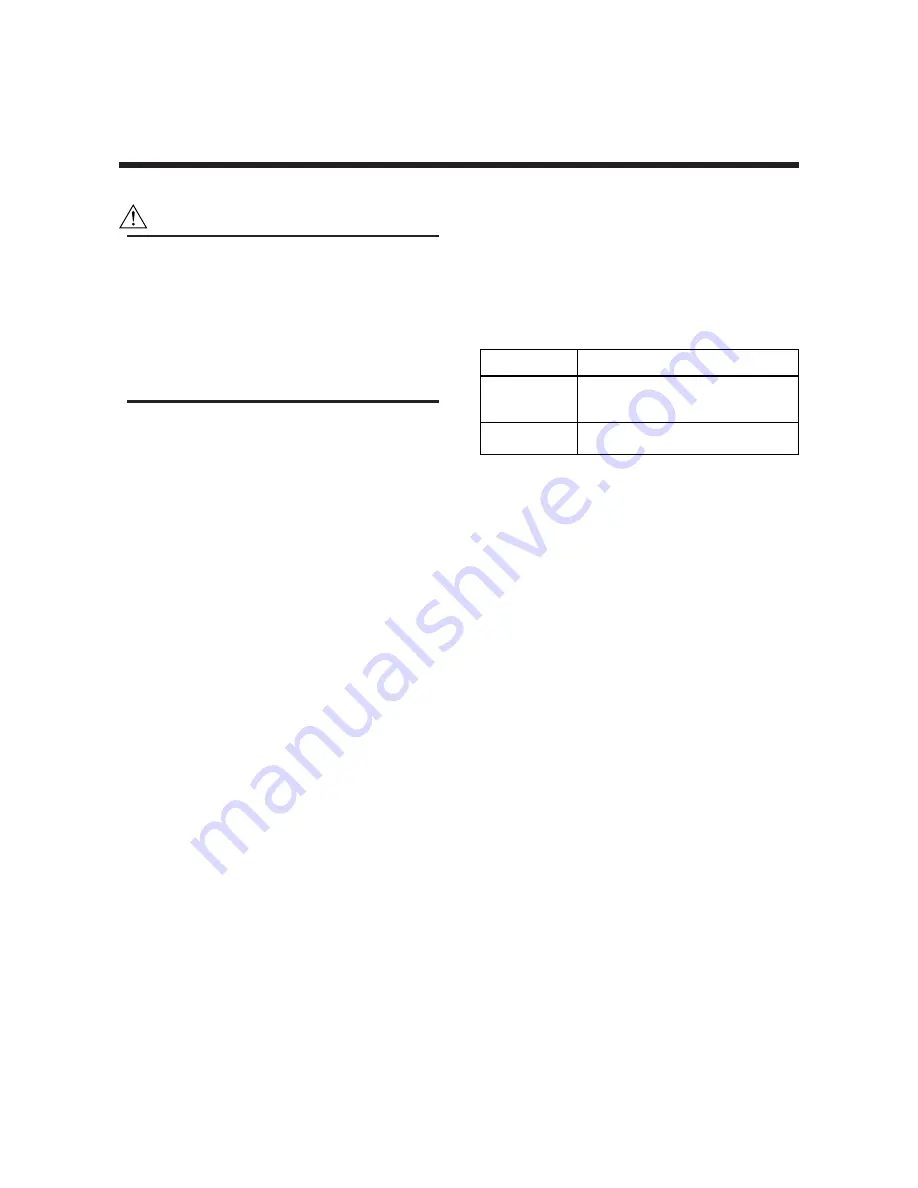
IM 01C25T03-01E
A-1
APPENDIX 1. SAFETY INSTRUMENTED SYSTEMS INSTALLATION
APPENDIX 1. SAFETY INSTRUMENTED
SYSTEMS INSTALLATION
WARNING
The contents of this appendix are cited from
exida.com safety manual on the EJX series
pressure transmitters specifically observed for
the safety transmitter purpose. When using the
EJX for Safety Instrumented Systems (SIS)
application, the instructions and procedures in
this section must be strictly followed in order to
preserve the transmitter for that safety level.
A1.1 Scope and Purpose
This section provides an overview of the user responsi-
bilities for installation and operation of the EJX in
order to maintain the designed safety level for Safety
Instrumented Systems (SIS) applications. Items that
will be addressed are proof testing, repair and replace-
ment of the transmitter, reliability data, lifetime,
environmental and application limits, and parameter
settings.
A1.2 Using the EJX for an SIS
Application
A1.2.1 Safety Accuracy
The EJX has a specified safety accuracy of 2%. This
means that the internal component failures are listed in
the device failure rate if they will cause an error of 2%
or greater.
A1.2.2 Diagnostic Response Time
The EJX will report an internal failure within 5
seconds of the fault occurrence.
A1.2.3 Setup
During installation the transmitter must be setup with
engineering units parameters. This is typically done
with a handheld terminal. These parameters must be
verified during the installation to insure that the correct
parameters are in the transmitter. Engineering range
parameters can be verified by reading these parameters
from the optional local display or by checking actual
calibration of the transmitter.
The calibration of the transmitter must be performed
after parameters are set.
A1.2.4 Required Parameter Settings
The following parameters need to be set in order to
maintain the designed safety integrity.
Table A1.2.4 Required Parameter Settings
Burnout direction
switch
To specify if the output should go 21.6
mA or higher or 3.6 mA or lower upon
detection of an internal failure.
Item
Description
The write function should be disabled.
TA0101.EPS
Write protection
switch
A1.2.5 Proof Testing
The objective of proof testing is to detect failures
within the transmitter that are not detected by the
diagnostics of the transmitter. Of main concern are
undetected failures that prevent the safety instrumented
function from performing its intended function. See
table A1.2.5 for proof testing method.
The frequency of the proof tests (or the proof test
interval) is to be determined in the reliability calcula-
tions for the safety instrumented functions for which
the EJX is applied. The actual proof tests must be
performed more frequently or as frequently as specified
in the calculation in order to maintain required safety
integrity of the safety instrumented function.
The following tests need to be specifically executed
when a proof test is performed. The results of the proof
test need to be documented and this documentation
should be part of a plant safety management system.
Failures that are detected should be reported to
Yokogawa.
The personnel performing the proof test of the trans-
mitter should be trained in SIS operations including
bypass procedures, EJX transmitter maintenance, and
company management of change procedures.