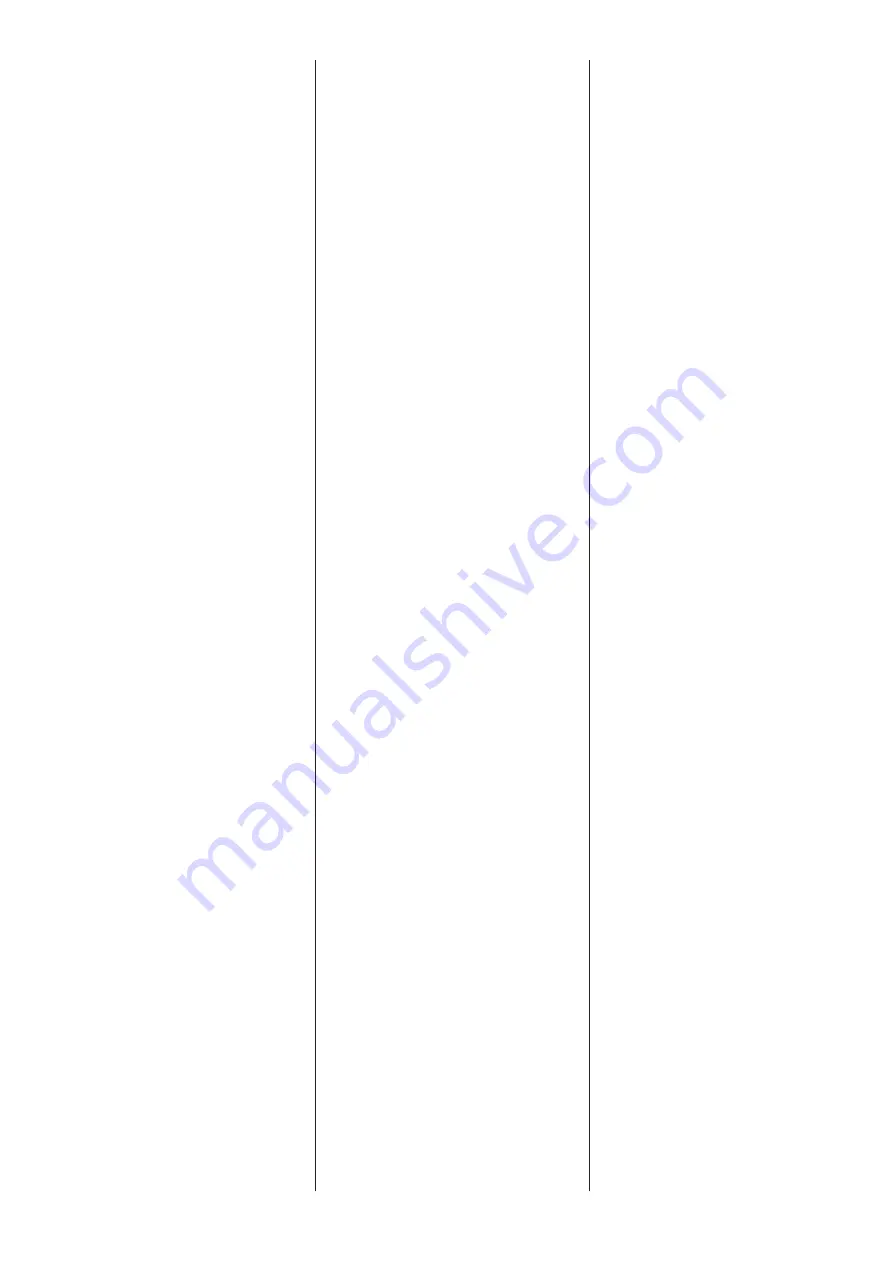
6 von 16
Actuate the handle with the required speed.
Make sure the handle is secured against
being pulled out.
ATTENTION:
For safe operation never fully
unwind the wire rope under load. Always leave
at least 3 turns of the rope on the rope drum
in order to prevent the rope from being pulled
off the rope drum.
Releasing a load
Position control lever A as shown in the left
fi gure (see Fig. 13). Press the handle to the ex-
treme lowest position until the load is removed
from the brake pawl B. As the handle is slowly
released, the load will be released one notch.
Releasing the wire rope,
unloaded condition
To release the wire rope, position control lever
A as shown in the right fi gure (see Fig. 14)
and hold the spring-loaded brake pawl B as
shown. The wire rope can now be pulled freely
through the unit to achieve quick and precise
attachment of the load. In the same way, with
control lever A in the illustrated position, the
unloaded wire rope can be rewound onto the
drum with the hand wheel.
Replacing the rope
- Only original Yale ropes with the nominal
diameter suitable for the hoist may be used.
- Roll the rope to be replaced off the rope
drum. To do this, release the rope.
- Loosen the grub screw to pull out the rope
end fi xed inside the drum.
- Lead the free end of the new rope into the
opening on the rope drum until it is safely
clamped after the grub screw is screwed in
and carefully tightened.
INSPECTION, MAINTENANCE AND
REPAIR
According to national and international acci-
dent prevention and safety regulations hoisting
equipment must be inspected:
• in accordance with the risk assessment of
the operating company,
• prior to initial operation,
• before the unit is put into service again
following a shut down,
• after substantial changes,
• however, at least once per year, by a
competent person.
ATTENTION:
Actual operating conditions
(e.g. operation in galvanizing facilities) can
dictate shorter inspection intervals.
Repair work may only be carried out by a spe-
cialist workshop that uses original Yale spare
parts. The inspection (mainly consisting of a
visual inspection and a function check) must
determine that all safety devices are complete
ATTENTION:
When the hoist is used in
combination with return pulleys (pulley block
principle), a multiple of the load weight may
act on the supporting structure!
Inspection of the rope
ATTENTION:
Always wear protection gloves
for handling wire ropes.
Check the rope for outer defects, deforma-
tions, kinks, broken individual wires or strands,
crushing, swelling, rust damage (e.g. corrosion
marks), strong overheating and heavy wear
of the rope end connections (e.g. pressure
sleeve). Rope damage may result in malfunc-
tions and lasting damage to the cable puller.
Protruding, broken wires may cause injuries.
If slight damage (not yet resulting in discard-
ing of the rope) is determined, the inspection
intervals must be shortened.
Inspection of the top hook and
load hook
The top and load hooks must be checked
for cracks, deformations, damage, wear and
corrosion marks. The safety latch must move
freely and be fully functioning.
OPERATION
Single or double-fall operation
Before each operation, clarify whether the
cable puller is to be used for single or double-
fall operation. Double-fall operation off ers
the possibility of double the pulling capacity
(see Tab. 1).
- For single-fall operation the load to be
pulled/tensioned is attached to the clevis
hook (see Fig. 9).
- For double-fall operation the clevis hook is
attached on the rope end in the eyebolt at
the bottom of the cable puller and the load
to be pulled/tensioned in the hook of the
bottom bloc (see Fig. 10).
Pulling/tensioning a load
The main element is a double interlocking
pawl system consisting of the rope drum
with an integrally cast ratchet disc and two
interlocking pawls.
The unloaded wire rope can be quickly
rewound onto the drum by means of a hand
wheel. The handle serves as an overload
check and bends before other components
can become overloaded. The handle can be
inserted from either side into the U-shaped
yoke to facilitate operation in confi ned areas.
Position control lever A as shown in the fi gure
(see Fig. 12). The brake pawl engages against
the ratchet teeth. Operate handle with a
pumping action.
since this may cause malfunctions in the
unit and damage to the rope.
- When ropes are used, it must be ensured
that they are correctly dimensioned. The
principles laid down in DIN 15020 for rope
drive arrangements must be complied with.
- Actuation of the rope release feature is
prohibited when a load is suspended!
- Never reach into moving parts.
- Do not allow the unit to fall from a large
height. Always place it properly on the
ground.
- The unit must not be used in potentially
explosive atmospheres.
INSPECTION BEFORE INITIAL
OPERATION
Prior to initial operation, before it is put
into operation again and after substantial
changes, the product including the supporting
structure must be inspected by a competent
person*. The inspection mainly consists of a
visual inspection and a function check. These
inspections are intended to establish that the
hoist is in a safe condition, has been set up
appropriately and is ready for operation and
that any defects or damage are detected and
eliminated, as required.
*Competent persons may be, for example, the
maintenance engineers of the manufacturer or
the supplier. However, the company may also
assign performance of the inspection to its
own appropriately trained specialist personnel.
ATTENTION:
Always wear protection gloves
for handling wire ropes.
INSPECTIONS BEFORE STARTING
WORK
Before starting work, inspect the unit including
the suspension, equipment and supporting
structure for visual defects, e. g. deforma-
tions, damage, cracks, wear and corrosion
marks. In addition also test functioning of
the locking mechanism and check that the
load is correctly attached. To do this, pull or
tension and release a load again over a short
distance with the unit.
Inspection of the attachment point
- The attachment point for the hoist must be
selected so that the supporting structure to
which it is to be fi tted has suffi
cient stability
and to ensure that the expected forces can
be safely absorbed.
- The unit must align freely also under load
in order to avoid impermissible additional
loading.
- The selection and calculation of the appropri-
ate supporting structure are the responsibil-
ity of the operating company.