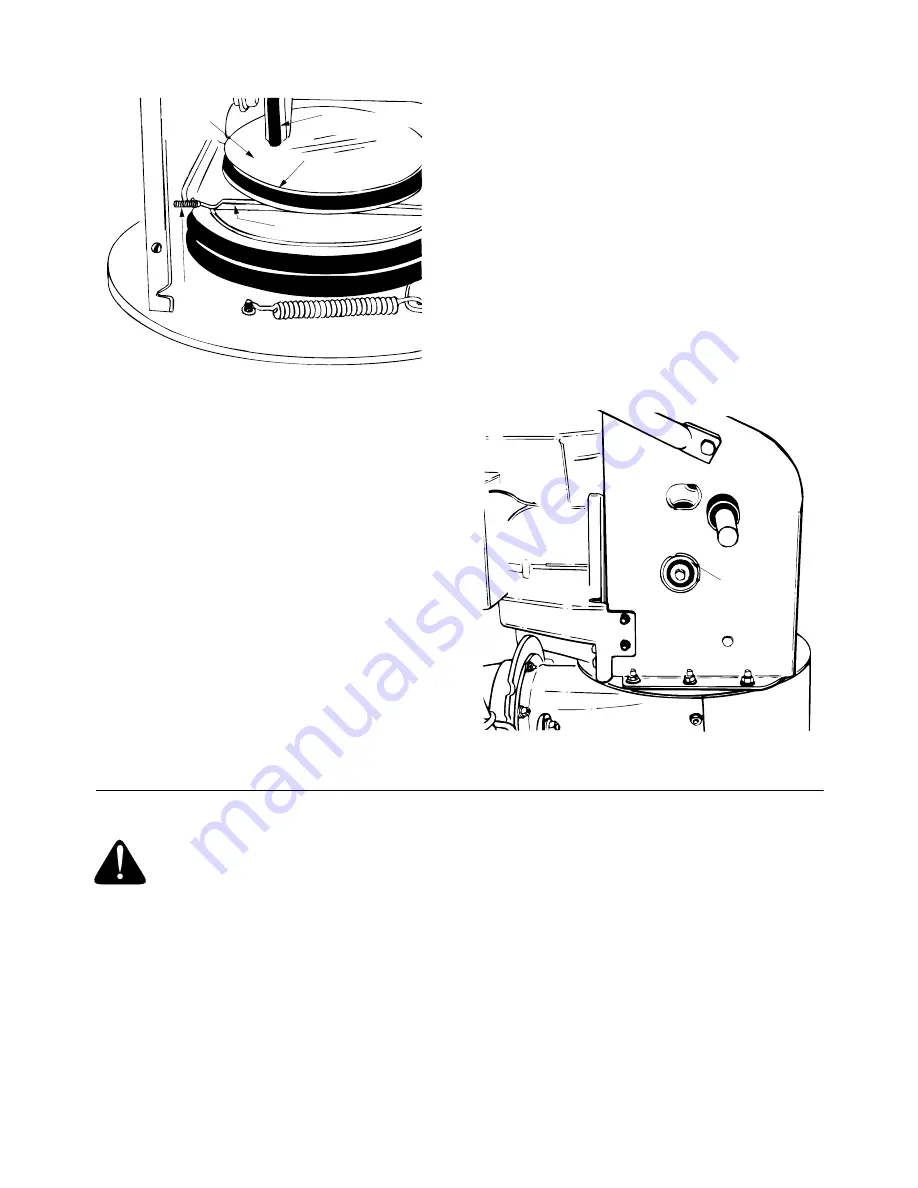
18
Figure 32
CHANGING THE FRICTION WHEEL RUBBER
The rubber on the friction wheel is subject to wear
and should be checked after 25 hours of operation,
and periodically thereafter. Replace the friction
wheel rubber if any signs of wear or cracking are
found.
1.
Drain the gasoline from the snow thrower, or
place a piece of plastic under the gas cap.
2.
Tip the snow thrower up and forward, so that it
rests on the auger housing.
3.
Remove six self-tapping screws from the frame
cover underneath the snow thrower.
4.
Remove the klick pins which secure the wheels,
and remove the wheels from the axle.
5.
Using a 7/8" wrench to hold the shaft, loosen,
but do not completely remove, the hex nut and
bell washer on the left end of gear shaft. See
Figure 33.
6.
Lightly tap the hex nut to dislodge the ball
bearing from the right side of frame. Remove
the hex nut and bell washer from left end of
shaft.
7.
Slide the gear shaft to the right and slide the
friction wheel assembly from the shaft.
8.
Remove the six screws from the friction wheel
assembly (three from each side). Remove the
friction wheel rubber from between the friction
wheel plate.
9.
Reassemble new friction wheel rubber to the
friction wheel assembly, tightening the six
screws in rotation and with equal force.
Position the friction wheel assembly up onto the pin
of the shift rod assembly, and slide the shaft
through the assembly. Reassemble in reverse order.
Figure 33
SECTION 11: OFF-SEASON STORAGE
WARNING:
Never store engine with
fuel in tank indoors or in poorly
ventilated areas, where fuel fumes may
reach an open flame, spark or pilot
light as on a furnace, water heater,
clothes dryer or other gas appliance.
1.
If unit is to be stored over 30 days, prepare the
engine for storage as instructed in the separate
engine operator’s manual included with your
unit.
2.
Remove all dirt from exterior of engine and
equipment.
3.
Follow lubrication recommendations on page 16.
NOTE:
When storing any type of power
equipment in a poorly ventilated or metal storage
shed, care should be taken to rust proof the
equipment. Using a light oil or silicone, coat the
equipment, especially any chains, springs, bearings
and cables.
Stop
Bolt
Friction
Wheel
Disc
Drive Belt
Friction Wheel
Support Bracket
Hex Nut
Bell Washer
Summary of Contents for E602E
Page 20: ...20 SECTION 13 ILLUSTRATED PARTS HOUSING ASSEMBLY...
Page 22: ...22 HANDLE ASSEMBLY...
Page 24: ...24 FRAME ASSEMBLY...