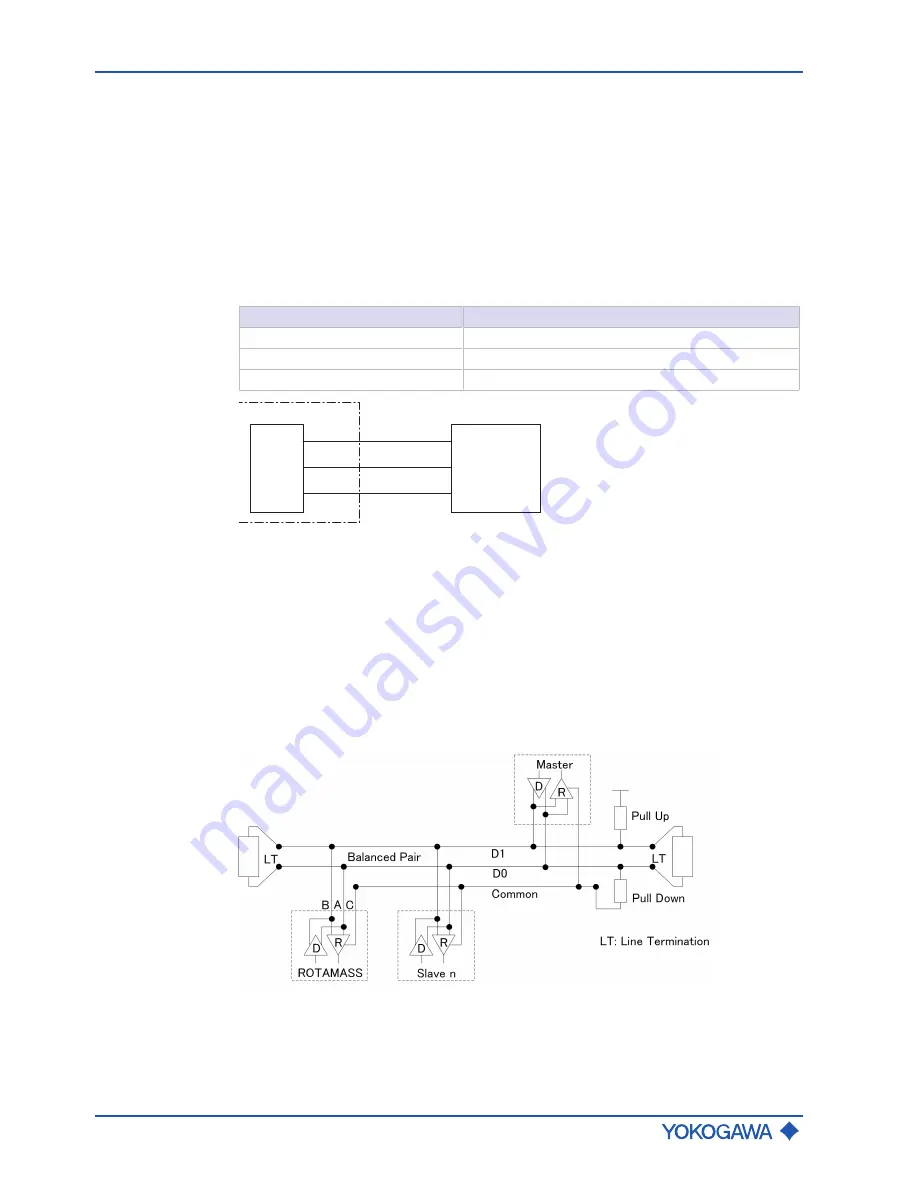
Quick Reference Instruction Manual
Wiring
Transmitter
36 / 54
IM01U10A00-00EN-R, 2nd edition, 2017-08-29
7.4.2 HART communication
For devices with HART communication, the HART interface, along with the analog signal,
is available at the output
Iout1
. A load resistance of 230 – 600 Ω at
Iout1
is recom-
mended.
How to connect to the communication tools is described in the applicable Software In-
struction Manual.
7.4.3 MODBUS communication
Modbus
interface
Modbus interface of Rotamass Total Insight is implemented in accordance with "MOD-
BUS over serial line specification and implementation guide V1.02", for details of instru-
mentation see website of the Modbus organization (http://www.modbus.org/).
Modbus
connections
Terminal
Description
I/O3 -
Modbus C (Common)
I/O4 +
Modbus B (D1)
I/O4 -
Modbus A (D0)
MODBUS_B
MODBUS_A
MODBUS_C
IO4+
IO4-
IO3-
RD+
RD-
GND
RS485
Modem
ROTAMASS
Fig. 21:
MODBUS communication
Modbus cable
3-Wire cable (twisted pair (D0, D1) and Common) with shield should be used. Wire gauge
should be AWG24 or wider.
Rotamass Total Insight has a RS485 electrical interface, operating in slave mode and
communicating with the following default specification:
Default Modbus
setting
▪ Modbus baud rate: 19200 bps
▪ Modbus transfer mode: RTU
▪ Modbus parity: Even
▪ Modbus stop bit: 1 stop bit
For further details, see applicable software instruction manual (SWIM).
Fig. 22:
Modbus connection