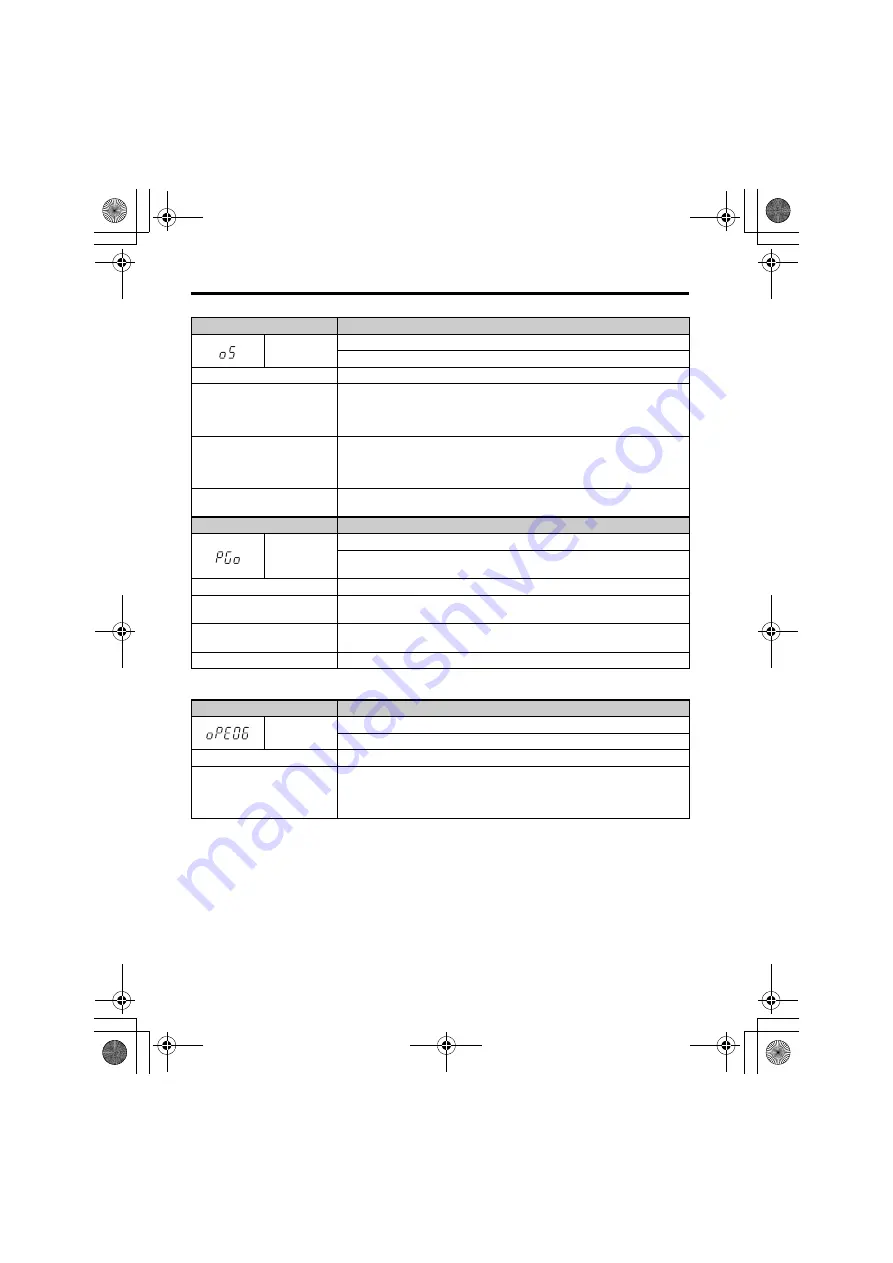
7 Troubleshooting
40
YASKAWA ELECTRIC
TOBP C730600 75B YASKAWA AC Drive Option PG-B3 Installation Manual
Table 12 Operation Error Displays, Causes, and Possible Solutions
Keypad Display
Fault Name
oS
Overspeed
The motor speed feedback exceeded the F1-08 setting.
Cause
Possible Solution
Overshoot is occurring.
• Increase the settings for C5-01 (Speed Control Proportional Gain 1) and reduce
C5-02 (Speed Control Integral Time 1).
• Adjust the input signal using parameters H6-02 through H6-05.
• Enable Feed Forward Control and perform Inertia Auto-Tuning in CLV.
Incorrect speed feedback scaling
when terminal RP is used as
speed feedback input in V/f
control.
Set H6-02 to the value of the speed feedback signal frequency when the motor
runs at the maximum speed.
Inappropriate parameter settings.
Check the setting for the overspeed detection level and the overspeed detection
time (F1-08 and F1-09).
Keypad Display
Fault Name
PGo
PG Encoder Disconnected
The drive has not received a PG encoder pulse for longer than the time set in
F1-14.
Cause
Possible Solution
The PG encoder is disconnected
or is not wired properly.
Make sure the PG encoder is properly wired or is not disconnected.
PG encoder does not have
enough power.
Confirm that the correct power supply is properly connected to the PG encoder.
Motor brake is engaged.
Ensure the brake releases properly.
Keypad Display
Fault Name
oPE06
Control Method Selection Error
Correct the setting for the control method.
Cause
Possible Solution
Control method requires
installing a PG option, but no PG
option is installed (A1-02 = 1, 3,
or 7).
• Connect a PG option.
• Correct the value set to A1-02.
TOBP_C730600_75B_1_0_E.book 40 ページ 2017年2月17日 金曜日 午後3時2分