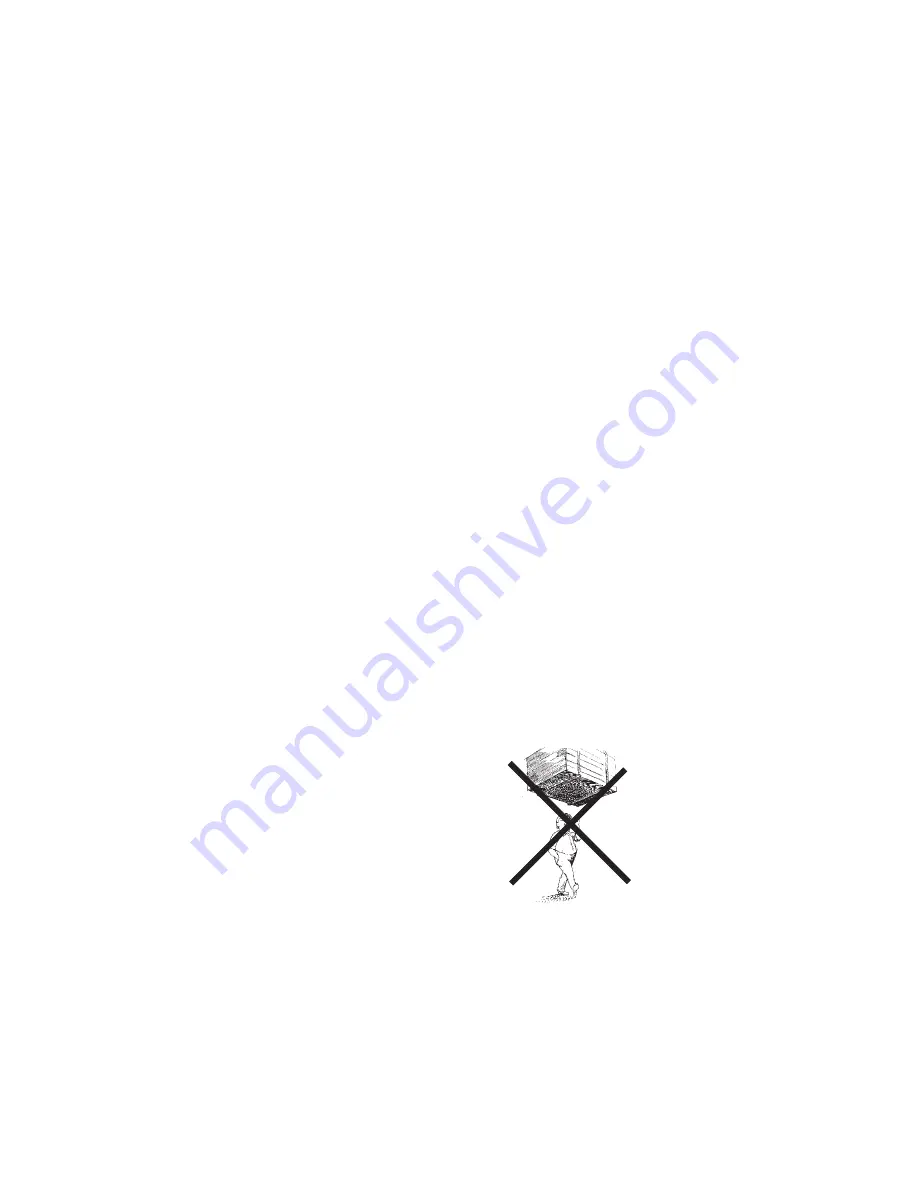
3
1. GENERAL INFORMATION
Attention:
All users must read these operating instructions care-
fully prior to the initial operation. These instructions are intended
to acquaint the user with the hoist/trolley and enable him to use it
to the full extent of its intended capabilities
The operating instructions contain important information on how
to handle the hoist/trolley in a safe, correct and economic way.
Acting in accordance with these instructions helps to avoid dan-
gers, reduce repair costs and down time and to increase the reli-
ability and lifetime of the hoist/trolley. Anyone involved in doing
any of the following work with the hoist/trolley must read the oper-
ating instructions and act accordingly:
operation, including preparation, trouble shooting during opera-
tion and cleaning maintenance, inspection, repair
transport
Apart from the operating instructions and the accident prevention
act valid for the respective country and area where the hoist/trol-
ley is used, also the commonly accepted regulations for safe and
professional work must be adhered to.
Every unit leaving the factory is furnished with a test certificate
showing the serial number of the hoist.
The continuous sound level at the place of work is equal to 75 dB.
The measurement was taken at a distance of 2.2 m from the hoist
in 1 position in accordance with DIN 45635 precision class 2.
2 OPERATING INSTRUCTIONS
2.1 CORRECT OPERATION
Capacity / max. safe working load
The Yale pneumatic chain hoist CPA is designed to lift and lower
loads up to the rated capacity. The lifting capacity indicated on the
hoist is the maximum safe working load which must not be ex-
ceeded.
Danger zones:
Do not lift or transport loads while
personnel are in the danger zone.
Do not allow personnel to pass
under a suspended load.
After lifting or tensioning, a load
must not be left unattended for a
longer period of time.
Start moving the load only after it
has been attached correctly and
all personnel are clear of the
danger zone.
Fig. 2
Attaching the hoist
The operator must ensure that the hoist is attached in a manner
that does not expose himself or other personnel to danger by the
hoist, chain(s) or the load.
INDEX
PAGE
1.
General information
3
2.
Operating instructions
3
2.1 Correct operation
3
Capacity / max. safe working load
3
Danger zones
3
Attaching the hoist
3
Temperature range
4
Regulations
4
Maintenance/repair
4
2.2 Incorrect operation
4
2.3 Commissioning
4
inspection before initial operation
4
Inspection before starting work
4
Inspection of load chain
4
Inspection of chain stop
4
Inspection of chain reeving
4
Inspection of suspension and load hooks
5
Attaching the load
5
Inspecting the traverse (for trolleys)
5
Check adjustment of trolley width
5
3.
Assembly
5
3.1 Inspection before assembly
5
3.2 Pneumatic chain hoist with hook suspension
(Standard design)
5
3.3 Pneumatic chain hoist with trolley
5
Fitting the trolley
6
3.4 Air pressure connections
6
4.
Functional check after assembly
6
5.
Operation
7
Installation, service, operation
7
Traversing the trolley
7
Attaching the load
7
Lifting the load
7
Emergency stop
7
6.
Service
8
6.1 Daily checks
8
6.2 Regular inspections, service, testing
8
6.3 Load chain
9
Lubricating the load chain
9
Inspecting the load chain for wear
9
Replace the load chain
9
Single fall design
9
Two-fall design
9
6.4 Load and suspension hooks
10
6.5 Trolleys
10
6.6 Pneumatic hoists in general
10
6.7 Overload protection device
10
6.8 Gearbox
10
Checkoil level
Oil change
10
Disassemble and reassemble the gearbox
11
6.9 Air motor
12
Motor
12
Disassemble and reassemble the motor
12-13