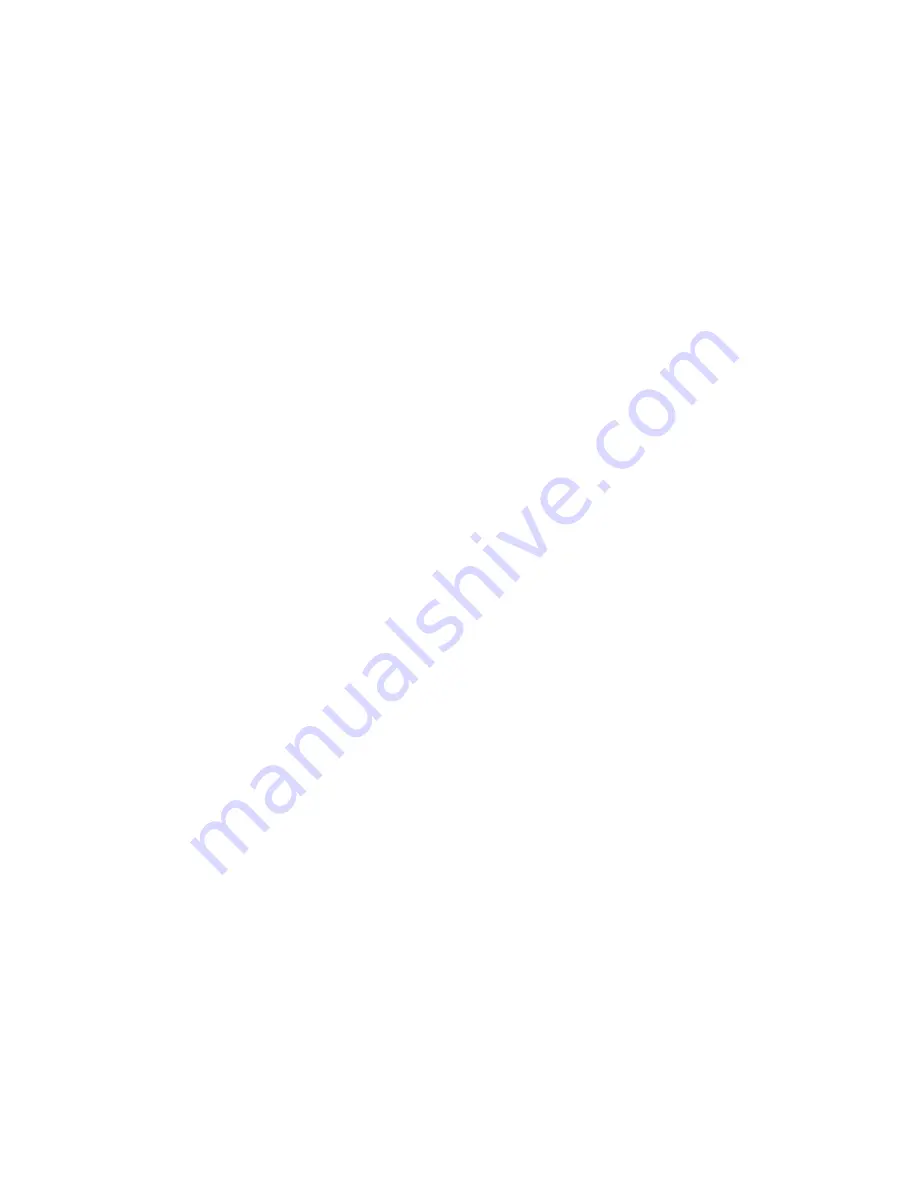
6
2.) Measure the flange width ”b” of the beam.
3.) Adjust the measurement “B” between the shoulders of the
round nuts (pos. 5) on the threaded traverses (pos. 1).
Ensure that the 4 bores in the round nuts face towards the
outside. Adjust the measurement “B” to equal the measure-
ment “b” plus 4 mm. The measurement “A” must be 2 mm on
each side and the suspension traverse must be centred be-
tween the shoulders of the round nuts.
4.) Replace one side plate (pos. 6).
Replace one side plate ensuring that the roll pins in the side
plates engage into the bores in the round nuts. To achieve this
it may be necessary to rotate the round nuts slightly.
5.) Replace the washers (pos. 3) and tighten the securing nuts
(pos. 2). Screw on the locknuts (pos. 8) fingertight and tighten
a further 1/4 to 1/2 turn.
Attention:
The locknuts must always be fitted.
6.) Loosely replace second side plate (pos. 6) on the traverse
(pos. 1):
The washers (pos. 3), security nuts (pos. 2) and locknuts (pos.
8) can be fitted loosely.
7.) Raise the complete pre-assembled trolley to the carrying
beam.
8.) Engage the second side plate ensuring that the roll pins in
the sideplate engage into the bores in the round nuts To achieve
this it may be necessary to rotate the round nuts slightly.
9.) Tighten the security nuts (pos. 2) on the second sideplate.
Tighten the locknuts (pos. 8) fingertight and then a further 1/4
to 1/2 turn.
Attention:
The locknuts must always be fitted.
10.) By traversing the trolley check following:
That a clearance of 2 mm on each side between the trol-
ley wheel flanges and beam edge is maintained.
The centre traverse is centred below the beam.
That all 4 locknuts are fitted and secured.
11.) Model CPA-VTG only
To fit the handchain, position the slot on the outer edge of the
hand chain wheel below the chain guide. Place one link of the
hand chain vertically into the slot and turn the hand wheel until
the link has passed the chain guides on both sides.
Attention
: Do not twist the hand chain when fitting.
Pulling the hand chain moves geared trolleys
3.4 AIR PRESSURE CONNECTIONS
Attention
The brake opening pressure for the disc brake is: min.
2.6 bar. The ”hold open” pressure of 3 bar must be main-
tained, to ensure that the brake lining does not constantly
slip on the pressure plate.
The operating pressure is 4 - 6 bar.
The compressed air must be clean and enriched with oil to
guarantee adequate lubrication. We, therefore recommend the
use of an oiler that works on the ram-air principle with an ad-
justable jet. 1 cm
3
of oil amounts to 25 – 30 drops, 2 – 5 drops
are required for every m
3
of air used under normal conditions
(see following table).
In any case a lubricator unit comprising of a filter and an oiler
with a pressure regulator in-between (regulator independent
of supply pressure, adjustable and with pressure gauge). When
choosing a unit consider the rate of flow and ensure it is not
fitted more than 5 m away from the hoist.
The lubricant can be replenished in service without discon-
necting the air supply.
For the oiler we recommend a resin and acid free lubricating
oil (SAE 5W – SAE 10W), as thicker oils tend to clog the vanes
and reduce the performance of the motor.
The air hose should have a diameter of at least 19 mm. The
connection is R1”.
The connections on the control pendant must not be ex-
changed.