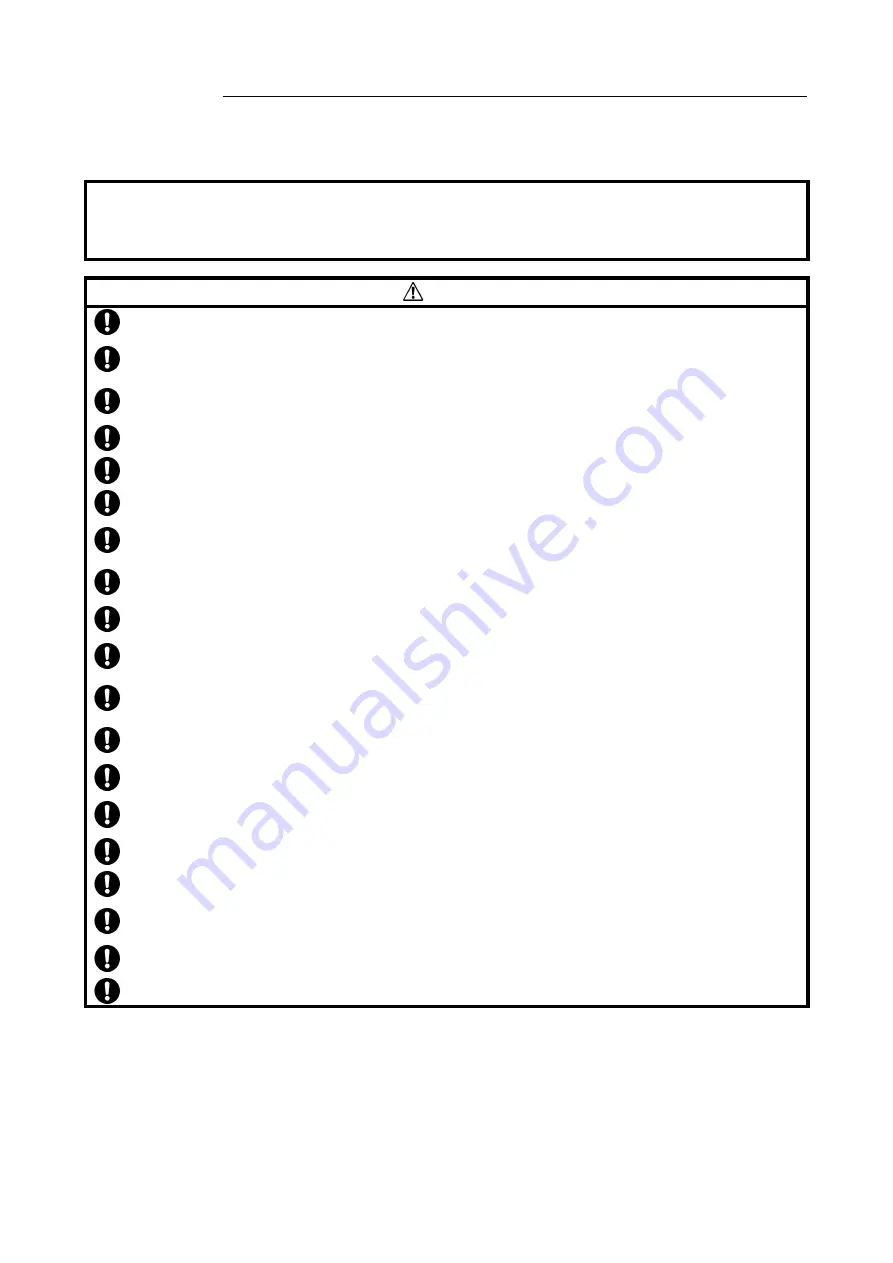
2
AB-6465
Safety Instructions
Please read instructions carefully and use the product as specified in this manual. Be sure to keep this manual nearby
for ready reference.
Usage Restrictions
This product is targeted for general air conditioning. Do not use this product in a situation where human life may be
affected. If this product is used in a clean room or a place where reliability or control accuracy is particularly required,
please contact Yamatake’s sales representatives. Yamatake Corporation will not bear any responsibility for the re-
sults produced by the operators.
CAUTION
•
Installation must be performed by qualified personnel in accordance with all applicable safety standards.
•
This product must be operated within its operating ranges specified in this manual. Failure to comply will
cause equipment damages.
•
Installation must be carried out under the operating conditions specified in this manual to prevent equip-
ment damages.
•
For storage, do not stack too many container boxes in which products are packed.
•
Do not put heavy load on the actuator.
•
Do not leave the controlled fluid frozen. Equipment damages and leakage may occur.
•
Make sure the flow direction and install the product in the direction and position specified in this manual.
Excessively tight connection of piping and improper installation position may cause equipment damages.
•
Flush the piping so that no foreign substance remains. Attach a strainer at upstream side of the piping to
prevent equipment damages.
•
After the piping installation, make sure no fluid leaks from the connecting parts.
•
Do not install the product in a location adjacent to a steam coil or a hot-water coil. High temperature ra-
diation may result in an actuator malfunction.
•
Avoid instrumentation that keeps equipment operating cycle excessively frequent so as not to shorten the
equipment operating life.
•
When this product is used with a controller of another manufacturer, contact Yamatake’s sales represen-
tatives.
•
All wiring must comply with local codes of indoor wiring and electric installation rules.
•
Disconnect the power supply before performing any wiring to prevent electrical shock or equipment dam-
ages.
•
Use crimp terminals with insulation for electric wires.
•
Make sure all the wires are tightly connected to prevent heat generation and equipment damages.
•
Do not disassemble the product at any time except when removing the cover to wire or replacing a part to
prevent equipment damages.
•
Do not incinerate this product for waste disposal. Do not recycle all or a part of this product, either.
•
Dispose of this product as industrial waste in accordance with the local regulations.
Trademark information:
ACTIVAL, Infilex, Neostat are trademarks or registered trademarks of Yamatake Corporation in Japan or other countries.
Summary of Contents for ACTIVAL VY51X2J
Page 14: ...14 AB 6465 ...
Page 15: ...15 AB 6465 ...