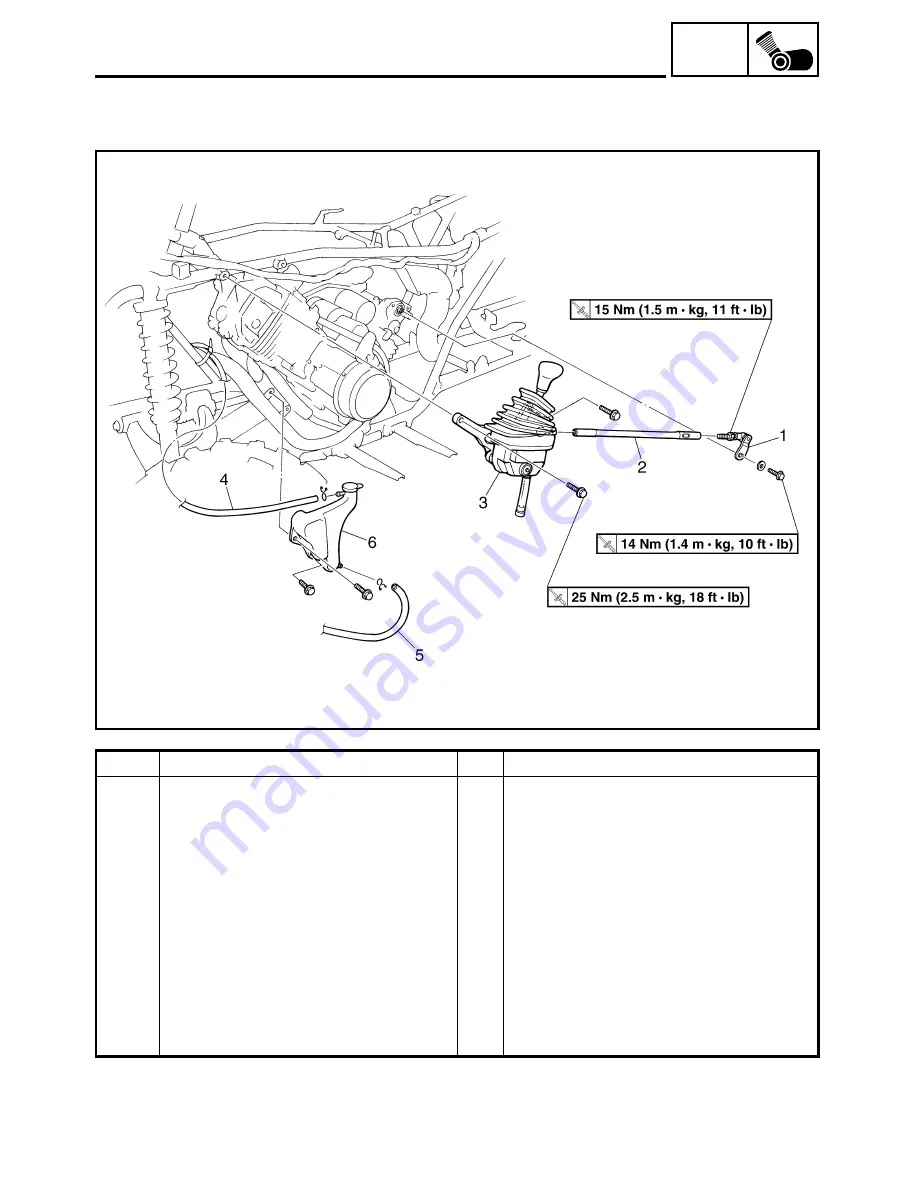
4 - 3
ENG
ENGINE REMOVAL
SELECT LEVER UNIT AND COOLANT RESERVOIR
Order
Job name/Part name
Q’ty
Remarks
Removing the select lever unit and
coolant reservoir
Remove the parts in the order below.
Coolant Drain.
Refer to “CHANGING THE COOLANT” in
CHAPTER 3.
1
Shift arm
1
2
Select lever shift rod
1
3
Select lever unit
1
4
Coolant reservoir breather hose
1
5
Coolant reservoir hose
1
6
Coolant reservoir
1
For installation, reverse the removal
procedure.
Summary of Contents for YFM660FS
Page 1: ...LIT 11616 17 14 5KM 28197 E2 YFM660FS SUPPLEMENTARY SERVICE MANUAL ...
Page 17: ...YAMAHA MOTOR CO LTD 2500 SHINGAI IWATA SHIZUOKA JAPAN PRINTED IN U S A ...
Page 19: ......
Page 20: ......
Page 21: ......
Page 22: ......
Page 23: ......
Page 24: ......
Page 25: ......
Page 26: ......
Page 27: ......
Page 28: ......
Page 29: ......
Page 30: ......
Page 31: ......
Page 32: ......
Page 33: ......
Page 34: ......
Page 35: ......
Page 36: ......
Page 37: ......
Page 38: ......
Page 39: ......
Page 40: ......
Page 41: ......
Page 42: ......
Page 43: ......
Page 44: ......
Page 45: ......
Page 46: ......
Page 47: ......
Page 48: ......
Page 49: ......
Page 50: ......
Page 51: ......
Page 52: ......
Page 53: ......
Page 54: ......
Page 55: ......
Page 56: ......
Page 57: ......
Page 58: ......
Page 59: ......
Page 60: ......
Page 61: ......
Page 62: ......
Page 63: ......
Page 64: ......
Page 65: ......
Page 66: ......
Page 67: ......
Page 68: ......
Page 69: ......
Page 70: ......
Page 71: ......
Page 72: ...YFM660FP SERVICEMANUAL LIT 11616 15 01 5KM 28197 E0 ...
Page 117: ...2 11 SPEC MAINTENANCE SPECIFICATIONS Item Standard Cylinder head tightening sequence ...
Page 417: ...9 3 ELEC CHECKING THE SWITCH ...
Page 478: ...YAMAHA MOTOR CO LTD 2500 SHINGAI IWATA SHIZUOKA JAPAN PRINTED IN U S A ...