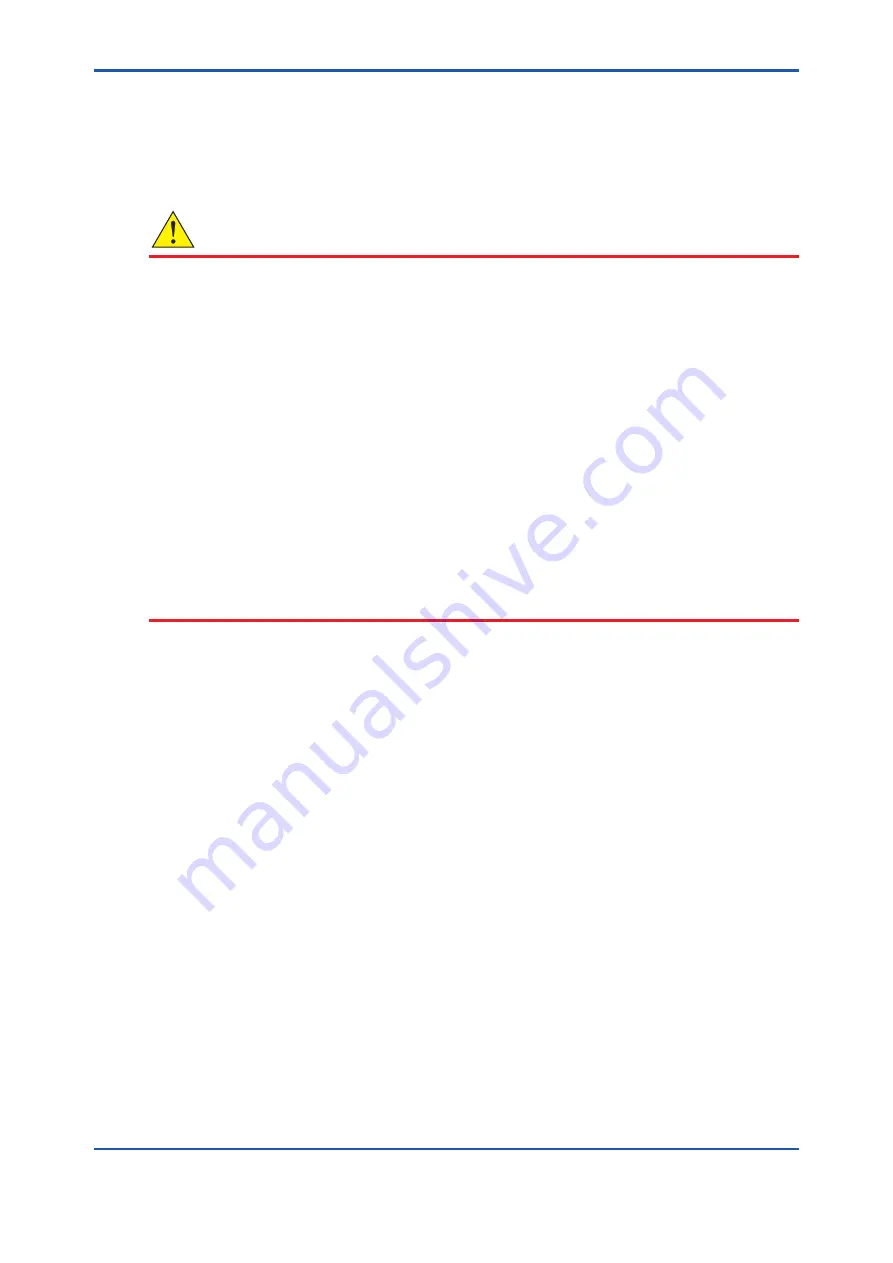
<1. Overview>
1-1
IM 11M10A01-01E
1. Overview
1.1
Cautions Regarding Use
CAUTION
· This is a precision instrument; be careful not to drop it.
· Do not disassemble it, as it may stop operating normally.
· As far as possible, mount horizontally. Secure the sensor so that it can’t vibrate. Avoid
installing in places where the temperature exceeds 70°C.
· Do not mount this instrument in a place that is exposed to direct sunlight, or to direct
radiation from a furnace, boiler or the like, in a windy place, or in a location that is subject to
vibration.
· Avoid mounting in a location where there may be corrosive gases, gases other than the
measured gas, or organic silicon vapor.
· Where the furnace gas of a nitrogen reflow furnace contains organic solvent at a few ppm to
percentage level, the sensor should be used with the optional sampling system (K9424GA),
to avoid contact with the solvent.
· This instrument was designed to be resistant to electrical noise, but to avoid invalid readings
it would be wise to avoid using electrically noisy devices in the vicinity.
· The sensor is a consumable. Its life depends on usage and environment, but is about one
year.
· Be sure to keep this manual in a handy place when using this instrument.
1.2
Standard Specifications
Measured gas:
Measures O
2
in N
2
or mixed gases; can’t contain silicone vapor,
flammable gas or organic solvent.
Measuring principle: Current-limited Zirconia sensor
Measuring range:
0 to 1000 ppm O
2
, 0.1 to 25% O
2
(measuring range autoswitching)
Note: If you want an oxygen (concentration) control range of 0.2 to 0.5%,please consult with us, or your Yokogawa
salesperson or representative.
Sampling method:
Natural diffusion (direct input)
Linearity :
±5% of span (for 0-1000 ppm range, with O
2
being in the range 0 to 100
ppm). ±3% of span (for 0-1000 ppm range, with O
2
being in the range
100 to 1000 ppm). ±2% of span (for 0.1 to 25% range, with O
2
being in
the range 100 to 1000 ppm).
Repeatability :
±5% of span (for 0-1000 ppm range, withO
2
being in the range 0 to 100
ppm). ±2% of span (for 0-1000 ppm range, with O
2
being in the range
100 to 1000 ppm). ±2% of span (for 0.1 to 25% range, with O
2
being in
the range 100 to 1000 ppm).
Stability (Drift):
±2% of span per week.
Display:
LED digital display
Output signal:
4-20 mA DC isolated (measuring range: 0 to 1000 ppm or 0.1 to 25%).
Contact outputs (relay) : Closed if fail, contact rating 250 V AC / 3A
Closed if alarm, contact rating 250 V AC / 3A.
4th Edition : Oct. 23, 2019-00
Summary of Contents for OX100
Page 27: ...Blank Page...
Page 29: ...Blank Page 4th Edition Oct 23 2019 00...
Page 39: ......
Page 41: ...Blank Page...