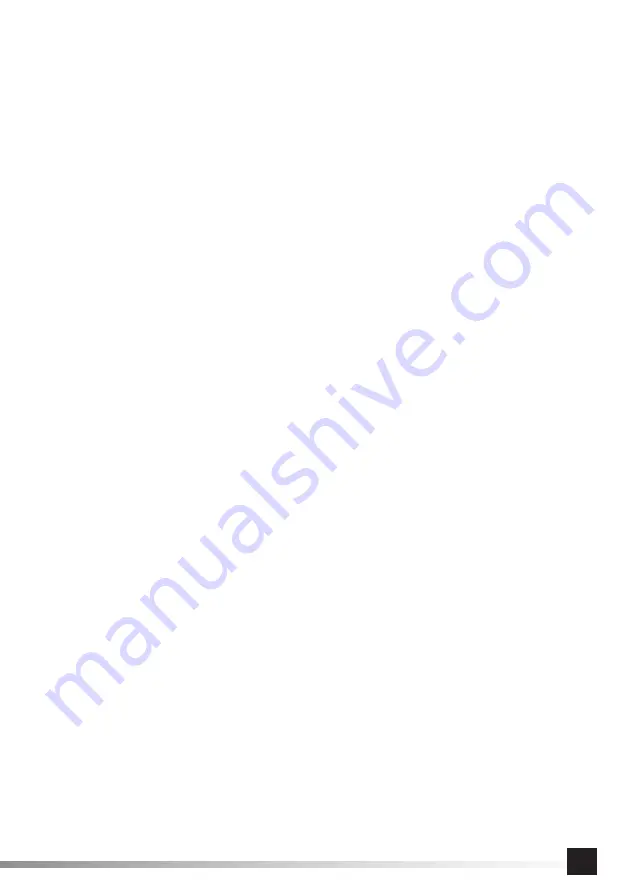
13
GB
O
R
I
G
I
N
A
L
I
N
S
T
R
U
C
T
I
O
N
S
MAINTENANCE AND CHECKS
Lubrication
Always before using drill bits or chisels, clean them and apply a thin layer of grease onto the tool chuck.
Oil re
fi
lling (V)
The hammer drill mechanism is lubricated by means of an oil bath. At the bottom of the housing there is an oil
fi
ller with an inspec-
tion glass. If the hammer is set with the tool chuck pointing upwards and the oil in the inspection glass is not visible, it should be
re
fi
lled. Oil level should be approx. 3 mm measured from the lower edge of the inspection glass. It is recommended to use SAE
20W-50 viscosity class engine oil .
Oil re
fi
lling should be carried out as follows. Unplug the power cord plug from a mains socket. Turn the hammer so that the oil
fi
ller is directed upwards. Unscrew the
fi
ller plug with inspection glass. Take precaution measures not to lose or damage the rubber
seal under the plug.
Re
fi
ll the oil and screw the
fi
ller plug. Tighten the plug with su
ffi
cient force required to obtain tightness. Excessive force may dam-
age the sealing or the threaded connection of the plug. Check the oil level before the start of work.
Oil should be re
fi
lled every 20 days of operation, assuming that the hammer works for about 3-4 hours per day.
ATTENTION! Before any adjustment, technical service or maintenance operations unplug the tool. Once the operations have been
fi
nished, the technical conditions of the tool must be assessed by means of external evaluation and inspection of the following
elements: body and handle, conductor with a plug and de
fl
ection, functioning of the electric switch, patency of ventilation slots,
sparking of brushes, noise level of functioning of bearings and gears, start-up and smoothness of operation. During the guarantee
period, the user cannot dismantle the electric tools or change any sub-assemblies or elements, since it will cancel any guarantee
rights. All irregularities detected at overhaul or during functioning of the tools are a signal to have the tool repaired at a service
shop. Once the functioning has been concluded, the casing, ventilation slots, switches, additional handle and protections must be
cleansed with a stream of air (at a pressure not exceeding 0.3 MPa), with a brush or a cloth without any chemical substances or
cleaning liquids. Tools and handles must be cleansed with a clean cloth.
Summary of Contents for YT-82002
Page 18: ...18 RUS 2 YT 82002 230 50 1600 1 1900 65 14 8 91 3 3 0 100 4 2 42 2 14 59 1 5 II IPX0 30...
Page 19: ...19 RUS...
Page 20: ...20 RUS II III 180 180 IV IV...
Page 21: ...21 RUS 5 60 C V 3 SAE 20W 50 20 3 4 0 3 MPa...
Page 22: ...22 UA 2 YT 82002 230 50 1600 1 1900 65 14 8 91 3 3 0 100 4 2 42 2 14 59 1 5 II IPX0 30...
Page 23: ...23 UA...
Page 24: ...24 UA II III 180 180 IV IV 5...
Page 25: ...25 UA 60 C V 3 SAE 20W 50 20 3 4 0 3 MPa...
Page 67: ...67 GR RCD RCD...
Page 68: ...68 GR 180O 180O V IV...