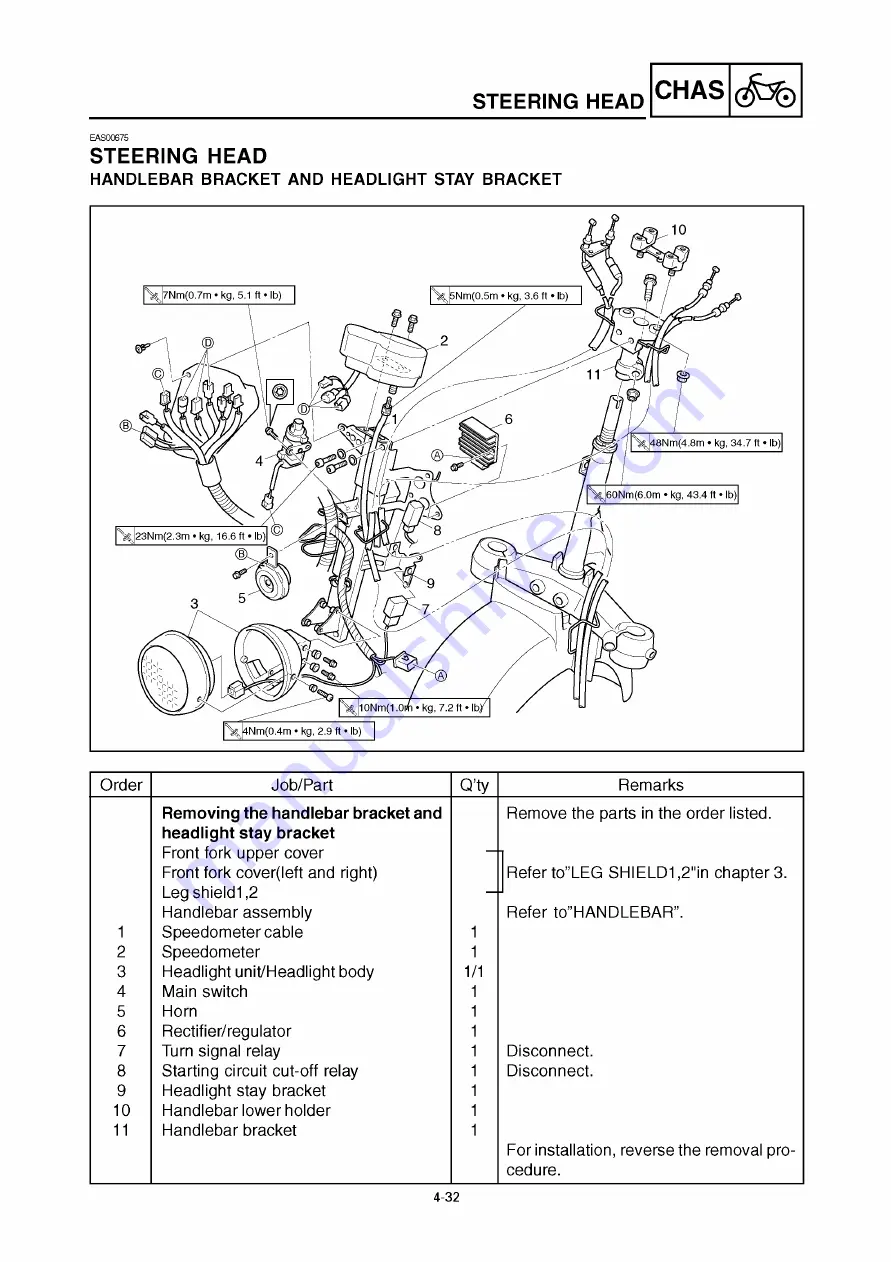
STEERING HEAD
CHAS (3^3^)
EAS00675
STEERING HEAD
HANDLEBAR BRACKET AND HEADLIGHT STAY BRACKET
®~.
S^
>
48Nm(4.8m • kg, 34.7 ft • lb)
S^60Nm(6.0m • kg, 43.4 ft • lb)
P^23Nm(2.3m kg, 16.6 ft lb)
al4Nm(0.4m • kg, 2.9 ft • lb)
Order
Job/Part
Q’ty
Remarks
1
2
3
4
5
6
7
8
9
10
11
Removing the handlebar bracket and
headlight stay bracket
Front fork upper cover
Front fork cover(left and right)
Leg shield1,2
Handlebar assembly
Speedometer cable
Speedometer
Headlight unit/Headlight body
Main switch
Horn
Rectifier/regulator
Turn signal relay
Starting circuit cut-off relay
Headlight stay bracket
Handlebar lower holder
Handlebar bracket
1
1
1/1
1
1
1
1
1
1
1
1
Remove the parts in the order listed.
Refer to”LEG SHIELD1,2"in chapter 3.
Refer to”HANDLEBAR”.
Disconnect.
Disconnect.
For installation, reverse the removal pro-
cedure.
4-32
Downloaded
from
www.ScooterTime.net