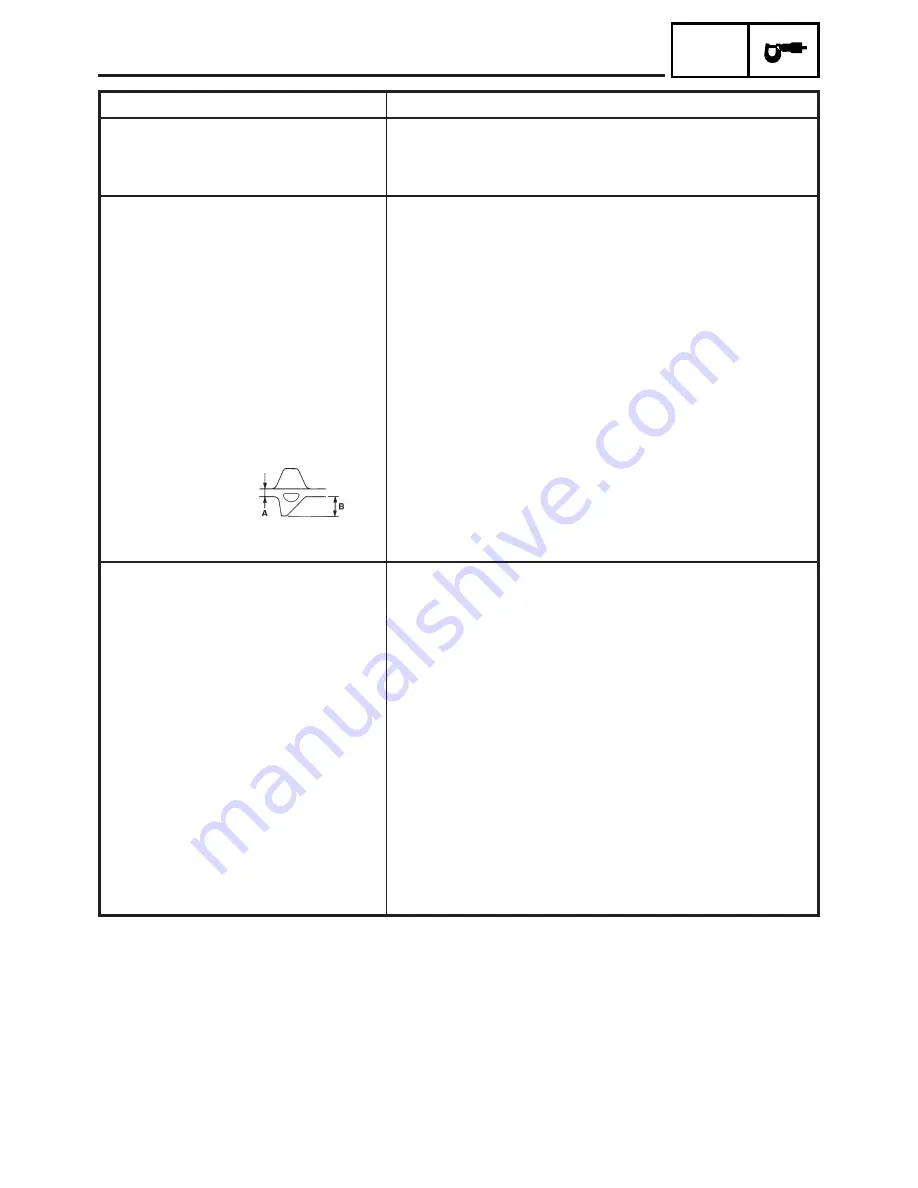
SPEC
9-9
MAINTENANCE SPECIFICATIONS
Model
Drive chain:
Type
Number of links
Track:
Part number
Width
Length
Pitch
Number of links
Thickness “A”
Height “B”
Track deflection at 10 kg (22 lb)
Slide rail suspension (Rear suspension):
Travel
Suspension spring rate
Front
Rear
Spring wire diameter
Front
Rear
VX700/VX700DX/SX700/MM700/VT700
REXNORD S37TNB13
70 L (VX700/VX700DX/SX700/MM700) (VT700 for U.S.A./Canada)
68 L (VT700 for Europe)
8EA-47110-10 (VX700/VX700DX/SX700)
8ED-47110-00 (MM700)
8BN-47110-00 (VT700)
381 mm (15.0 in)
3,072 mm (120.9 in) (VX700/VX700DX/SX700)
3,584 mm (141.1 in) (MM700)
3,456 mm (136.1 in) (VT700)
64 mm (2.52 in)
48 (VX700/VX700DX/SX700)
56 (MM700)
54 (VT700)
5.5 mm (0.22 in) (VX700/VX700DX/SX700)
7.25 mm (0.29 in) (MM700)
6.0 mm (0.24 in) (VT700)
23 mm (0.91 in) (VX700/VX700DX/SX700)
50.8 mm (2.00 in) (MM700)
19 mm (0.75 in) (VT700)
25 ~ 30 mm (0.98 ~ 1.18 in) (VX700/VX700DX/SX700/VT700)
20 ~ 25 mm (0.79 ~ 0.98 in) (MM700)
292 mm (11.5 in)
19.6 N/mm (2.0 kg/mm, 112 lb/in) (VX700/VX700DX)
14.8 ~ 24.5 N/mm (1.5 ~ 2.5 kg/mm, 84 ~ 140 lb/in) (SX700)
29.4 N/mm (3.0 kg/mm, 168 lb/in) (MM700)
14.7 N/mm (1.5 kg/mm, 84 lb/in) (VT700)
29.4 ~ 44.1 N/mm (3.0 ~ 4.5 kg/mm, 168 ~ 252 lb/in) (VX700/VX700DX)
22.44 ~ 47.04 N/mm (2.3 ~ 4.8 kg/mm, 129 ~ 269 lb/in) (SX700)
22.54 ~ 42.14 N/mm (2.3 ~ 4.3 kg/mm, 129 ~ 241 lb/in) (MM700)
34.3 ~ 51.94 N/mm (3.5 ~ 5.3 kg/mm, 196 ~ 297 lb/in) (VT700)
6.5 mm (0.26 in) (VX700)
7.8 mm (0.31 in) (VX700DX/SX700/VT700)
8.2 mm (0.32 in) (MM700)
11.5 mm (0.452 in) (VX700/VX700DX)
11.4 mm (0.448 in) (SX700)
10.8 mm (0.425 in) (MM700)
12.0 mm (0.472 in) (VT700)
Summary of Contents for SXV70SJ
Page 1: ......
Page 52: ... 46 CARBURETORS CARB 7 ...
Page 70: ... 64 SELF DIAGNOSIS ELEC ...
Page 90: ... 84 SPEC ...
Page 91: ... 85 CABLE ROUTING SPEC ...
Page 93: ... 87 CABLE ROUTING SPEC ...
Page 95: ... 89 CABLE ROUTING SPEC ...
Page 97: ... 91 CABLE ROUTING SPEC ...
Page 99: ... 93 CABLE ROUTING SPEC ...
Page 101: ... 95 CABLE ROUTING SPEC ...
Page 103: ... 97 CABLE ROUTING SPEC ...
Page 105: ... 99 CABLE ROUTING SPEC ...
Page 107: ... 101 CABLE ROUTING SPEC ...
Page 109: ... 103 CABLE ROUTING SPEC ...
Page 111: ... 105 CABLE ROUTING SPEC ...
Page 117: ......
Page 118: ......
Page 119: ......
Page 120: ...VX700F VX700DXF SX700F MM700F VT700F SERVICE MANUAL LIT 12618 02 17 8CH 28197 10 981050 ...
Page 175: ...2 42 INSP ADJ CARBURETOR TUNING Guide for carburetion SCH2815 ...
Page 351: ...8 35 ELEC ...
Page 383: ...9 22 SPEC ...
Page 384: ...SPEC 9 23 CABLE ROUTING SCH9010 ...
Page 386: ...SPEC 9 25 CABLE ROUTING SCH9010 ...
Page 388: ...SPEC 9 27 CABLE ROUTING SCH9020 ...
Page 390: ...SPEC 9 29 CABLE ROUTING SCH9030 ...
Page 392: ...SPEC 9 31 CABLE ROUTING SCH9030 ...
Page 394: ...SPEC 9 33 CABLE ROUTING SCH9040 ...
Page 396: ...SPEC 9 35 CABLE ROUTING SCH9050 ...
Page 398: ...SPEC 9 37 CABLE ROUTING SCH9050 ...
Page 400: ...SPEC 9 39 CABLE ROUTING SCH9060 ...
Page 404: ...00 06 0 8 E CR PRINTED ON RECYCLED PAPER ...
Page 405: ......
Page 406: ......
Page 407: ......
Page 408: ......
Page 409: ......
Page 410: ......
Page 411: ......
Page 412: ......
Page 413: ......
Page 414: ......
Page 415: ......
Page 416: ......
Page 417: ......
Page 418: ......
Page 419: ......
Page 420: ......
Page 421: ......
Page 422: ......
Page 423: ......
Page 424: ......
Page 425: ......
Page 426: ......
Page 427: ......
Page 428: ......
Page 429: ......
Page 430: ......
Page 431: ......
Page 432: ......
Page 433: ......
Page 434: ......
Page 435: ......
Page 436: ......
Page 437: ......
Page 438: ......
Page 439: ......
Page 440: ......
Page 441: ......
Page 442: ......
Page 443: ......
Page 444: ......
Page 445: ......
Page 446: ......
Page 447: ......
Page 448: ......
Page 449: ......
Page 450: ......
Page 451: ......
Page 452: ......
Page 453: ......
Page 454: ......
Page 455: ......
Page 456: ......
Page 457: ......
Page 458: ......
Page 459: ......
Page 460: ......
Page 461: ......
Page 462: ......
Page 463: ......
Page 464: ......
Page 465: ......
Page 466: ......
Page 467: ......
Page 468: ......
Page 469: ......
Page 470: ......
Page 471: ......
Page 472: ......
Page 473: ......
Page 474: ......
Page 475: ......
Page 476: ......
Page 477: ......
Page 478: ......
Page 479: ......
Page 480: ......
Page 481: ......
Page 482: ......
Page 483: ......
Page 484: ......
Page 485: ......
Page 486: ......
Page 487: ......
Page 488: ......
Page 489: ......
Page 490: ......
Page 491: ......
Page 492: ......
Page 493: ......
Page 494: ......
Page 495: ......
Page 496: ......
Page 497: ......
Page 498: ......
Page 499: ......
Page 500: ......
Page 501: ......
Page 502: ......
Page 503: ......
Page 504: ......
Page 505: ......
Page 506: ......
Page 507: ......
Page 508: ......
Page 509: ......
Page 510: ......
Page 511: ......
Page 512: ......
Page 513: ......
Page 514: ......
Page 515: ......
Page 516: ......
Page 517: ......
Page 518: ......
Page 519: ......
Page 520: ......
Page 521: ......
Page 522: ......
Page 523: ......
Page 524: ......
Page 525: ......
Page 526: ......
Page 527: ......
Page 528: ......
Page 529: ......
Page 530: ......
Page 531: ......
Page 532: ......
Page 533: ......
Page 534: ......
Page 535: ......
Page 536: ......
Page 537: ......
Page 538: ......
Page 539: ......
Page 540: ......
Page 541: ......
Page 542: ......
Page 543: ......
Page 544: ......
Page 545: ......
Page 546: ......
Page 547: ......
Page 548: ......
Page 549: ......
Page 550: ......
Page 551: ......
Page 552: ......
Page 553: ......
Page 554: ......
Page 555: ......
Page 556: ......
Page 557: ......
Page 558: ......
Page 559: ......
Page 560: ......
Page 561: ......
Page 562: ......
Page 563: ......
Page 564: ......
Page 565: ......
Page 566: ......
Page 567: ......
Page 568: ......
Page 569: ......
Page 570: ......
Page 571: ......
Page 572: ......
Page 573: ......
Page 574: ......
Page 575: ......
Page 576: ......