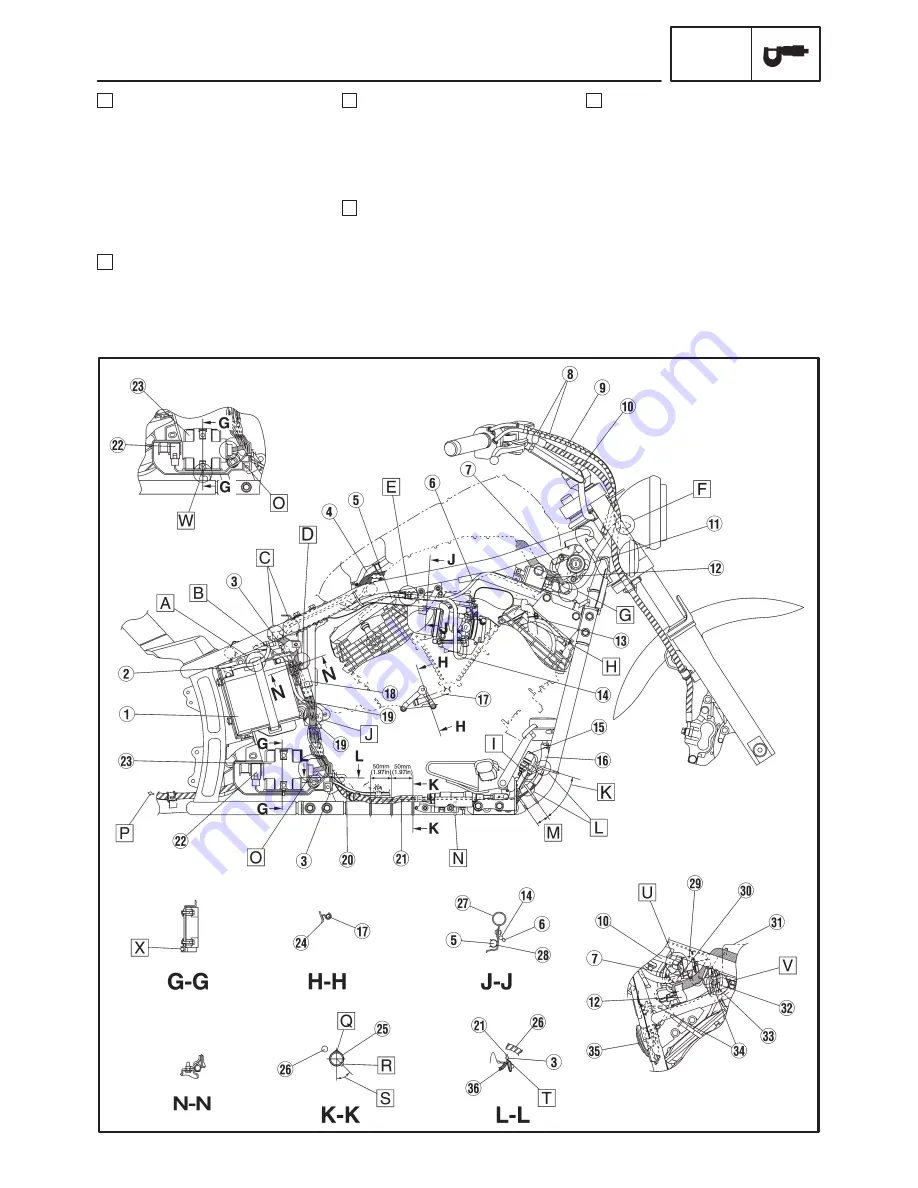
–11–
T Fasten the oil level sensor lead
with a locking tie to battery box.
Fix to the battery box with the
band. To fix, align the band to the
bottom of the box’s hole while fix-
ing the lead to the back of the box
(inside the body). The cutting part
at the edge of the band comes to
the front side of the body.
U Clamp the handlebar switch lead
(right) to the frame with a holder.
The part to open and shut is out-
side of the body.
CABLE ROUTING
SPEC
V Arrange the throttle position sen-
sor connector, carburetor heater
connector and thermo switch
connector between the starting
circuit cut off relay and high ten-
sion code.
W Secure to the battery box with
the band, cut the surplus section
and then point the locking sec-
tion to the regulator side.
X Push the light reduce lead and
the terminal-coupler lead for the
carburetor heater into the deep-
est position in the groove of the
battery box.
Summary of Contents for 5KSJ
Page 1: ......
Page 38: ...PRINTED IN U S A ...