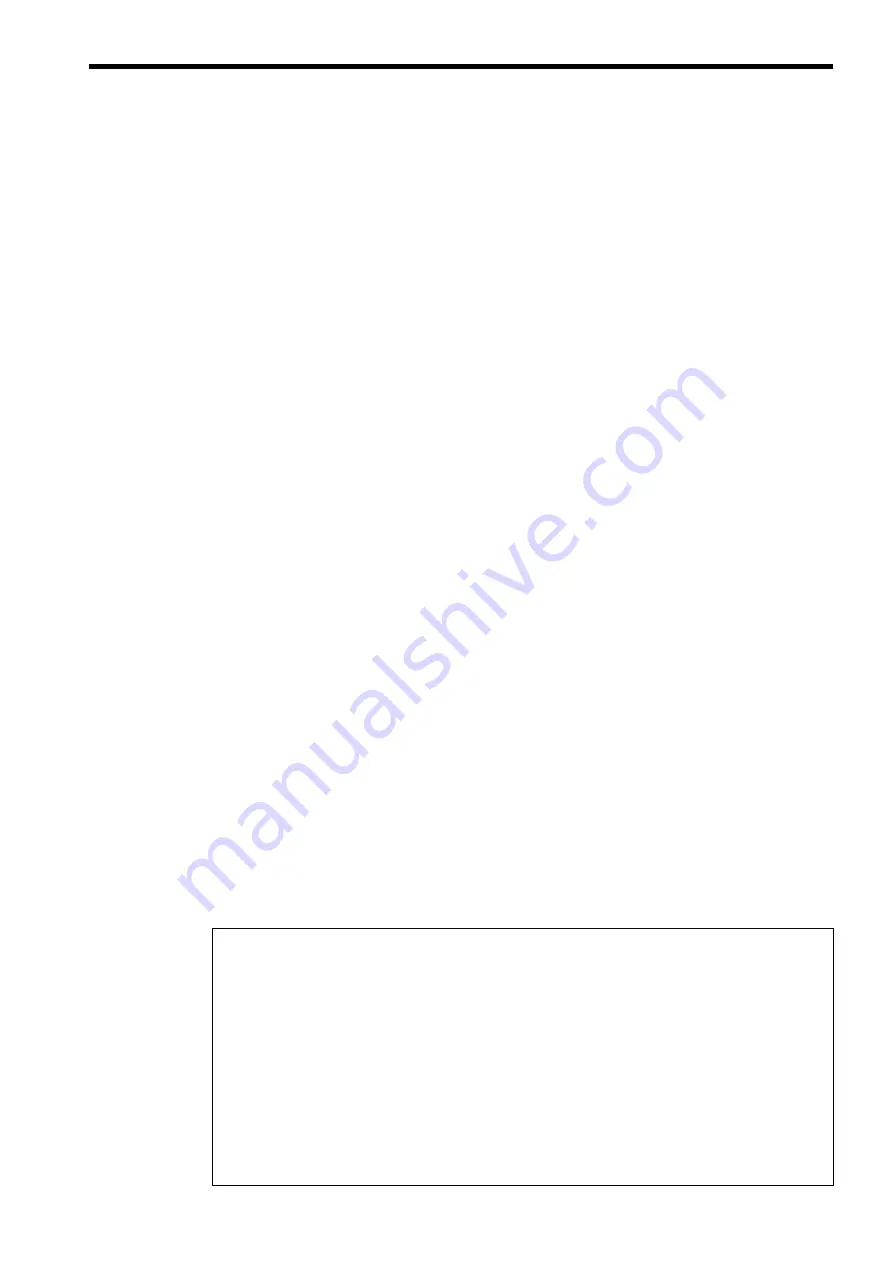
3
Introduction
Thank you for purchasing a Current Vector Control General-purpose Varispeed G7/F7
Inverter and a SI-T MECHATROLINK-I/MECHATROLINK-II Communications Interface
Card (called “SI-T Card” below).
This manual describes the operation and specifications of the SI-T Card, which connects to
the MECHATROLINK-I/MECHATROLINK-II high-speed field network for exchanging
data. Be sure that you have read and understood this manual before attempting to operate the
SI-T Card.
For details on operating the Inverter itself, refer to the Varispeed G7/F7 Series Instruction
Manual (TOE-S616-60.1, TOE-S616-55.1).
Yaskawa Electric, Inc.
General Precautions
• The diagrams in this manual may be indicated without covers or safety shields in order to show
details. Be sure to restore covers or shields before operating the Inverter, and operate the Inverter
according to the instructions provided in this manual.
• The products and specifications described in this manual or the contents and presentation of the
manual may be changed without notice to improve the product and/or the manual.
• When ordering a new copy of the manual due to damage or loss, contact your Yaskawa represen-
tative or the nearest Yaskawa sales office and provide the manual number shown on the front
cover.
• Any modifications to the product by the customer invalidate the warranty, and Yaskawa accepts no
responsibility for the results of any modifications