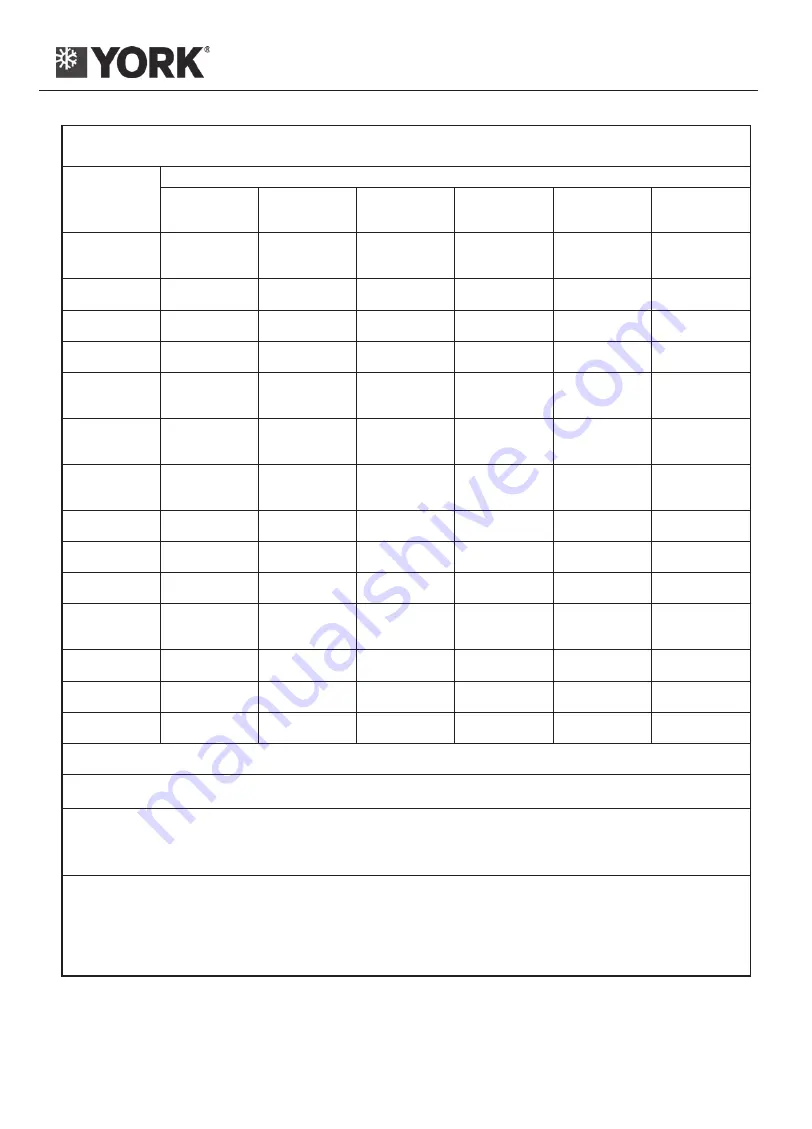
83
Content of Toxic and Harmful Substances
Component
Name
Toxic or Hazardous Substance or Element
Lead (
Pb
)
Mercury
(Hg)
Cadmium
(
Cd
)
Hexavalent
Chromium
(Cr (VI))
Polybrominated
Biphenyl
(PBB)
Polybrominated
Diphenyl Ether
(PBDE)
Compressor
and Its
Accessories
×
○
○
○
○
○
Sheet Metal
Parts
○
○
○
×
○
○
Valve
×
○
○
○
○
○
Crankcase’s
Heating Belt
○
○
○
○
○
○
Fasteners Such
as Screws and
Bolts
×
○
○
×
○
○
Controller and
Electrical
Components
×
○
○
○
○
○
Water Side
Heat
Exchanger
○
○
○
○
○
○
Pipeline
Component
○
○
○
○
○
○
Rubber Parts
○
○
○
○
○
○
Refrigerant
○
○
○
○
○
○
Heat
Preservation
Cotton
○
○
○
○
○
○
Plastic Parts
○
○
○
○
○
○
Foam
○
○
○
○
○
○
Printing Parts
○
○
○
○
○
○
This table is prepared in accordance with the provisions of SJ/T11364
○: It indicates that the content of the toxic and harmful substance in all homogeneous materials of the component is
below the limit specified in GB/T26572.
×: It is indicated that the content of the toxic and harmful substance exceeds the limit specified in GB/T26572 at
least in one homogeneous material of the component. The components marked with “×” in the table cannot be
replaced at present due to the technical reasons, and it will be gradually improved as the development of the
technology subsequently .
1. After the product is scrapped, please separate it from the domestic garbage, and the consumer has the
responsibility to send it to the qualified recovery station;
2. The recovery and treatment center will recover and reuse the material in the product through appropriate method;
3. Please consult the local government, scrap disposal center or the local distributor for the details of this product's
recovery processing;
4. The environmental protection period of the product is not equivalent to the product’s safety service life.
Content of Toxic and Harmful Substances
Cooke Industries - Phone: +64 9 579 2185 Email: [email protected] Web: www.cookeindustries.co.nz