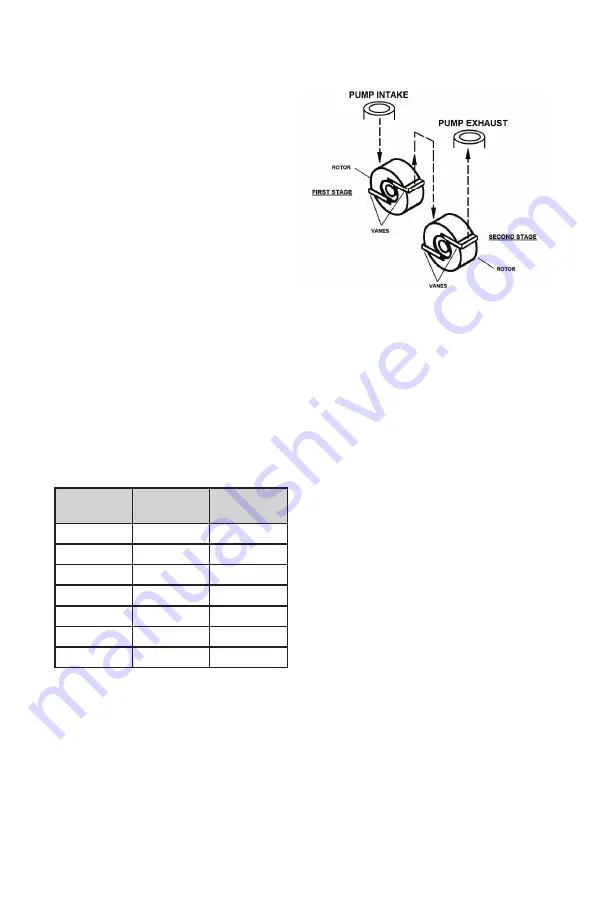
The SuperEvac Pump is a 2-stage ro tary
vane design (at right) that increases
efficiency and speeds pump down to 15
microns.
The pump lowers the internal pressure of
a refrigeration system until moisture boils
into a vapor. As the moisture is vaporized,
it is evacuated by the pump to help dehy-
drate the system. Most technicians try to
achieve between 250 and 1000 microns.
A manometer or electronic vacuum gauge
are the only ways to monitor evacua-
tion progress. Manometer readings are
approximate in inches of mercury. Only an
electronic vacuum gauge (see page 8) is
accurate enough to show when you reach
the desired mi cron range.
As the chart shows, only an electronic
gauge reads fine differences to provide
assurance that the vacuum is low enough
to boil the greatest possible amount of
moisture.
The Purpose of the SuperEvac
™
Design
How one small drop dampens
your profits.
A small drop of moisture can hurt your
profits and reputation.
During new system set-up, protective caps
are removed admitting moisture and air
into system components.
First stage exhausts into the intake of the second stage
similar to two single stage pumps connected together.
If air – a non-condensible – remains in the
system, it collects on the high side reduc-
ing system efficiency. This causes a rise
in head pressure. The discharge valve gets
hotter than normal and organic solids form
causing compressor failure.
Moisture in the system can form ice which
closes off openings in expansion valves
and cap tubes, and prevent adequate
cooling.
Ultimately moisture and air can produce
acids and sludge which could cause
in -warranty failures.
During service and parts replacement,
the same contaminants get in again, and
you could be called back for repairs by a
dissatisfied customer.
Moisture and air can even enter through
system leaks. And as the moisture in
the air increases, so does the amount of
contamination. The higher the humidity,
the bigger your problem.
A vacuum pump “pulls” air and mois-
ture out of the system before the system
is damaged. The higher and more
complete the vacuum, the more moisture
is removed. That’s why your SuperEvac
pump is specifically engineered for high
vacuums of 15 microns and better.
4
Boiling Temp
of Water
Inches
Mercury
Microns
212°F (100°C)
0
760,000
151°F (66°C)
22.05
200,000
101°F (38°C)
27.95
50,000
78°F (26°C)
28.95
25,000
35°F (2°C)
29.72
5,000
1°F (17°C)
29.882
1,000
-50°F (-46°C)
29.919
50