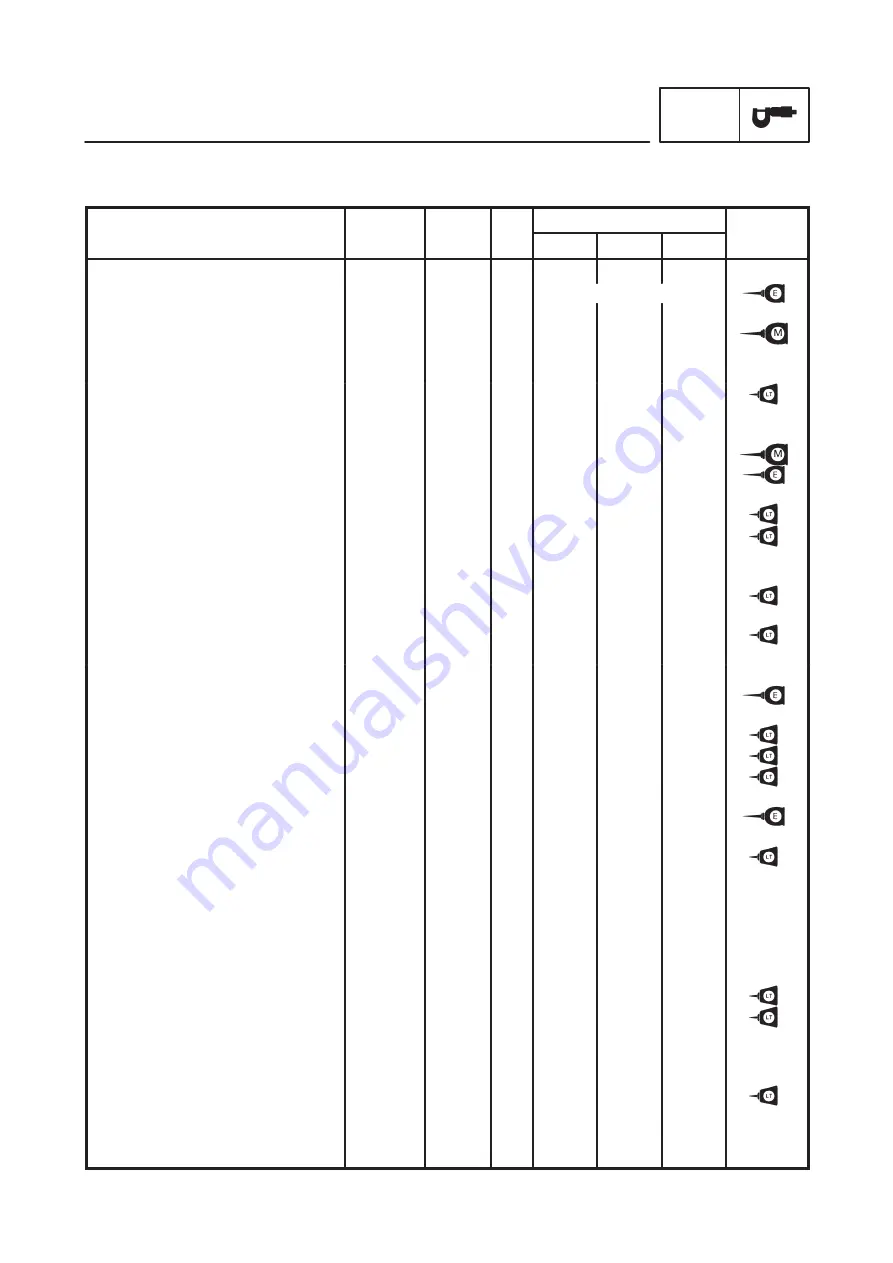
2-19
TIGHTENING TORQUES
SPEC
Use a lock
washer
TIGHTENING TORQUES
ENGINE TIGHTENING TORQUES
Item
Fastener
Thread
Q’ty
Tightening torque
Remarks
Item
Fastener
size
Q ty
Nm
m
S
kg
ft
S
lb
Remarks
Spark plugs
—
M10
4
13
1.3
9.4
Cylinder head
Nut
M10
10
See NOTE 1
Bolt
M6
2
12
1.2
8.7
Camshaft caps
Bolt
M6
28
10
1.0
7.2
Cylinder head cover
Bolt
M6
6
12
1.2
8.7
Cylinder head (exhaust pipe)
Stud bolt
M8
8
15
1.5
11
Air indication system cap
Bolt
M6
4
10
1.0
7.2
Camshaft sprockets
Bolt
M7
4
24
2.4
17
Cylinder head and throttle body
Clamp
M5
4
3
0.3
2.2
Connecting rod caps
Bolt
M8
8
20+150
_
2.0+150
_
14+150
_
Generator rotor
Bolt
M10
1
60
6.0
43
Timing chain tensioner
Bolt
M6
2
10
1.0
7.2
Water pump outlet pipe
Bolt
M6
1
10
1.0
7.2
Water pump inlet pipe
Bolt
M6
1
10
1.0
7.2
(water pump side)
Water pump inlet pipe (front side)
Bolt
M6
1
10
1.0
7.2
Oil/ water pump assembly
sprocket
Bolt
M6
1
15
1.5
11
Water pump
Bolt
M6
2
12
1.2
8.7
Thermostat cover
Nut
M6
2
10
1.0
7.2
Thermostat inlet pipe
Bolt
M6
1
10
1.0
7.2
Oil cooler
Bolt
M20
1
63
6.3
46
Engine oil drain bolt
Bolt
M14
1
43
4.3
31
Oil pipe
Bolt
M6
2
10
1.0
7.2
Oil strainer
Bolt
M6
3
10
1.0
7.2
Oil delivery pipe
Bolt
M6
3
10
1.0
7.2
Oil filter union bolt
Bolt
M20
1
70
7.0
51
Oil filter
—
M20
1
17
1.7
12
Oil pan
Bolt
M6
14
12
1.2
8.7
Oil pan
Bolt
M6
1
12
1.2
8.7
Air filter case cover
Screw
M5
10
1.7
0.17
1.2
Throttle body and throttle body
joint
Clamp
M5
4
3
0.3
2.2
Throttle body and funnel
Bolt
M5
6
4.2
0.42
3.0
Throttle cable
Nut
M6
1
4.5
0.45
3.3
Throttle cable adjuster
Bolt
M6
1
4.5
0.45
3.3
Stator coil
Screw
M6
3
14
1.4
10
Generator rotor cover and
bearing housing
Screw
M6
3
10
1.0
7.2
Pull lever cover
Bolt
M6
2
10
1.0
7.2
Thermostat assembly stay
Bolt
M6
2
10
1.0
7.2
Starter clutch idler gear
Bolt
M6
1
10
1.0
7.2
Clutch boss
Nut
M20
1
95
9.5
69
Stake
Clutch spring
Bolt
M6
6
10
1.0
7.2
Drive sprocket
Nut
M22
1
85
8.5
61
20
Summary of Contents for YZF-R1 2004
Page 1: ...Yamaha Motor Co Ltd 2004 YZF R1 S 5VY1 SE1 SERVICE INFORMATION ...
Page 50: ...YZF R1 S 2004 WIRING DIAGRAM ...
Page 51: ......