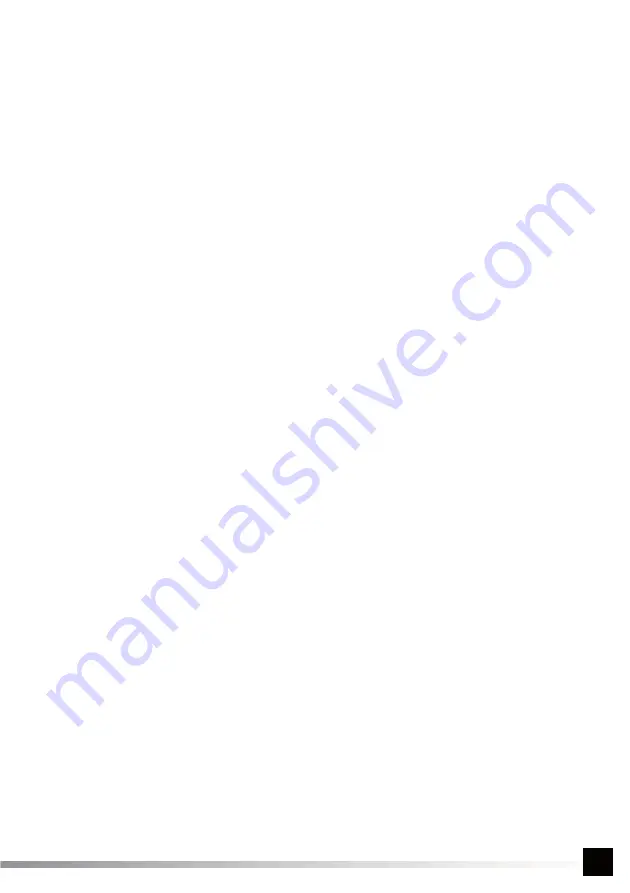
11
O R I G I N A L I N S T R U C T I O N S
GB
ment of the damaged element for a new one, free from damage.
Wash the product in accordance with the instructions from the point “Product maintenance”.
The product should be adjusted in accordance with the recommendations and leave for at least an hour in order to stabilize the
oil level in its pump.
Before connecting the product to the power supply, check the oil level in the pump. Attention! The starting of the product with
improper oil level can lead to damage to the product. It is recommended to use oil which is intended for vacuum pumps.
Depending on the type of product, remove the back panel (II) or pick up the entire upper case (III). Oil pump is equipped with the
oil level indicator, which should be between 1/2, and 3/4 of the indicator height. In other case you should refill the oil level or drain
oil to the required level.
In order to fill oil you should pour oil into the dispenser, unscrew the filler opening cap and pour oil into the tank of the pump, at that
time observing the oil level in the indicator. Then screw the infill opening cap and close the product housing (IV).
In the case of a too high oil level, your should place an container under the drain hole, unscrew the cap of the drain hole and drain
the excess oil to achieve the required level. Then screw the infill opening cap and close the product housing (IV).
Attention! If during the above described steps there will be spilled oil, it should be exactly wiped out before closing the product
housing.
Attention! It is recommended to carry out the exchange of oil every 120 hours of operation.
Attention! It is recommended to carry out the exchange of oil when the pump is still warm when you are finished working. This will
dilute the oil and make it easier to flush the oil tank.
You should leave the opened cover of the vacuum chamber.
Connect the power cable plug into the mains wall socket, and then start the product by using the mains switch located on the rear
wall of the product.
Mains power supply connection of the packager YG-09307
Packager YG-09307 requires power supply of three-phase voltage specified in the technical data table. Therefore, because of
multiple plug standards, the packager is supplied with a power supply cable, equipped with five cables, but without a plug.
Attention! It is required that the connection of power plug would be by a staff with the relevant classifications (electrical authoriza-
tion). It is forbidden to connect the power plug by someone’s own.
You should connect to the cable a plug with five pins which is compliant with IEC 60309 standard. The power supply installation for
the packager should be equipped with three wires, grounding wire and protecting wire (3P+N+E). Power cable wires are marked
with colors. Mains wire L1: brown, L2 wire: gray, L3 wire: black, neutral wire N: blue, protecting wire: yellow-green.
Cable wires and the connecting cable itself should be connected in accordance with the documentation that attached to the plug.
Installation for the product supply should be equipped with safety switch which would an emergency shutoff of the power supply.
Control Panel
The product is equipped with a control panel, which allows you to set the operating parameters.
Button marked “I” is used to switch on the product.
Button marked “O” is used to switch off the product.
Button marked “STOP” is used for an emergency work interruption. When you press this button, it follows with the immediate
stopping of work which is currently performed, filling the vacuum chamber with air, and then opening the cover of the vacuum
chamber.
The button labeled “SET/UST” is used to select the parameter to adjust its duration. The possible parameters are: emptying time
from the air of vacuum chamber, time of the bag sealing and time the heating bar cooling off.
Button marked “+” is used to enhance the value of parameter.
Button marked “-” is used to reduce the value of parameter.
Button marked „SEALING TEMPERATURE / TEMPERATURA ZGRZEWANIA” is used to select the temperature for sealing the
bag. There are three possible settings: „HIGH/WYSOKA”, „MIDDLE/
Ś
REDNIA” and „LOW/NISKA”, they are signaled by lighting
up the control with an appropriate description. When selecting the temperature you should be guided by the thickness of the bag.
The greater the thickness of the bag, the higher temperature should be set. It is recommended to make trials and to carry out an
experimental determination of correct sealing temperature for the bags. You can also contact the manufacturer of your bags and
get information about their sealing temperature. In the case, when it is impossible to obtain the above mentioned information, it is
recommended that you set the average welding temperature and sealing time for 1.2 seconds.
In addition to the buttons on the control panel, there is a gauge indicating the pressure in the vacuum chamber, the LED display
marked “TIME/CZAS”, and a number of controls to allow the user to check the status of the product parameters.
The control labeled “VACUUM/PRÓ
Ż
NIA” is enabled at the time of the air suction from vacuum chamber of packaging machine.
Control marked “GAS/GAZ” is enabled at the time of filling the bag with inert gas (nitrogen). Because the packagers do not have
the possibility of filling the bag with inert gas, this control remains inactive.
Control labeled “SEALING/ZGRZEWANIE” is enabled at the time of the bag closing by sealing its edges.
Control labeled “COOLING/CH
Ł
ODZENIE” is turned on during the cooling operation of the heating bar.
Turned on the control “WORKING/PRACA” means, that the activity of the product in one of the operating modes.