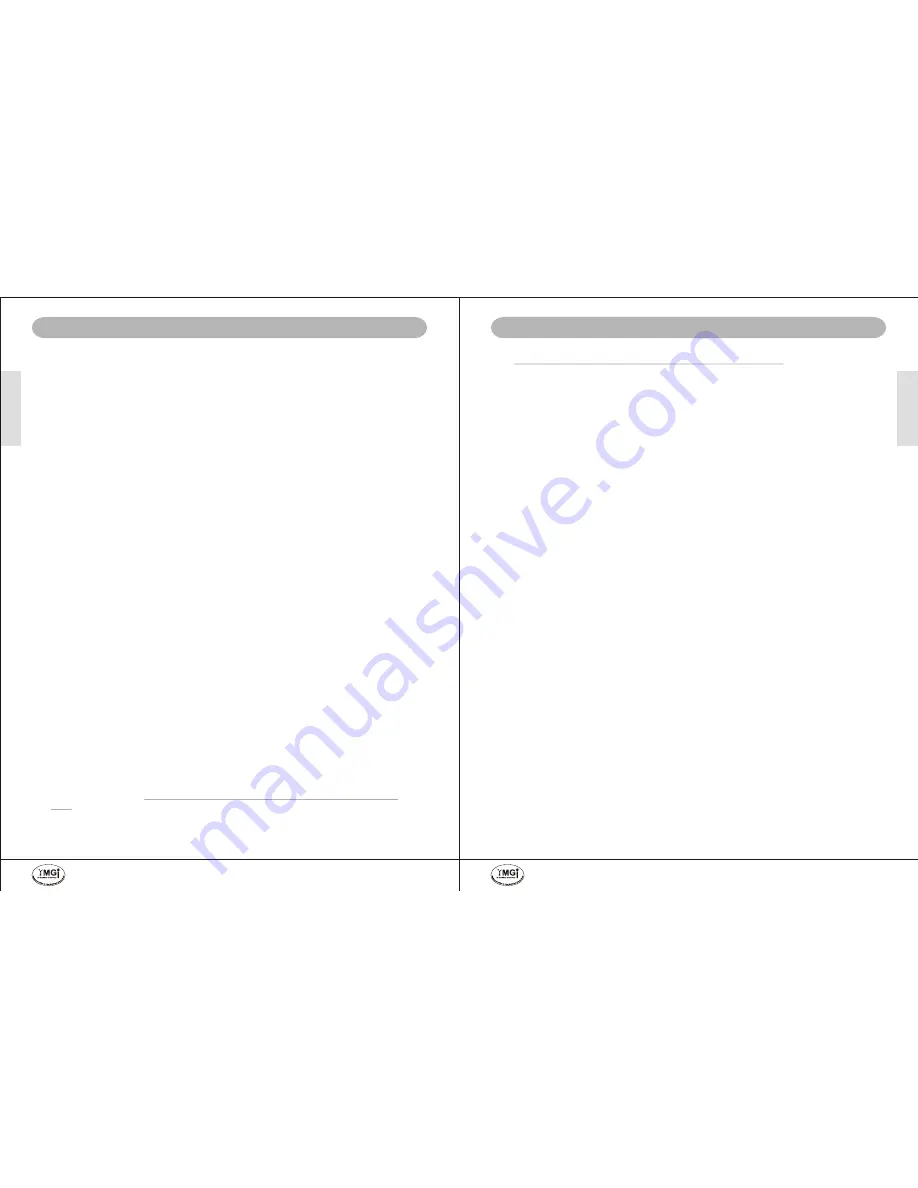
MUST READ
MUST READMUST READ
P3 OF 38
P4 OF 38
YMGI, Engineered Comfort Products for A Sustainable and Efficient Green World !
YMGI, Engineered Comfort Products for A Sustainable and Efficient Green World !
DEAR CUSTOMER(S)/END USER(S)/UNIT PURCHASER(S)/INSTALLER(S)/
CONTRACTOR(S)
Thanks for choosing YMGI products.
The YMGI equipment you purchased is either a split-type or a self-contained cooling/heating system which
requires an installer's license, certification, knowledge, experience, carefulness and details for a successful and
good installation. This equipment is different from those window or portable air conditioners you can normally
purchase from local retail stores such as Home Depot, Lowe's, Sears, etc. which the manufacturer may not
require licensed personnel to install.
Reading and following the YMGI Group recommendations, suggestions, and requirements, written in the
following pages and other documents, is the first step in our hope and effort to help ensure a smooth installation
& proper operation of your products for many years.
WHY DOES YMGI GROUP REQUIRE INSTALLATION AND SERVICE TO BE
PERFORMED BY LICENSED OR CERTIFIED HVAC TECHNICIAN/
CONTRACTOR?
1) They have the training and experience to accurately and safely install and service your equipment.
The equipment runs with high-pressure refrigerant and oil and line-voltage. The copper lines must be installed
properly to prevent leakage and foreign substances from contaminating the refrigerant system.
2) You will save money in the long run.
If any problems occur on the unit that is fully installed by the licensed or certified contractor, they have the
training and experience to correct the problem more efficiently. A technician(s) may be unwilling to repair an
issue on a unit that they did not install. If you do find a technician willing to perform the service, there is an
increased possibility of higher service fees than normal, increased service visits, or delayed service from that
technician.
3) It's the law!
The federal, state and/or local government and authorities have various governing laws or regulations,
guidelines, ordinances, etc., requiring only licensed or certified professionals can install and service high
pressure HVAC equipment.
SUGGESTIONS, TO AID YOU IN HIRING AN HVAC CONTRACTOR:
1) Hire a currently, practicing, licensed/ certified HVAC technician/ contractor. Technicians, who are no longer
practicing (retired, etc.) in this field, may not have the updated knowledge or may lack experience on the
equipment you have purchased.
2) Hire a technician/ contractor who services customers in your local area and you are familiar with. Local
contractors have a faster response time and will be easier for you to determine if they are reputable.
3) Use only reputable licensed/ certified HVAC installation contractors/ technicians to prevent any unexpected
charges as a result from unethical business practices.
4) Check their references, to verify they are a good service provider to the general customers. N.A.T.E or A.C.C.A
certified technicians are strongly recommended.
5) Some contractors/ technicians may not feel comfortable about installing the equipment that you purchased for
them to install, and they prefer to purchase and install the equipment. You can contact YMGI directly to check
and see if there have been any contractors in your area who have installed our products or similar.
6) Ask for a detailed quote for the whole installation project. A flat rate quote is the safest contract for both you
and the contractor
7) Your local HVAC technicians may charge you on a project basis or on an hourly basis. To our general
knowledge and experience,
a full single head installation may normally cost anywhere from $800 to
$1500
. These costs are estimates and your actual costs may differ due to job nature and location.
8) Number of hours can vary depending upon each individual situation, some factors are, but not limited to:
9) How difficult or complex the indoor unit is to be securely installed.
10) How difficult or how long the inter-connecting pipes and wires are to be installed.
11) If all the suggestions have been taken and all the necessary steps are followed.
CUSTOMER AND TECHNICIAN MUST READ
The cost of not having your unit installed properly can be more expensive than spending the little extra money
that hiring the right contractor will cost. Protect your investment and warranty eligibility by doing it right the first
time.
THE FOLLOWING LISTS THE JOBS AND RESPONSIBILITIES OF THE
TECHNICIAN/ CONTRACTOR:
* Performing a load calculation for the room(s) you would like to air condition. Cooling requirements will be
different from the heating requirements. They will consider cooling hours, heating hours and your special needs
or requirements. Supplemental heating such as baseboard heater or portable heater may help you save money
by not over-sizing or under-sizing the heating equipment.
* Selecting the right type, size or model of cooling and/or heating equipment.
* Determining the best location to install the unit. (Positioning indoor unit, outdoor unit and running the inter-
connecting pipes/wires.)
* Selecting the correct electrical components (HVAC circuit breaker or fuse and disconnect switch for the electric
power to the outdoor unit, types and sizes of the connecting wires between circuit breaker/disconnect switch
and outdoor unit, and the wires between outdoor unit and indoor unit).
* Keeping the indoor unit away from the ceiling and the outdoor unit away from the wall, bushes and other
obstacles at a proper and safe distance to allow for the proper airflow through the unit's.
* Placing the units on a secured level structure.
* Taping and sealing both ends of the inter-connecting pipes, before running them through structures, to prevent
dust or other debris from getting into the pipes otherwise they will contaminate and damage the refrigeration
system. Failure to follow this practice will make your factory warranty void.
* Connecting the inter-connecting pipes between the outdoor and indoor units. Checking for leaks through
pressurization with nitrogen. After releasing nitrogen, evacuate the piping and indoor unit, for removal of system
contaminants. Finally refrigerant introduction and adjustment, if necessary, from the outdoor unit.
* Back-seating the stopping valves at outdoor condensing unit to release pre-charged refrigerant from outdoor
unit to indoor unit.
* Measuring and recording the electrical voltages at different terminals and the refrigerant pressures at stopping
valves of outdoor condensing unit.
* Verifying and ensuring the unit is connected to the proper electrical power supply.
* Adjusting refrigerant levels (if necessary) following the installation instructions or chart on the unit.
* Checking for any unusual noises and other abnormalities that might be present.
* Operating the unit and check all functions, one by one, and explain to the owner how to operate and maintain
the unit.
* Completing all fields in detail on the installer checklist, signing and dating the
Warranty Registration Card/Form.
LIMITED PRODUCT WARRANTY
If the installation is successfully and fully done by a qualified licensed/ certified HVAC technician/contractor,
the
registration card/form is filled completely and correctly, and filed along with a valid installation invoice from the
contractor company within 7 days of the original installation, the following standard
Limited Product
Warranty
is
qualified:
5-year on compressor and 1-year other PARTS ONLY. There is
no labor coverage
.
12) If the contractor(s)/technician(s) are experienced with the systems/brands you purchase.
You might spend less. But remember, many times you get what you pay for.
13) Sign a contract with them. The contract should list all the detailed work they will conduct and the standards
they will follow. Some contractors are willing to include a 1-year installation/service warranty at no extra
charge. Check with them to see if that is available. If available, include that in the contract.
14) Verify and confirm the installation is done completely and all the unit functions have been checked and are
working properly, all the items in the checklist have been checked and marked well in the warranty registration
card/form, prior to paying the contractor in full.
CUSTOMER AND TECHNICIAN MUST READ