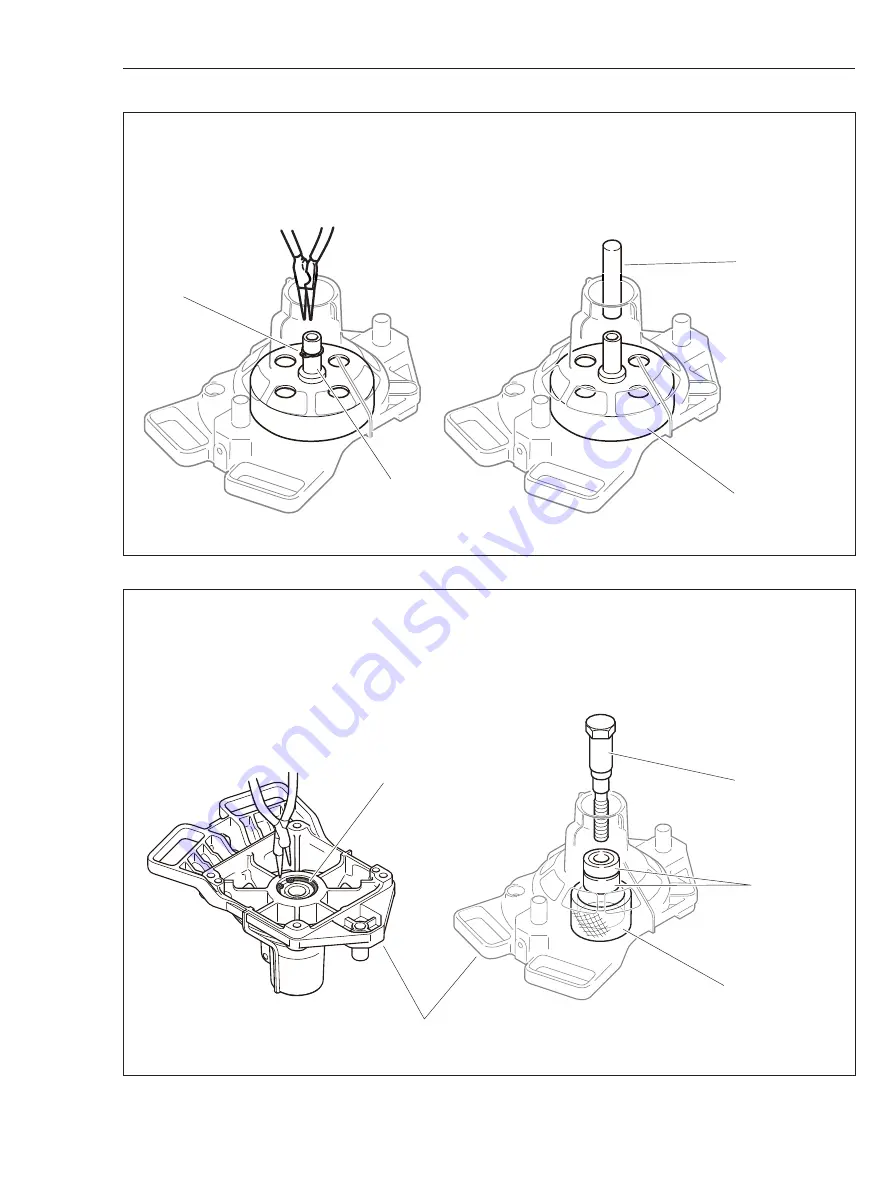
39
SRM-420ES, SRM-420TES
T410S, B410S
T410TS, B410TS
CLUTCH SYSTEM
39
5-4 Removing clutch drum bearings
1. Remove retaining ring (A) from clutch case (B).
2. Remove two ball bearings (C) together from
clutch case (B) using shaft (D) and boss (E) of
bearing tool 897701-14732 as shown.
5-3 Removing clutch drum
1. Remove retaining ring (A) from clutch drum
shaft (b) using needle nose pliers.
2. Push out clutch drum (B) using press machine
with 12 mm (0.47 in.) diameter pusher (C).
A
B
C
b
A
D
B
C
E