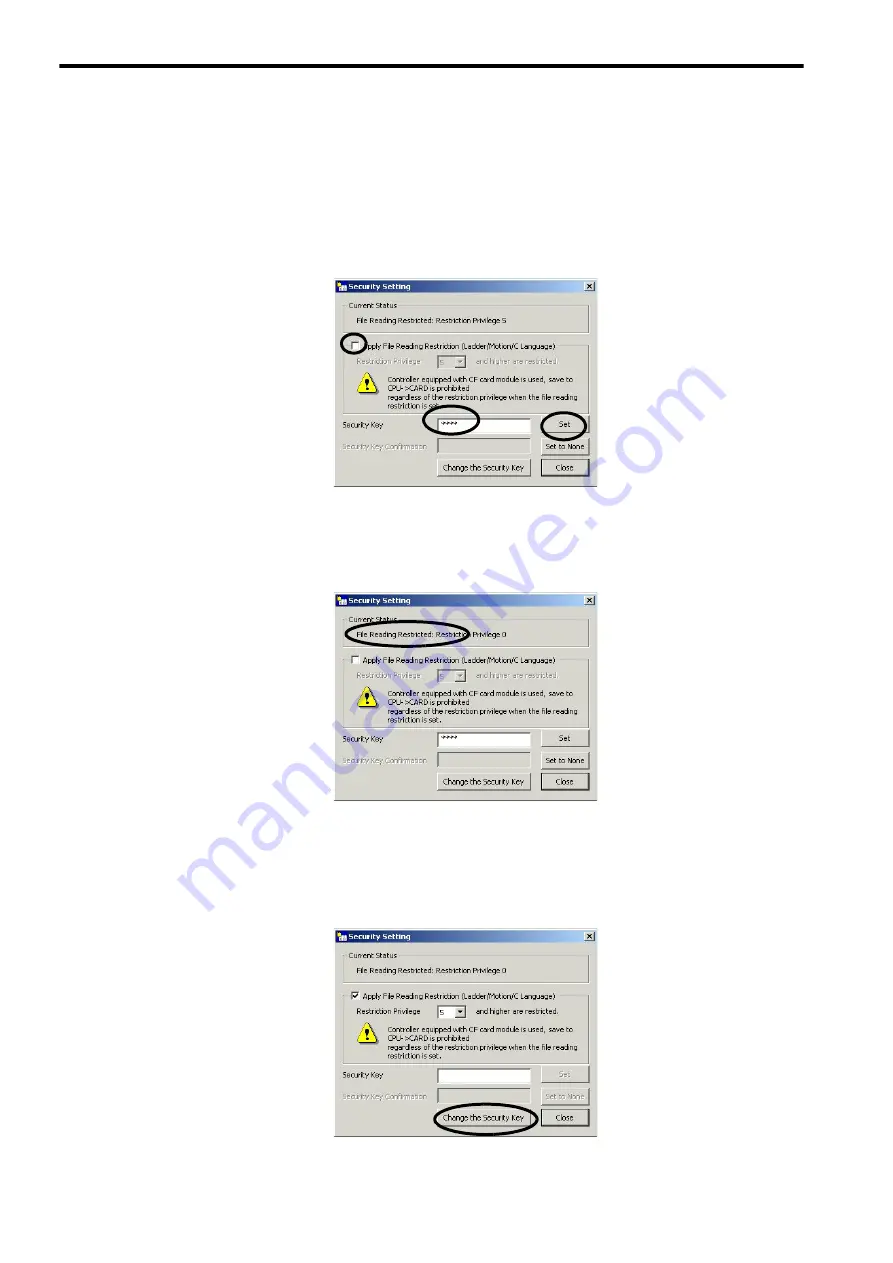
Appendix E Optional Functions
E.2 Security
A-90
[ d ] Changing the File Reading Restriction
Change the file reading restriction with the security settings made. In this example, we will release the restriction. To
set the restriction, use the same procedure. Having no file reading restriction set is the same as security being released.
1.
Select or clear the
Apply File Reading Restriction (Ladder/Motion/C Language)
Check Box. Enter
the password in the
Security Key
Field, and then click the
Set
Button.
2.
If the change in file reading restriction has been normally applied to the Controller, the status will
change from
File Reading Restricted
to
No Security Setting
in the
Current Status
Area.
[ e ] Changing the Security Key
The security key can be changed with the security settings made. This procedure will change only the security settings.
1.
Open the
Security Setting
Dialog Box, and then click the
Change the Security Key
Button.