configuring the Sensor kits
The Aurora Advanced Control allows Refrigeration, Energy,
and Performance Monitoring sensor kits. These kits can be
factory or field installed. The following description is for
field activation of a factory installation of the sensor kits.
Energy Monitoring (Standard Sensor Kit)
The Energy Monitoring Kit includes two current transducers
(load pump and electric heat) and two compressor sensors
so that the complete power usage of the heat pump
can be measured. The AID Tool provides a line voltage
calibration procedure to improve accuracy. This information
can be displayed on the AID Tool or Symphony via AWL
(if available). Ensure the Energy Kit has been enabled
by accessing the ‘Sensor Kit Setup” in the AID Tool and
complete the following:
a. Activate ‘Energy Option’ to activate the sensors
for compressor (2), load pump and aux heat current.
b. Select ‘Pump’ option of FC1, FC2, or open loop.
Select ‘Open Loop’ if this heat pump is linked to a
flow center through another heat pump.
This selects the pump watts used in the calculation.
Source pump watts are not measured but
estimated.
c. Line Voltage Calibration – Voltmeter required to
calibrate line voltage during heating or cooling.
Refer to Line Voltage Calibration in this manual for
more
details.
i. Turn on Unit in Heating or Cooling .
ii. Use multimeter at L1 and L2 to measure
line
voltage
iii. In the Sensor Kit Setup screen adjust the
‘Base Voltage’ to the nearest value to that
is
measured
iv. Then use the ‘Fine Adjust’ to select the
exact voltage being measured at L1 and L2.
v. Exit ‘Sensor Setup’ Screen
e. Power Adjustment: Refer to the Power Adjustment
tables in the Aurora ‘Advanced’ Control section of
the
literature
i. On the Main Menu screen select Setup
ii. Once in the Setup menu select the Power
Adjustment
Factor
iii. Power Adjustment - allows you to enter
the unit’s compressor power setting for
high and low speed operation.
Refer to the tables and use the voltage
that is closest to the unit’s line
voltage and set the power adjustment
accordingly.
AFFINITY SINGLE STAGE HYDRONIC WITH OPTIHEAT INSTALLATION MANUAL
Summary of Contents for AFFINITY OptiHeat YAW040
Page 2: ......
Page 51: ...51 Notes AFFINITY SINGLE STAGE HYDRONIC WITH OPTIHEAT INSTALLATION MANUAL...
Page 52: ......