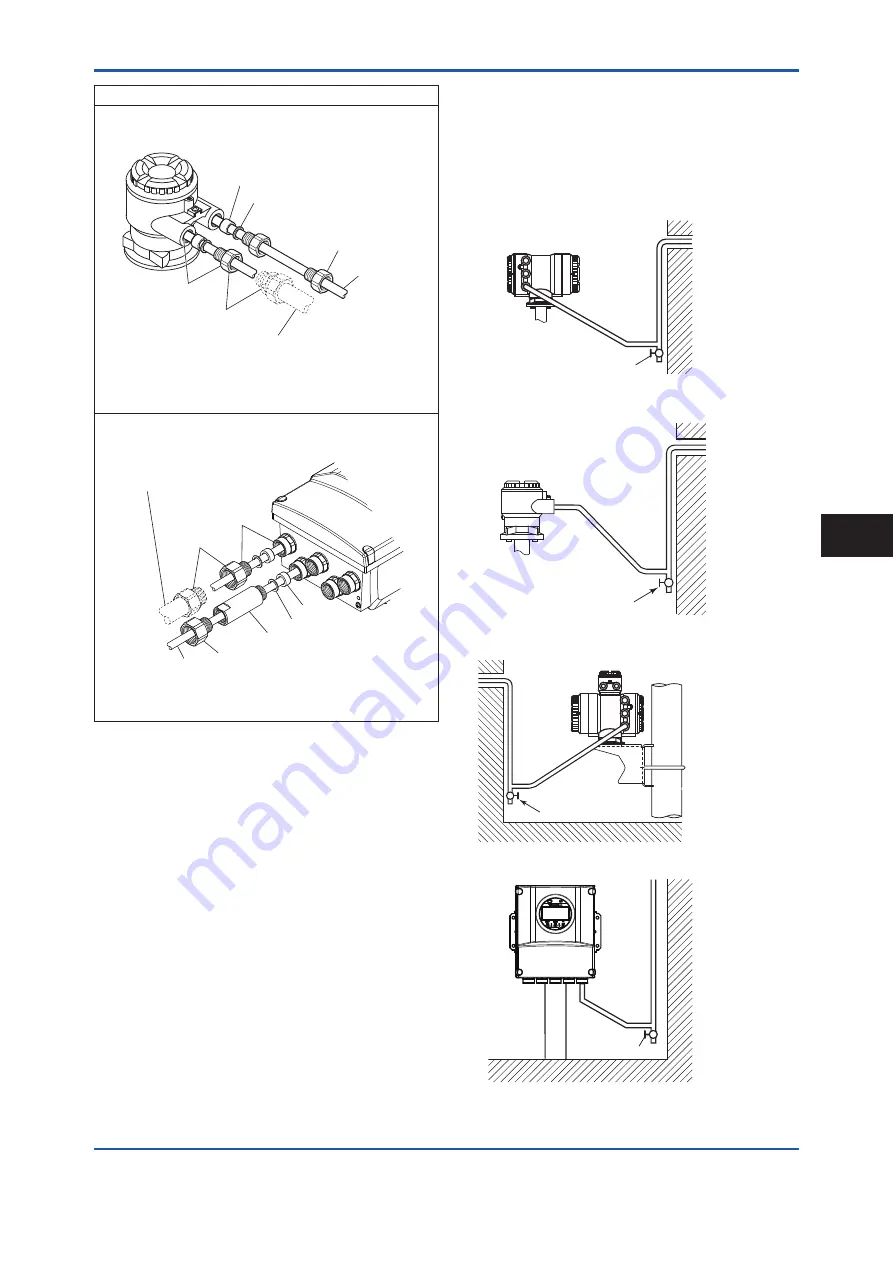
<4. Wiring>
29
IM 01E25A01-01EN
(4) Waterproof Gland with JIS G3/4 Female
Remote Sensor
Optional code: EW
Gasket
Washer
* When connecting G1/2, remove the conversion plug and
connect directly to electrical connection.
Cable
G3/4
G1/2
Conversion plug (x2)*
F0416.ai
When working on conduit or flexible tube (G3/4)
Remote Transmitter (AXG1A/AXFA11)
Optional code: EW5 (AXG1A), EW (AXFA11)
Gasket
Washer
* When connecting G1/2, remove the conversion plug
and connect directly to electrical connection.
When working on conduit or
flexible tube (G3/4)
Extension plug (x2)
Cable
G3/4
G1/2
Conversion plug (x5)*
F0417.ai
4.3.2 Conduit Wiring
When wiring the conduits, utilize the waterproof gland to
prevent water from flowing in through the conduit. Place
the conduit pipe on an angle as shown in the following
figures.
Install a drain valve at the low end of the vertical pipe, and
open the valve regularly.
F0418.ai
Drain valve
Figure 4.3.1 Integral Flowmeter
Drain valve
F0419.ai
Figure 4.3.2 Remote Sensor
F0420.ai
Drain valve
Figure 4.3.3 Remote Transmitter (AXW4A)
F0421.ai
Drain valve
Figure 4.3.4 Remote Transmitter (AXG1A/AXFA11)
W
iring
4