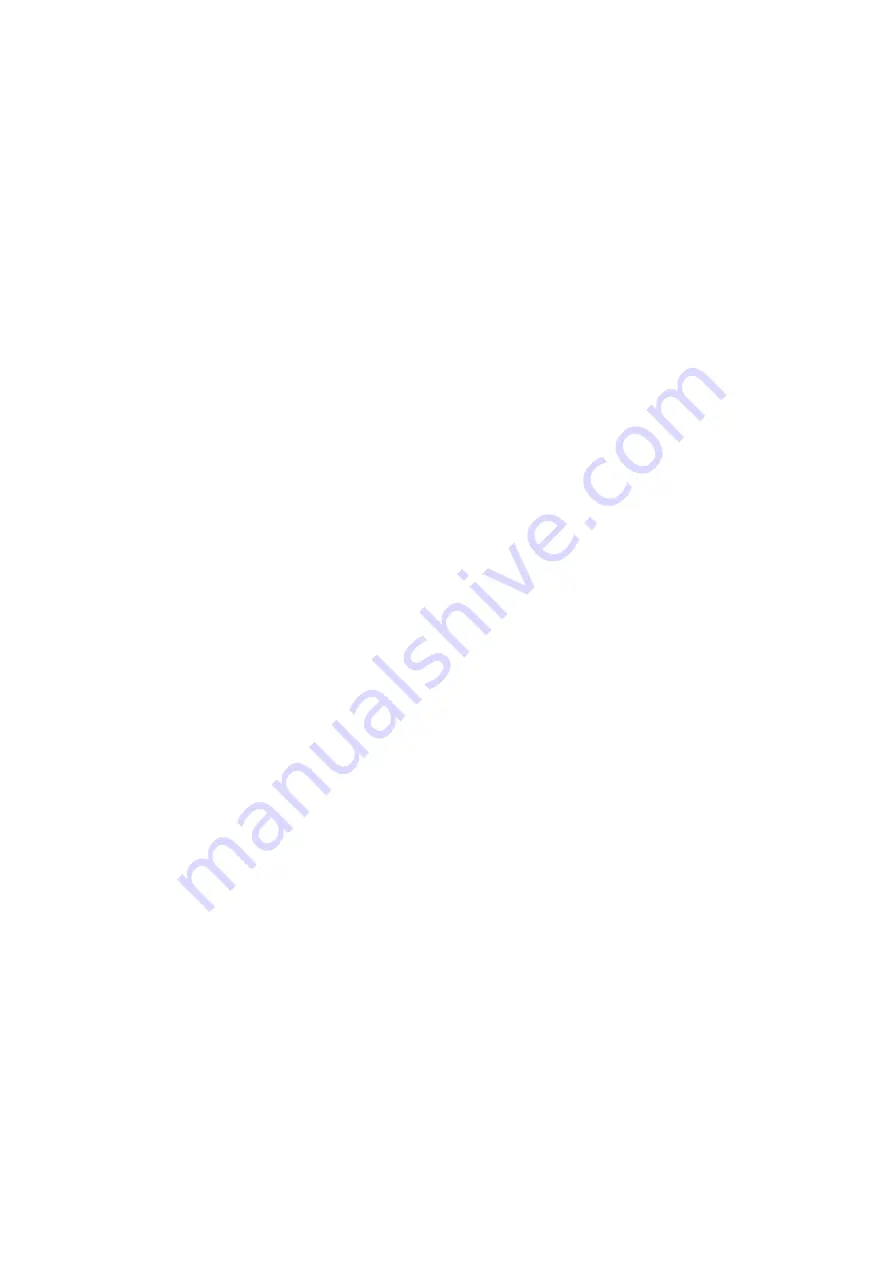
IM 12D08N04-01E
3-9
3. Installation and Wiring
3-4. Wiring the contact signals
3-4-1. General precautions
The contact output signals consist of voltage-free relay contacts for switching electrical
appliances (SPDT). They can also be used as digital outputs to signal processing
equipment (such as a controller or PLC). It is possible to use multi-core cables for the
contact in and output signals and shielded multi-core cable for the analog signals.
3-4-2. Contact outputs
The EXA unit’s four contact outputs can be wired to suit your own custom requirements
(Figure 3-6).
In the Non-Alarm or Power Off states, contacts S1, S2 and S3 are OFF, Common (C)
and Normally Closed (NC) are in contact.
In the “Fail” or Power Off states, contact S4 is ON, Common (C) and Normally Closed
(NC) are in contact.
You can either use them to switch AC power, or switch a DC Voltage for digital
interfacing.
Default settings
• The contact S1 is pre-programmed for high alarm function.
• The contact S2 is pre-programmed for a low alarm function.
• The contact S3 is not activated as an alarm (off).
• The contact S4 is pre-programmed for FAIL.
The three control contacts (S1 to S3) can be used for simple process control by program-
ming their function (Chapter 5). The FAIL contact is programmed to signal a fault in the
measuring loop. Always connect the FAIL contact to an alarm device such as a warning
light, sound annunciator, or alarm panel to make full use of the fault detection possibili-
ties (self diagnostics) of the EXA converter.
3-5. Wiring the analog output signals
3-5-1. General precautions
The analog output signals of the EXA transmit low power standard industry signals to
peripherals like control systems or strip-chart recorders (Figure 3-6).
3-5-2. Analog output signals
The output signals consist of active current signals of either 0-20 mA or 4-20 mA. The
maximum load can be 600 ohms on each.
It is necessary to use screening/shielding on the output signal cables. Terminal 63 is
used to connect the shielding.