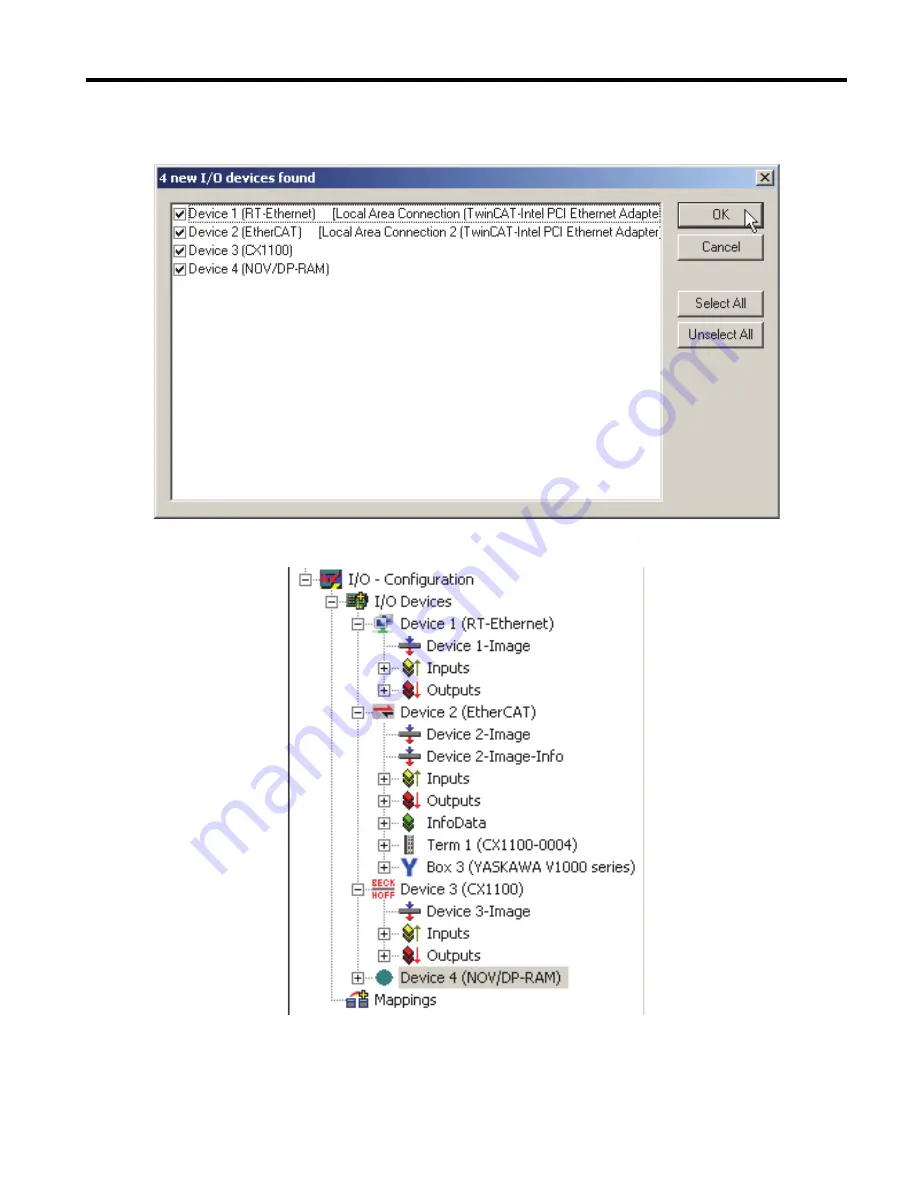
10 Examples
YASKAWA ELECTRIC
TOBP C730600 96C YASKAWA AC Drive Option SI-ES3 Installation Manual
43
3. Make sure the EtherCAT device (line two in the graphic) is selected and confirm with
OK
.
Figure 21
4. TwinCAT System Manager will ask you to scan for boxes. Select Yes.
Figure 22
GEM_EtherCAT_IM_E_conditional.book 43 ページ 2018年10月25日 木曜日 午後7時29分