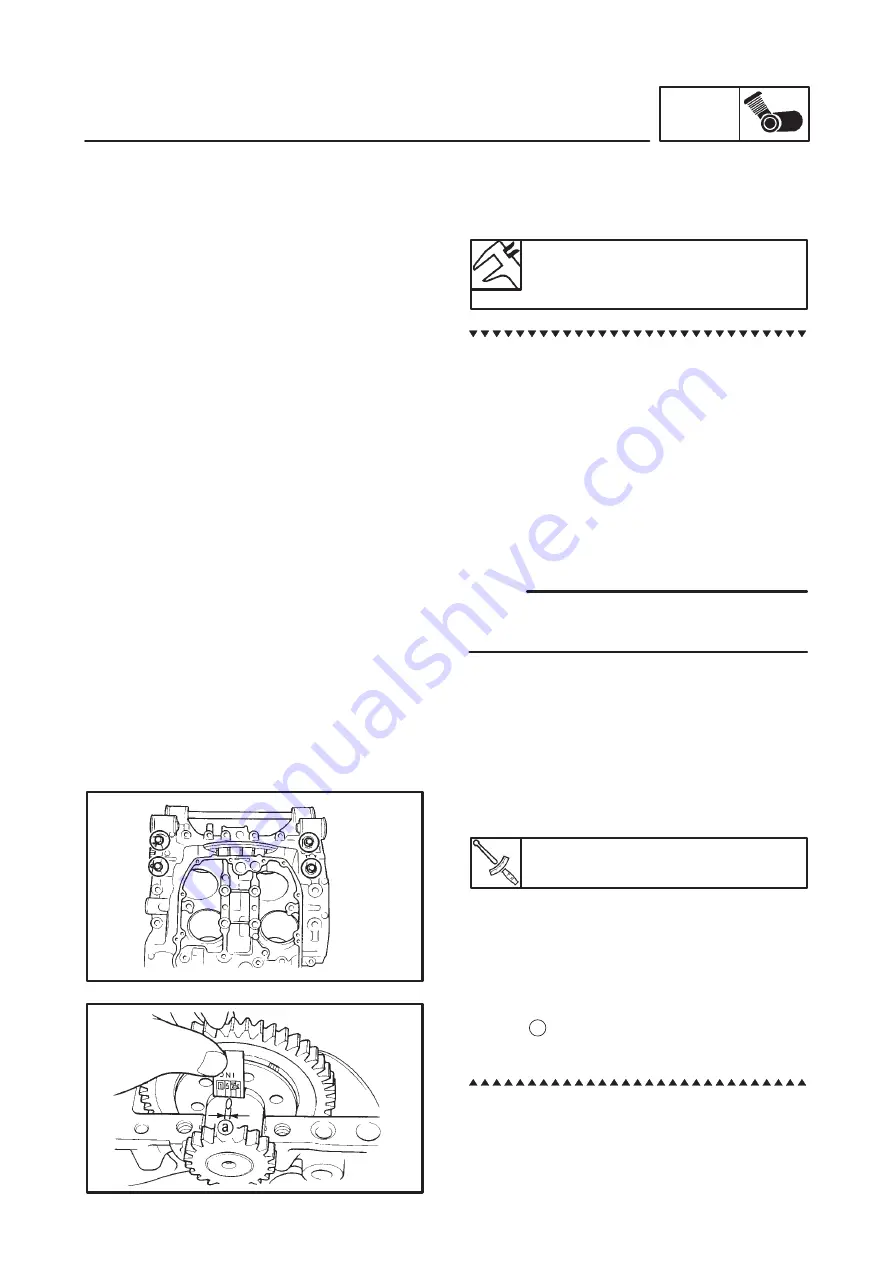
–11–
E
INSPECTION AND REPAIR
ENG
NOTE:
BALANCER SHAFT
1. Measure:
S
Oil clearance (balancer shaft bearing)
Out of specification
Replace bearing.
Oil clearance:
0.020
0.048 mm
(0.0008
0.002 in)
Measurement steps:
F
Clean the bearings, balancer shaft and bear-
ing portions of the crankcase.
F
Place the crankcase (upper) on a bench in an
upside down position.
F
Install the upper half of the bearings and the
balancer shaft into the crankcase (upper).
F
Put a piece of Plastigauge
on each balanc-
er shaft journal.
F
Install the lower half of the bearings into the
crankcase (lower) and assemble the crank-
case halves.
Do not move the balancer shaft until the oil
clearance measurement has been completed.
F
Tighten the bolts to specification in the tight-
ening sequence cast on the crankcase.
Bolt (crankcase-M8):
24 Nm (2.4 m
S
kg, 17 ft
S
lb)
F
Remove the crankcase (lower) and lower half
of the bearings.
F
Measure the compressed Plastigauge
width
a
on each balancer shaft journal. If oil
clearance is out of specification, select a re-
placement bearing.