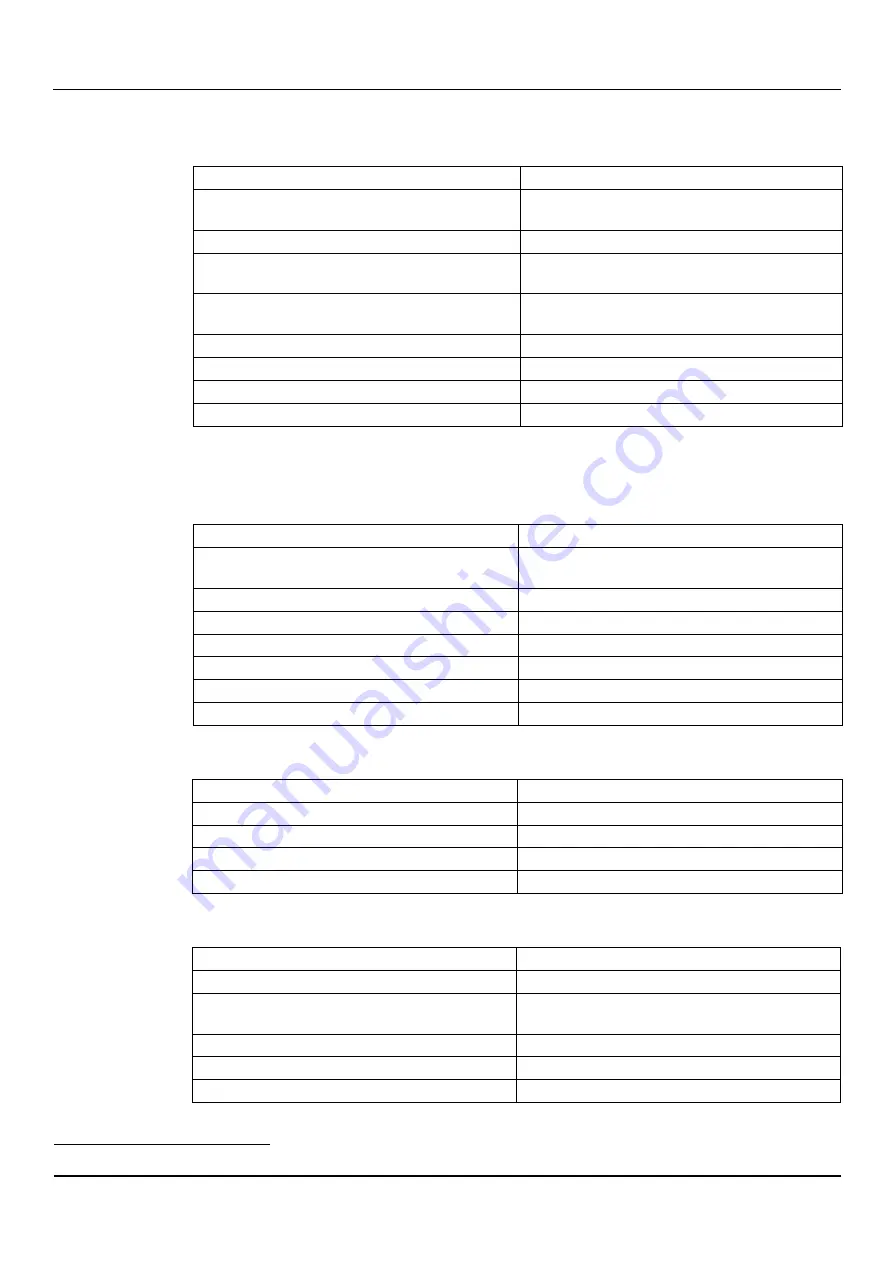
en – Original instructions
e-IXPS - Installation, Operation and Maintenance Instructions
31
7.5
The thermal overload protection triggers or the fuses trip
The motor thermal overload protection triggers or the fuses trip when the unit starts.
Cause
Solution
It is calibrated at a value too low in relation to the rated
current of the motor
Recalibrate
Missing power supply phase
Check the power supply and restore the phase
Loose and/or faulty connections of the thermal overload
protection
Tighten or replace the clamps and terminals
Loose and/or incorrect and/or faulty (star-delta) connections
in the terminal board of the motor
Tighten or replace the clamps and terminals
Motor (coil) faulty
Check and repair or replace the motor
Pump unit mechanically seized
Check and repair the pump unit
Check valve faulty
Replace the check valve
Foot check valve faulty
Replace the foot valve
7.6
The thermal overload protection triggers
The motor thermal overload protection triggers occasionally, or after the unit has been
running for a few minutes.
Cause
Solution
It is calibrated at a value too low in relation to the rated
current of the motor
Recalibrate
Input voltage outside the rated limits
Make sure the voltage values are correct
Unbalanced input voltage
Make sure the voltage of the three phases is balanced
Wrong duty point, flow rate above the permitted limits
Bring the flow rate back within the permitted limits
Liquid too thick
Check the liquid
Room temperature too high
Decrease the temperature
Unit faulty
Contact Xylem or the Authorised Distributor
7.7
The motor becomes excessively hot
Cause
Solution
Room temperature too high
Decrease the temperature
Motor cooling fan damaged
Replace the cooling fan
Too many starts
See paragraph 7.10
Frequency converter wrongly calibrated (if present)
See the frequency converter manual
7.8
Little or no hydraulic performance
Cause
Solution
Three-phase motor turning in the wrong direction
Check the direction of rotation and change if necessary
Incorrect priming (there are air bubbles in the suction pipe or
in the unit)
Repeat the priming procedure
Cavitation
Increase the NPSH
Check valve blocked or partially clogged
Replace the check valve
Piping and/or unit clogged
Remove the clogging
3
Net Positive Suction Head