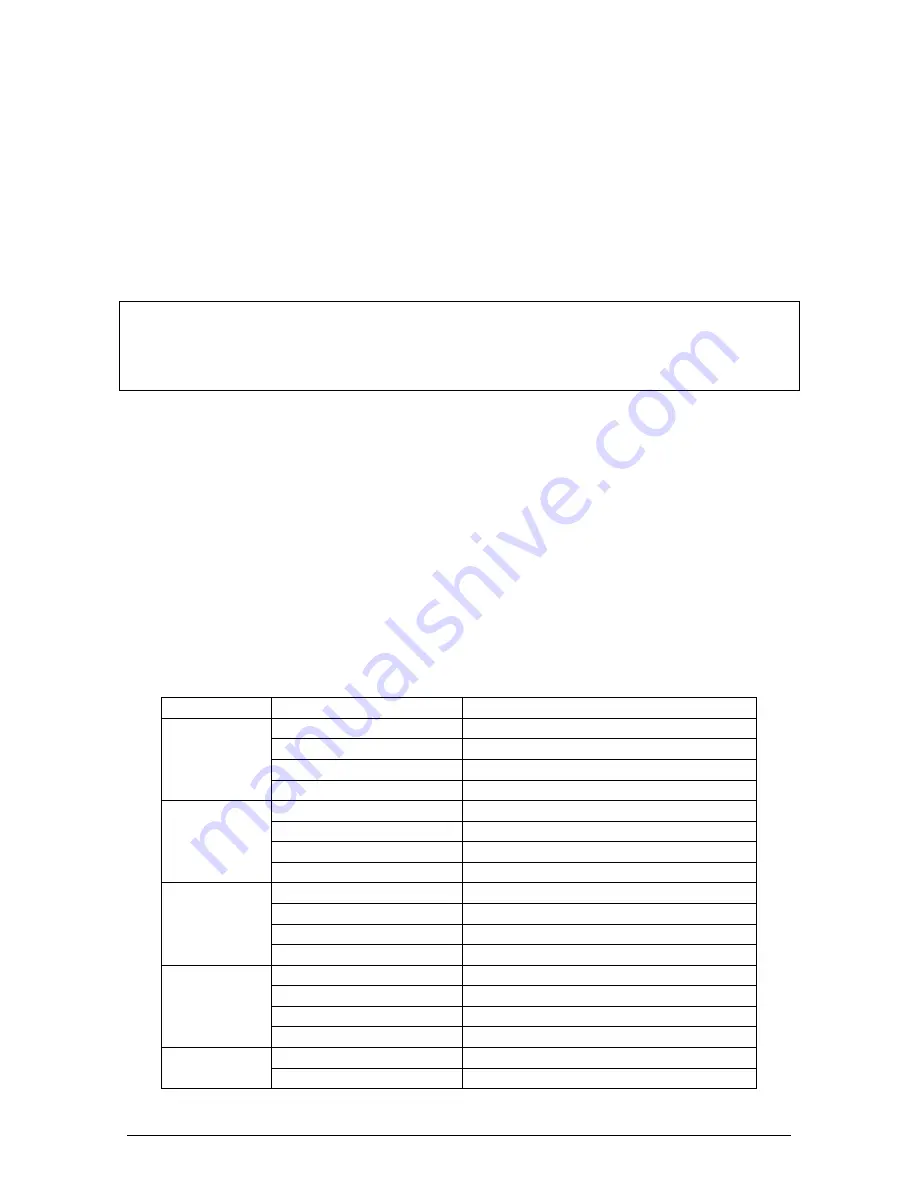
60
XYZ Machine Tools Ltd
XYZ Bed Mill Safety, Installation, Maintenance, Service & Parts List Manual
adjustment is necessary. Value 4.04 means the friction is a factor of 4 in one direction, and 4 in the
other direction. The values should be within 3 or 4 of each other in both directions. A value of 6.08
would still be considered normal.
The feed forward gain can be adjusted manually by pressing the manual button. Choose the axis you
would like to change and then enter values in the positive and negative direction to adjust. Adjusting
the gain can help solve circularity problems. Default values can be set by pressing the Reset button.
The manual feature should only be used in extreme cases where the AUTO routine did not solve the
problem. Manual adjusts above 12 may lead to servo related problems.
4.8.2.3
CODE 100: Axis Open Loop Test
Code 100 procedure is used to diagnose problems with the configuration of the system, the encoders
and incoming A/C voltage.
IMPORTANT -- SAFETY NOTICE
During this procedure the designated axis will be given a command to move at maximum
speed for 1 second in the direction you choose. Avoid crashes by making sure the quill is out
of the way and by starting with the table and saddle centred. MAKE SURE THAT NO ONE IS
STANDING IN THE WAY OF THE TABLE OR SADDLE!
Note: You will lose the DRO reference position.
This procedure is to be run for each axis that is servo-driven, and for both the plus and minus direction
for each axis.
1.
Centre the table and saddle and raise the head.
2.
On the Pendant display, go into the Service Codes and input the Code 100.
3.
The conversation line will say: “SELECT AXIS”. Input the axis. Either X, Y or Z.
4.
In the conversation line it will say “WHICH DIRECTION? PLUS”.
If you want to run in the plus direction, press INC SET.
If you want to run in the minus direction, press +/-, then INC SET
5.
In the conversation line it will say “PRESS GO”. Press Go after you are sure that the machine
will not crash in the direction and axis that you have specified.
6.
Afterward the screen will display values next to the DRO position axes. The table below
assumes machine has secondary feedback scales. Machines with motor encoders only will
display the reading next to the axis in question.
Your input
Display
Data displayed.
X +
X
Table encoder reading
Y
nothing (should be 0)
Z
Motor encoder reading
Feedrate
the maximum feedrate attained
X -
X
Table encoder reading
Y
nothing (should be 0)
Z
Motor encoder reading
Feedrate
the maximum feedrate attained
Y +
X
nothing (should be 0)
Y
Table encoder reading
Z
Motor encoder reading
Feedrate
the maximum feedrate attained
Y -
X
nothing (should be 0)
Y
Table encoder reading
Z
Motor encoder reading
Feedrate
the maximum feedrate attained
Z +
X
nothing (should be 0)
Y
nothing (should be 0)