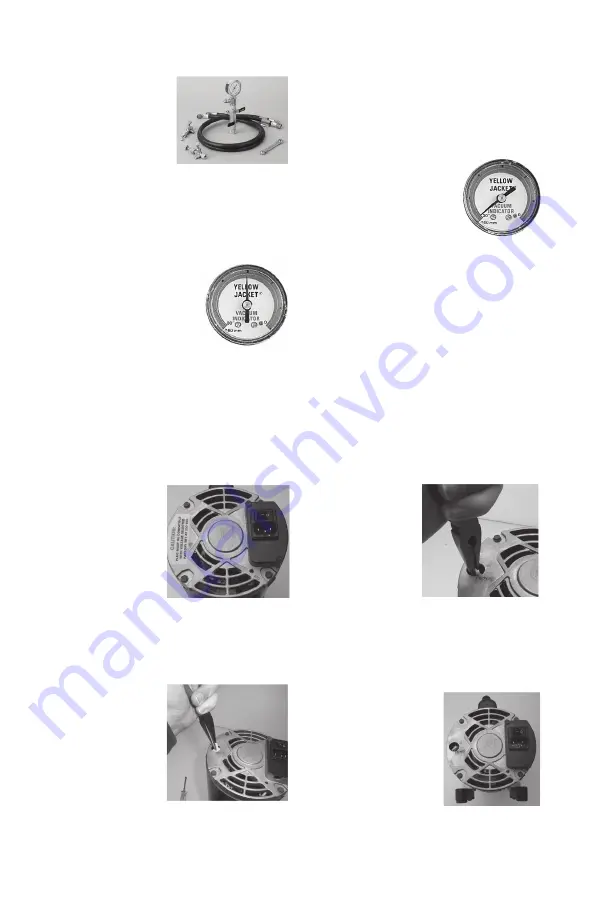
STEP 1
Disconnect the
motor from the
power supply
and remove.
Remove the yellow
“CAUTION” sticker
from the back of
the motor.
STEP 2
Pull up on the white plastic “arrow”
switch using needle-nosed pliers until
the switch is loose
inside the motor
housing (it will not
come completely
out of the motor).
NOTE: Do not try to
turn or rotate the
switch until it has
been pulled up and is loose.
If you think there is excessive mois-
ture, blow out the AC&R system with dry
nitrogen wherever possible. This reduces
the amount of contaminants that must
be “pulled” into the pump and increases
evacuation speed.
Use a nitrogen regulator
valve with pressure limited
to 150 psi and a frangible
disc device set at 175 PSIG.
When the indicator reaches
the 29-30” range, turn
on the electronic micron
gauge for more precise readings.
Oil Changes: CHANGE OIL AFTER EACH
USAGE
to protect pump components from
contaminants pulled into pump during
service. Place used oil in a sealable
container and dispose properly in accor-
dance with local regulations.
STEP 3
Point the arrow
toward the desired
voltage setting and
push the switch
back down into the
motor. The arrow on
the switch should
be sub-flush of the
motor housing when correctly installed at
the desired voltage.
HI = 230 VAC / 50 Hz
LO = 115 VAC / 60 Hz
STEP 4
Replace the yellow
“CAUTION” sticker over
the voltage selector
switch.
Ensure that the voltage
setting corresponds
with the power supply that the motor is
plugged into.
6
8. Use a SuperEvac System I, II or III to
decrease vacuum
time by over 50%.
These systems
include a 2-valve
vacuum manifold
and two 3/8”
vacuum hoses which can evacuate
three times faster than a 1/4” hose.
9. Use a heat gun on the condenser and
evaporator to speed the evacuation
process.
Built-in Vacuum Gauge:
The built-in indicator
gauge in your pump
monitors evacuation
progress down to the
29-30” range. If the
reading stays in the mid range, there is
either high contamination or a large leak
in the system.
Gross Leak
Dual Voltage Motor Power Conversion (if applicable)
Turn on
Electronic Gauge
*Warranty is void if the set vacuum pump voltage does not match the power supply. Dual voltage
motors are factory set to 230V/50Hz.