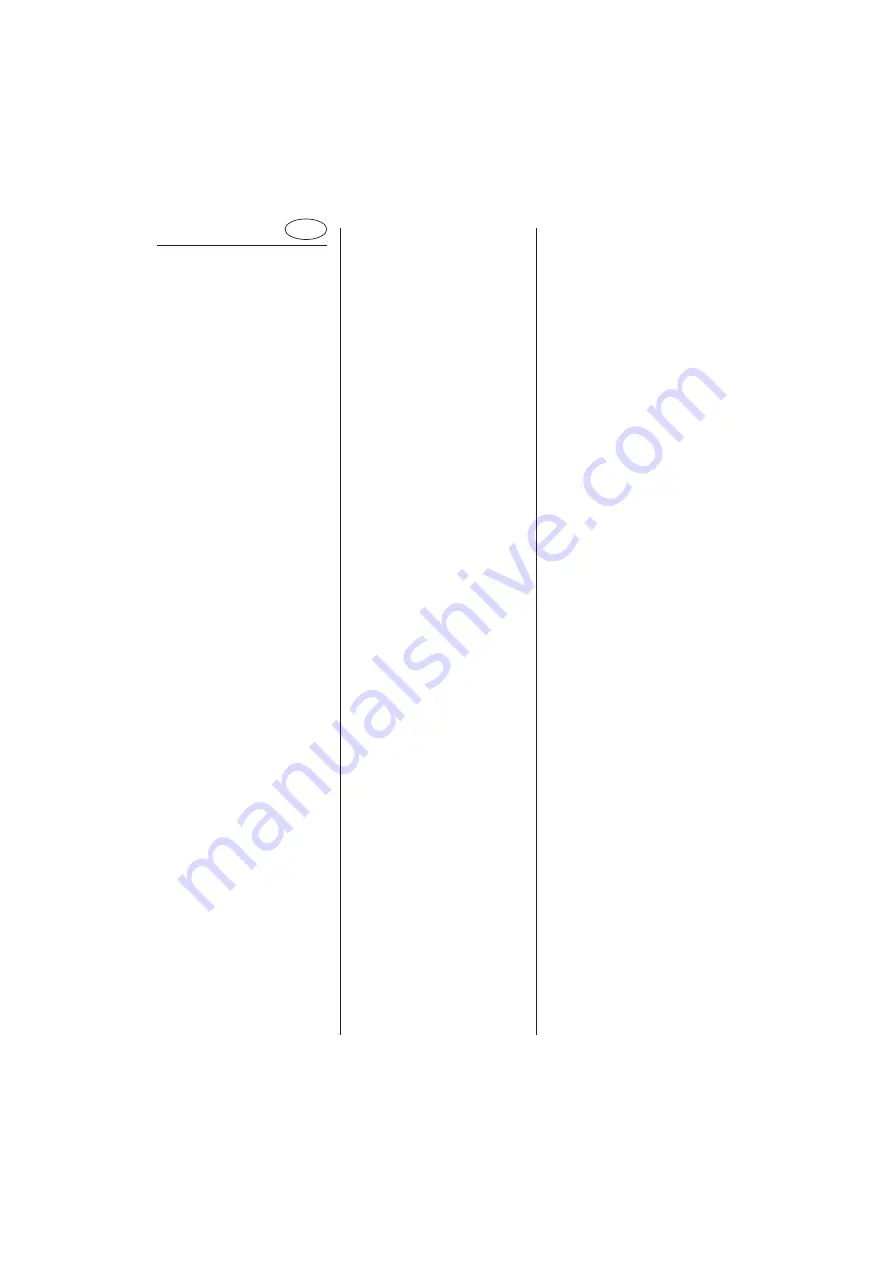
English
INTRODUCTION
All users must read these operating instruc-
tions carefully prior to the initial operation.
These instructions are intended to acquaint
the user with the lifting tackle and enable him
to use it to the full extent of its intended capa-
bilities. The operating instructions contain
important information on how to handle the
lifting tackle in a safe, correct and economic
way. Acting in accordance with these instruc-
tions helps to avoid dangers, reduce repair
cost and down time and to increase the relia-
bility and lifetime of the lifting tackle. This op-
erating instruction must always be available
for consultation in the area where the lifting
tackle is in operation. Apart from the operat-
ing instructions and the accident prevention
act valid for the respective country and area
where the lifting tackle is being used, also the
commonly accepted regulations for safe and
professional work must be adhered to.
CORRECT OPERATION
- The capacity indicated on the lifting tackle
is the maximum safe working load limit
(W.L.L.) which must not be exceeded.
- Do not lift or transport loads while
personnel are in the danger zone.
- Do not allow personnel to pass under a
suspended load.
- After lifting a load it must not be left unat-
tended for a longer period of time.
- The operator must position the clamp so that
it can be operated without the clamp, lifting
slings or load posing a danger to himself or
other personnel.
- The clamp can be used in ambient temper-
atures between –10
°
C and +50
°
C.
For extreme temperatures outside this range
please first contact the manufacturer.
- The accident prevention act and safety
regulations valid in the country of operation
are to be strictly adhered to at all times.
- If defects are found, stop using the clamp
immediately.
- The load must be hung in the centre of the
suspension bar. Side pull is forbidden as it
damages the side plates. Always lift, lower
or pull in a straight line between suspension
point and load attachment point.
INCORRECT OPERATION
- Do not exceed the rated lifting capacity
(W.L.L.).
- Do not tamper with lifting tackle.
- It is forbidden to use the clamp for trans-
porting personnel.
GB
- Welding on the clamp is strictly forbidden
(Fig. 1).
- It is forbidden to apply side-pull forces to the
clamp (Fig. 2).
- Incorrect attachment to, or incorrect loading
of the suspension bar by side pull (Fig. 3) or
by using the beam clamp as a clamping jaw
is not allowed.
- Do not let the lifting tackle fall from a great
height.
INSPECTION BEFORE INITIAL
OPERATION
A competent person must inspect each clamp
prior to its initial operation. The inspection is
visual and functional and shall establish that
the clamp is in a safe condition resp. that any
defects found can be corrected before opera-
tion commences.
A service engineer, a representative of the
manufacturer or the supplier, can make the
inspection although the company can assign
its own suitably trained personnel.
INSPECTIONS BEFORE STARTING
WORK
Before starting work inspect the beam clamp
and all load bearing constructions every time
for visual defects. The selection and calculation
of suitable carrying beams is the responsibility
of the user.
Inspection of the beam clamp
Inspect the beam clamp and visually check
for external defects, deformations, superficial
cracks, wear or corrosion marks.
Inspection of beam clamp attachment
The beam clamp jaws should completely grip
the profile so that the load is on the top of the
beam flange and not on the edge.
USING THE CLAMP
The beam clamp jaws are opened wide enough
to pass over the beam profile (Fig. 4). By
turning the spindle in the opposite direction,
the jaws close and clasp the beam flange. The
beam clamp jaws must completely grip the
profile so that the load is on the top of the
beam flange and not on the edge.
To ensure the clamp remains tightly clamped
and be locked against unintended loosening,
the set screw which is fitted in the longitudinal
axis of the tensioning nut (Fig 5, item 11), must
be tightened. A copper flat on the tip of the
set screw prevents damage to the spindle.
When removing the beam clamp the set screw
has to be loosened first.
The load must be hung in the centre of the
suspension bar.
3
INSPECTIONS AND SERVICE
Inspections are to be made by a competent
person at least once annually unless adverse
working conditions dictate shorter periods. The
clamp is to be inspected for damage, wear,
corrosion or other irregularities and all safety
devices have to be checked for completeness
and effectiveness.
Repairs may only be carried out by specialist
workshops that use original Yale spare parts.
Inspections are instigated by the user.