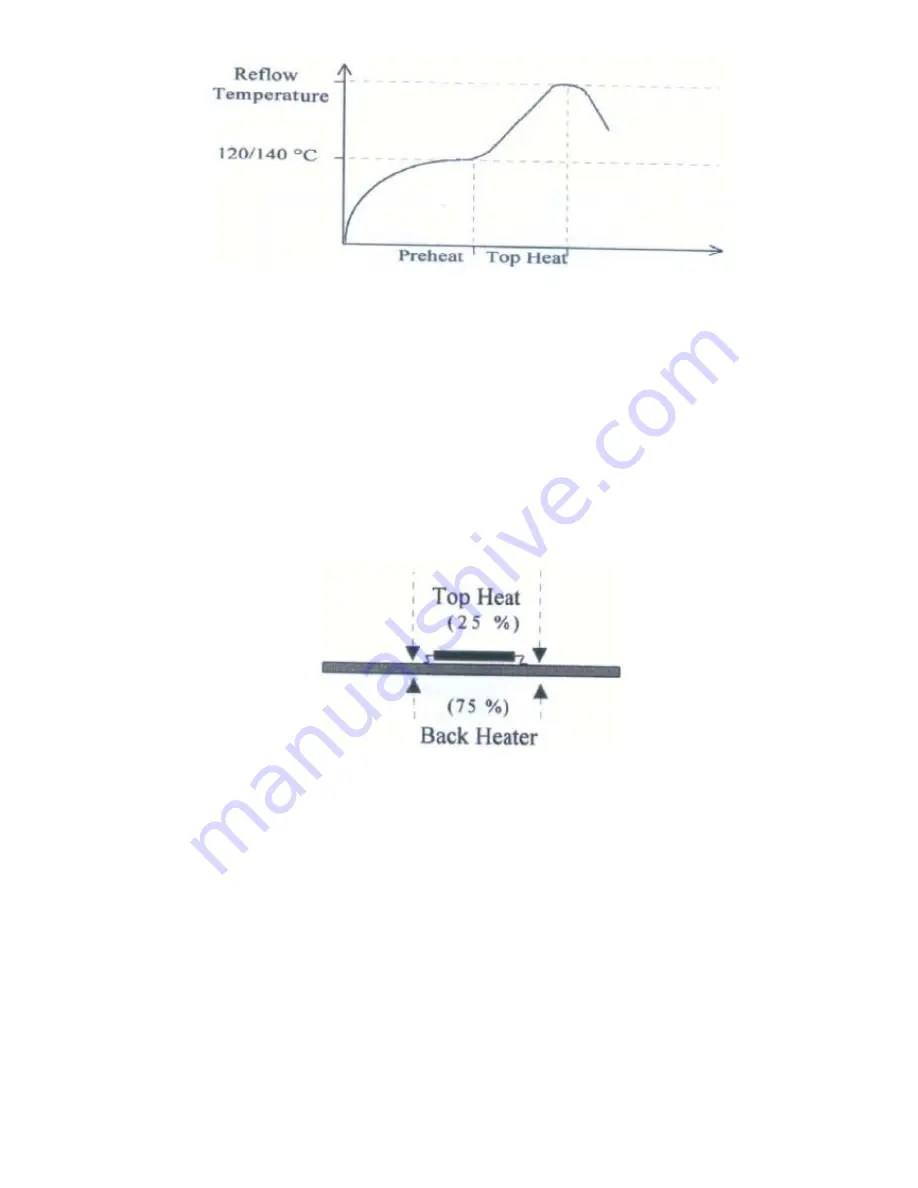
In operation the component is first put through a preheat stage, followed by a reflow stage.
The system is designed for rework single/double side and mixed technology PCB. The top
heat is derived from a 150W short wave IR lamp focused through a reflective chamber
system. The bottom heater delivers a maximum of 650W medium wave IR.
In normal use, approximately 25% of the energy is proved by the top heater, and 75% of the
energy is provided by the back heater (pre-heater). Figure below shows how the energy is
applied to a component.
Soldering
ٛ
PREPARATION -
Place PCB in the PCB holder, positioning the component site to
be reworked over the center of the PCB pre-heater. For BGAs, apply a very small amount of
gel flux (approx. 0.1 - 0.15mm) thickness). Place and align component. ( note – depending
on the application, y0ou may be required to apply solder paste to the PCB before placing
component.)
ٛ
(A) PREHEAT
– the fluxed component/PCB to approximately 120
℃
(as measured
by the IR sensor).
ٛ
(B) REFLOW
– use the IR hand tool (operated by pressing the footswitch) for the
reflow phase to heat the component up to reflow temperature (200-225
℃
). It is not so easy
to measure temperature during the reflow phase so therefore we use the timer on the IR 810
controller to limit the reflow phase time (normally 30-45 seconds for a small PCB).
ٛ
(C) SOAK
– for a short period to soak (about 10 seconds) the component allowing
the joints to fully bond.
ٛ
(D) COOL
– allow the component to cool to below 180
℃
before moving the PCB.