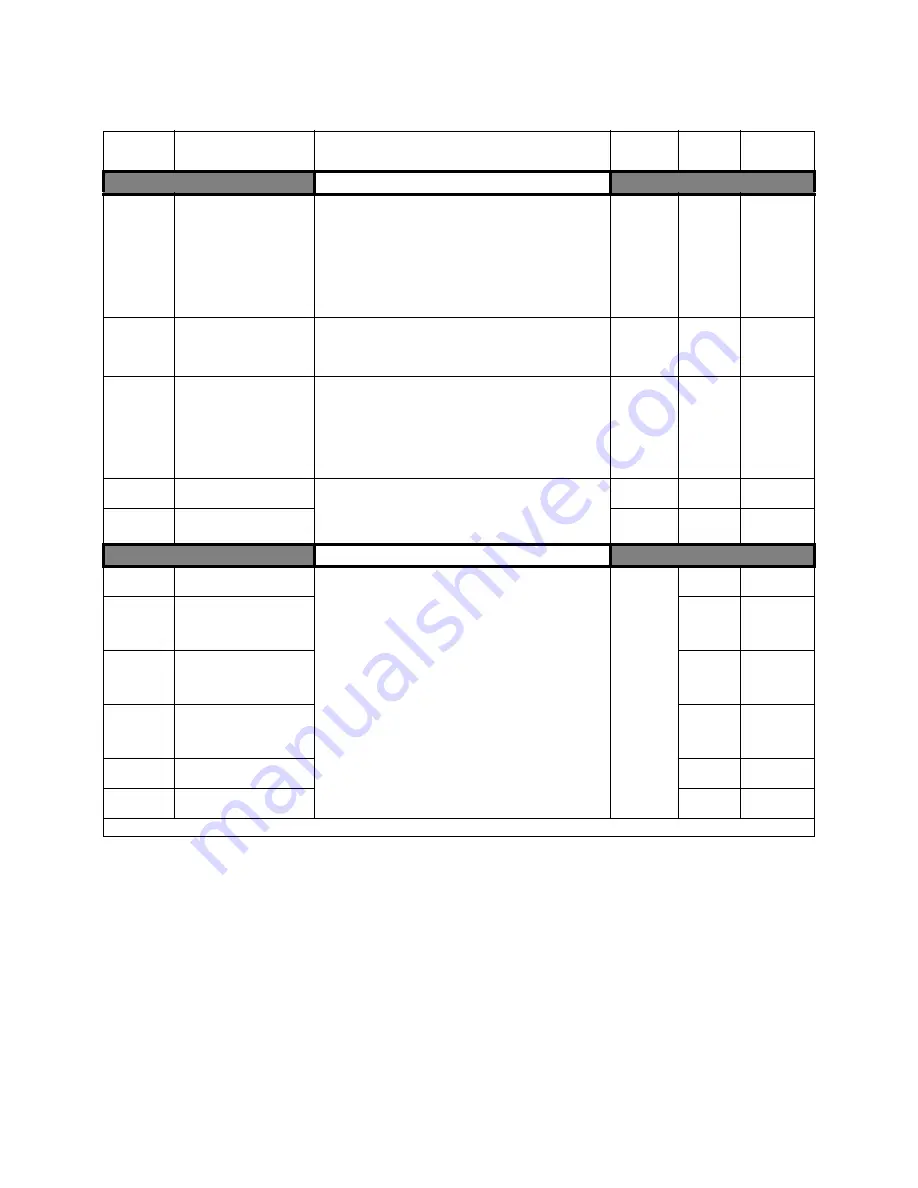
Parameter List A - 2
Table 1: E7 Parameter List
Parameter
No.
Parameter Name
Digital Operator Display
Description
Setting
Range
Factory
Setting
Menu
Location
Initialization
A1-00
Language Selection
Select Language
Language selection for digital operator display
0: English
1: Japanese
2: Deutsch
3: Francais
4: Italiano
5: Espanol
6: Portugues
*Not returned to factory setting by initialization
0 to 6
0
Quick Setting
A1-01
Access Level Selection
Access Level
This setting determines which parameters are accessable.
0: Operation Only
1: User Level
2: Advanced Level
0 to 2
2
Programming
A1-03
Initialize Parameters
Init Parameters
Used to return all parameters to their factory or user setting.
0: No Initialize
1110: User Initialize (The user must set their own parameter
default values and then parameter o2-03 must be set to “1” to save
them. If the parameter values are changed after o2-03 is set to “1”,
the user default values can be restored by setting A1-03 to 1110.)
2220: 2-Wire Initial
3330: 3-Wire Initial
0 to
3330
0
Programming
A1-04
Password 1
Enter Password
When the value set into A1-04 does NOT match the value set into
A1-05, parameters A1-01 thru A1-03 and A2-01 thru A2-32 cannot
be changed. All other parameters as determined by A1-01 can be
changed. Parameter A1-05 can be accessed by pressing the MENU
key while holding the RESET key.
0 to 9999
0
Programming
A1-05
Password 2
Select Password
0 to 9999
0
Programming
User Parameters
A2-01
User Parameter 1
User Param 1
Selects the parameters to be available in the User Access Level
(A1-01 = 1). These are the only parameters accessible for the user
level. These parameters are not related to the User Initialize
function.
b1-01
to
o3-02
–
Programming
A2-02
User Parameter 2
User Param 2
–
Programming
A2-03
User Parameter 3
User Param 3
–
Programming
A2-04
User Parameter 4
User Param 4
–
Programming
A2-05
User Parameter 5
User Param 5
–
Programming
A2-06
User Parameter 6
User Param 6
–
Programming
Denotes that parameter can be changed when the drive is running.
Summary of Contents for E7 Drive
Page 1: ...E7 Drive User Manual Model E7U Document Number TM E7 01...
Page 74: ...Start Up 4 10 Notes...
Page 132: ...Maintenance 7 8 Notes...
Page 162: ...Parameter List A 30 Notes...
Page 166: ...Capacity Related Parameters B 4 Notes...
Page 184: ...Communications D 14 Notes...
Page 192: ...Spare Parts F 4 Notes...