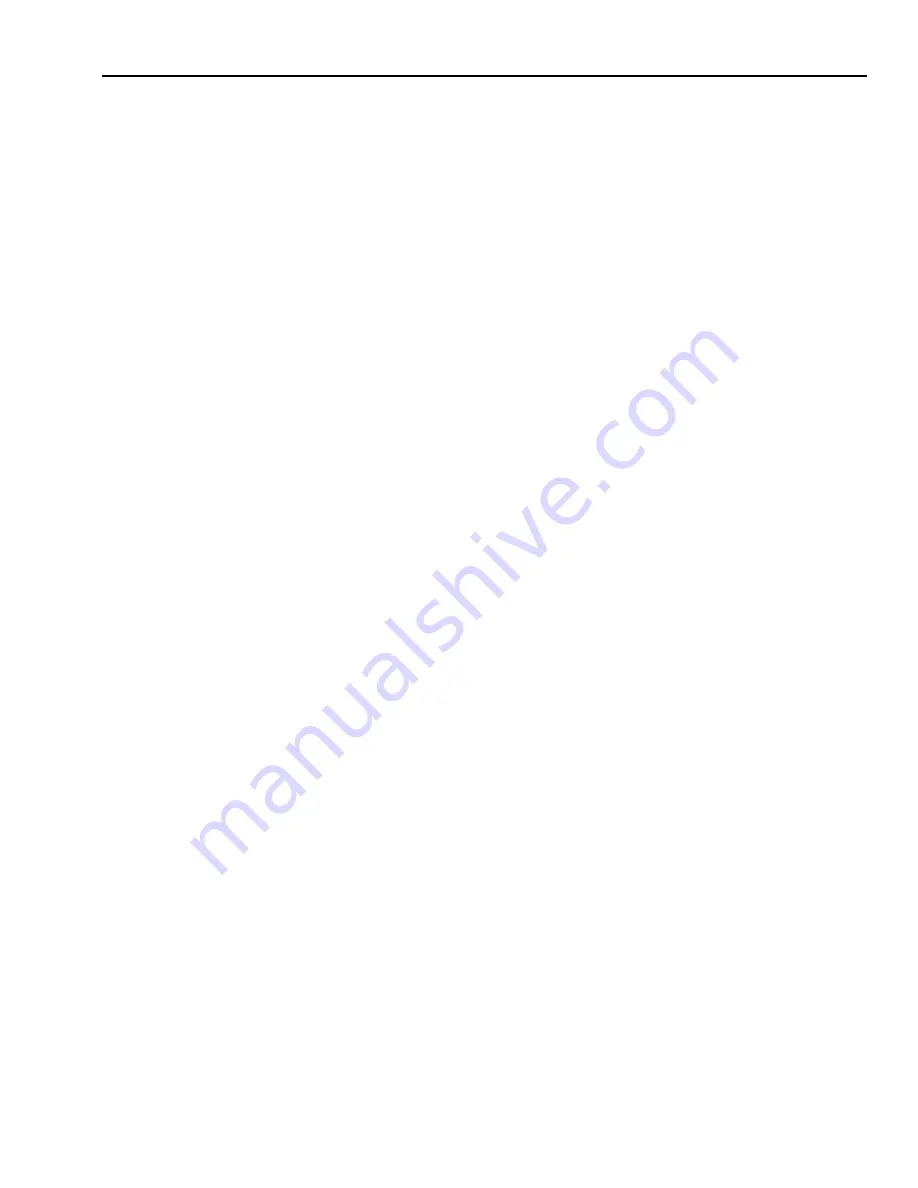
7800 SERIES EC7885A/RM7885A RELAY MODULE
65-0203
23
3. For a flame rod, make sure:
•
Ground area is large enough.
•
Flame rod is properly located in the flame.
•
Temperature at the flame rod insulator is no
greater than 500
°
F (260
°
C).
4. For all optical detectors, clean the detector viewing
window and inside of the sight pipe as applicable.
5. With the burner running, check the temperature at the
detector. If it exceeds the detector maximum rated
temperature:
•
Add a heat block to stop conducted heat traveling
up the sight pipe.
•
Add a shield or screen to reflect radiated heat.
•
Add cooling (refer to sight pipe ventilation in the
detector Instructions).
6. Make sure that the flame adjustment is not too lean.
7. Make sure that the detector is properly sighting the
flame.
8. If necessary, resight or reposition the detector.
Initial Lightoff Check For Proved Pilot
Perform this check on all installations that use a pilot. It
should immediately follow the preliminary inspection.
NOTE:
These steps may require two people, one to open
the manual valve(s) and one to watch for ignition.
NOTE:
Low fuel pressure limits, if used, could be open. If
so, bypass them with jumpers during this check.
1. Open the master switch.
2. Make sure that the manual main fuel shutoff valve(s) is
closed. Open the manual pilot shutoff valve. If the pilot
takeoff is downstream from the manual main fuel
shutoff valve(s), slightly open the manual main valve to
supply pilot gas flow. Make sure the main fuel is shut off
just upstream from the burner inlet, or disconnect
power from the automatic main fuel valve(s).
3. Close the master switch. Allow ten seconds for the
7885A to complete the INITIATE Test. Start the system
by pushing the Start Switch, see Fig. 17, or 7885A
sequence. Ignition should occur and the 7885 will turn
on the PILOT LED and the pilot valve after a two-
second delay for the RM7885 to complete the Safe-
Start Check. The FLAME LED is energized when the
pilot flame is proven. The MAIN LED is turned on and
the ALARM LED and the Alarm output (terminal no. 3)
are turned off.
Proceed to step 5.
If the pilot does not light in ten seconds, release the Start
Switch. Allow time for purging the unburned fuel from the
combustion chamber before pressing the Start Switch for an
additional ten seconds.
4. If the pilot flame is not established on the second try,
make the following ignition/pilot adjustments or consult
the equipment operating manual for further information:
a.
Open the master switch and remove the 7885A
from the subbase.
b.
Close the master switch and push the Start
Switch to energize only the ignition transformer.
c.
If the ignition spark is not strong and continuous,
release the Start Switch, open the master switch,
and adjust the ignition electrode spark gap setting
to the manufacturer recommendations.
d.
Make sure the ignition electrodes are clean.
e.
Close the master switch, press the Start Switch,
and observe the spark.
f.
After a continuous spark is obtained, release the
Start Switch and open the master switch. Add a
jumper from the subbase terminal 10 to the pilot
terminal 8.
g.
Close the master switch and press the Start
Switch to energize both the ignition transformer
and the pilot valve.
h.
If the pilot does not ignite and if the ignition spark
is still continuous, adjust the pressure regulator
until a pilot is established.
i.
When the pilot ignites properly and stays ignited,
release the Start Switch, open the master switch,
and remove the jumper from terminals 8 through
10 of the subbase.
j.
Check for adequate bleeding of the fuel line.
k.
Reinstall the 7885A on the subbase, close the
master switch, and repeat step 3.
5. When the pilot ignites, release the Start Switch and
measure the flame signal. If the pilot flame signal is
unsteady or approaching the 1.25 Vdc minimum value,
adjust the pilot flame size or detector sighting to provide
a maximum and steady flame signal.
6. Press the Stop Switch. Restart the system to recheck
lightoff and the pilot flame signal.
7. When the MAIN LED is energized, make sure the
automatic main fuel valve is open; then smoothly open
the manual main fuel shutoff valve(s) and watch for
main burner flame ignition. When the main burner flame
is established, proceed to step 13.
8. If the main burner flame is not established within five
seconds or the normal lightoff time specified by the
equipment manufacturer, close the manual main fuel
shutoff valve(s).
9. Let the 7885A run with the pilot only for a couple
minutes to allow time for purging unburned fuel from
the combustion chamber. Smoothly open the manual
fuel shutoff valve(s) and try lightoff again. (The first
attempt may have been required to purge the lines and
bring sufficient fuel to the burner.)
10. If the main burner flame is not established within five
seconds or the normal lightoff time specified by the
equipment manufacturer, close the manual main fuel
shutoff valves(s). Check all burner adjustments.
11. If the main burner flame is not established after two
attempts:
a.
Check for improper pilot size.
b.
Check for excess combustion air.
c.
Check for adequate fuel flow.
d.
Check for proper gas supply pressure.
e.
Check for proper valve operation.
f.
Check for proper pilot flame positioning.
12. Repeat steps 6 and 7 to establish the main burner
flame; then proceed to step 13.
13. With the sequence in RUN, make burner adjustments
for flame stability and BTU input rating.
14. Shut down the system by pressing the Stop Switch.
Make sure the main flame goes out. There may be a
delay due to gas trapped between the valve(s) and the
burner. Make sure all automatic fuel valves close.
15. Restart the system by pressing the Start Switch.
Observe that the pilot and main burners light properly.
Lightoff should occur within the time specified by the
equipment manufacturer.
16. Measure the flame signal. Continue to check for the
proper signal through the RUN period; see Table 5.