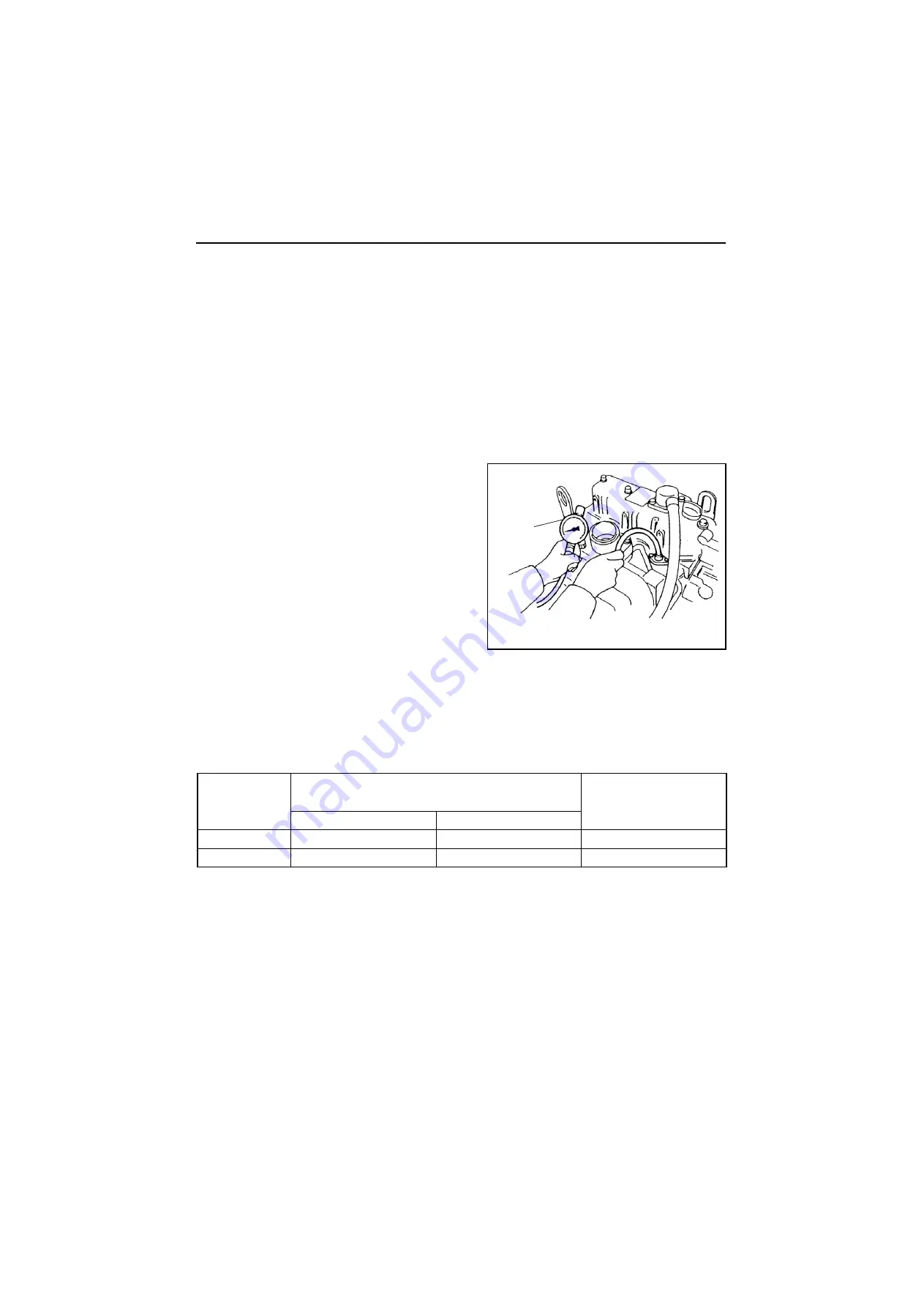
3. Troubleshooting
62
3.4 Troubleshooting by measuring compression pressure
Compression pressure drop is one of major causes of increasing blowby gas (lubricating oil contamination or
increased lubricating oil consumption as a resultant phenomenon) or starting failure. The compression pres-
sure is affected by the following factors:
1) Degree of clearance between piston and cylinder
2) Degree of clearance at intake/exhaust valve seat
3) Gas leak from nozzle gasket or cylinder head gasket
In other words, the pressure drops due to increased parts wear and reduced durability resulting from
long use of the engine.
A pressure drop may also be caused by scratched cylinder or piston by dust entrance from the dirty air
cleaner element or worn or broken piston ring. Measure the compression pressure to diagnose
presence of any abnormality in the engine.
(1) Compression pressure measurement
method
1) After warming up the engine, remove the fuel
injection pipe and valves from the cylinder to be
measured.
2) Crank the engine before installing the compression
gage adapter.
a) Perform cranking with the stop handle at the stop
position (no injection state).
b) See 4.2.3(2) in Chapter 4 for the compression
gage and compression gage adapter.
3) Install the compression gage and compression
gage adapter at the cylinder to be measured.
a) Never forget to install a gasket at the tip end of
the adapter.
4) With the engine set to the same state as in 2)a),
crank the engine by the starter motor until the
compression gage reading is stabilized.
(2) Standard compression pressure
Engine compression pressure list (reference value)
Model
Compression pressure at 250 min
-1
MPa (kgf/cm
2
)
Deviation among cylinders
MPa (kgf/cm
2
)
Standard
Limit
3YM30
3.43 ± 0.1 (35 ± 1)
2.75 ± 0.1 (28 ± 1)
0.2 ± 0.3 (2 ± 3)
3YM20
3.23 ± 0.1 (33 ± 1)
2.55 ± 0.1 (26 ± 1)
0.2 ± 0.3 (2 ± 3)
(Measurement of the compression pressure)
Compression
gage
Summary of Contents for 3YM30
Page 1: ...M9961 03E100...