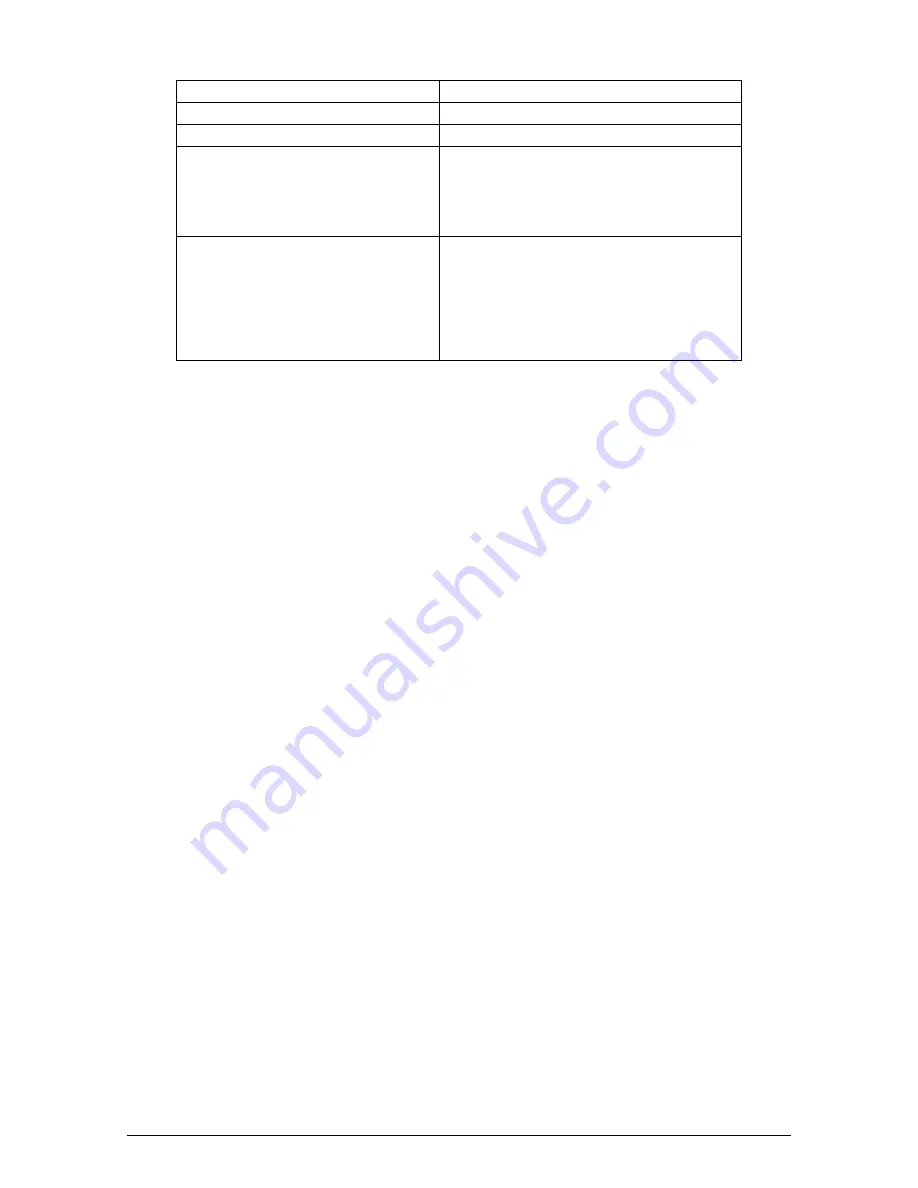
119
XYZ Machine Tools Ltd
XYZ Bed Mill Safety, Installation, Maintenance, Service & Parts List Manual
c. Select
c. Press SERV CODES
d. Select
d. Press “B”
e. Select Code 127
e. Press X or Y or Z
f. Backlash Value = _ _ _ _
f. What is shown is the current value. Follow
the instruction on the screen and press the
appropriate soft keys. Wait a few seconds
between each INCR VALUE or DECR VALUE
press.
g. The following is an example of what
you might see when running this code.
For example, if the up and down "Oscillation
Value" shown in the conversation line is .07
mm, and the dial indicator is moving back
and forth .03, then the true backlash value is
.07 .03 = .04 mm. Input this by pressing
MODE, SET UP, SERV CODE, 128, SET and
then .04, SET, RETURN.
3.
The X backlash identified and stored in Step 2 should be less than 0.076 mm on a new
machine. If it is appreciably larger, inspect the drive train for loose bolts, brackets, bearings,
etc.
CODE 128: Input Backlash Constant
Code 128 allows you to enter the backlash values, manually for each axis. It displays the value after
it is entered. This code is only used on machines without scales.
The measure the backlash manually, do the following:
1.
Set a 0.005 mm dial indicator in the spindle and load the indicator to zero from one direction
against a block or vice and zero out the DRO.
2.
Move the indicator to 0.05 mm and then back to zero. Do not over shoot 0, otherwise start
over.
3.
Whatever number appears on the screen is the backlash value.
4.
Enter this value into service code 128.
5.
After entering this number redo the process. The DRO and indicator should now both read 0.
5.2.3
Head Rotation and Tramming
The head is free to rotate up to 90 degrees to the right or left.
5.2.3.1
To Rotate the Head:
1.
Loosen the four locknuts.
2.
Rotate the head with the adjusting worm shaft.
3.
Tighten the locknuts. Snug each locknut, then lightly tighten each locknut, then fully tighten
each locknut in a crisscross pattern.
4.
Tram the head to the table to ensure it is square.
5.2.3.2
Tramming the Head
The purpose of tramming the head is make sure the head is perpendicular to the top surface of the
table from both side to side and back to front.
Side to side tolerance – 0.025 mm
Side-to-Side Alignment
1.
Make sure the machine is level.
2.
Make sure the table has been clean and the Z gibs are adjusted properly.
3.
Mount a dial indicator in a tool holder and mount in the quill.
4.
Adjust the Y-axis so that the spindle is in the centre of the table.
5.
Adjust the Z ram so that the dial indicator will reach the table.
6.
Move the dial indicator to 6 o’clock position and adjust the face so the needle is zero.