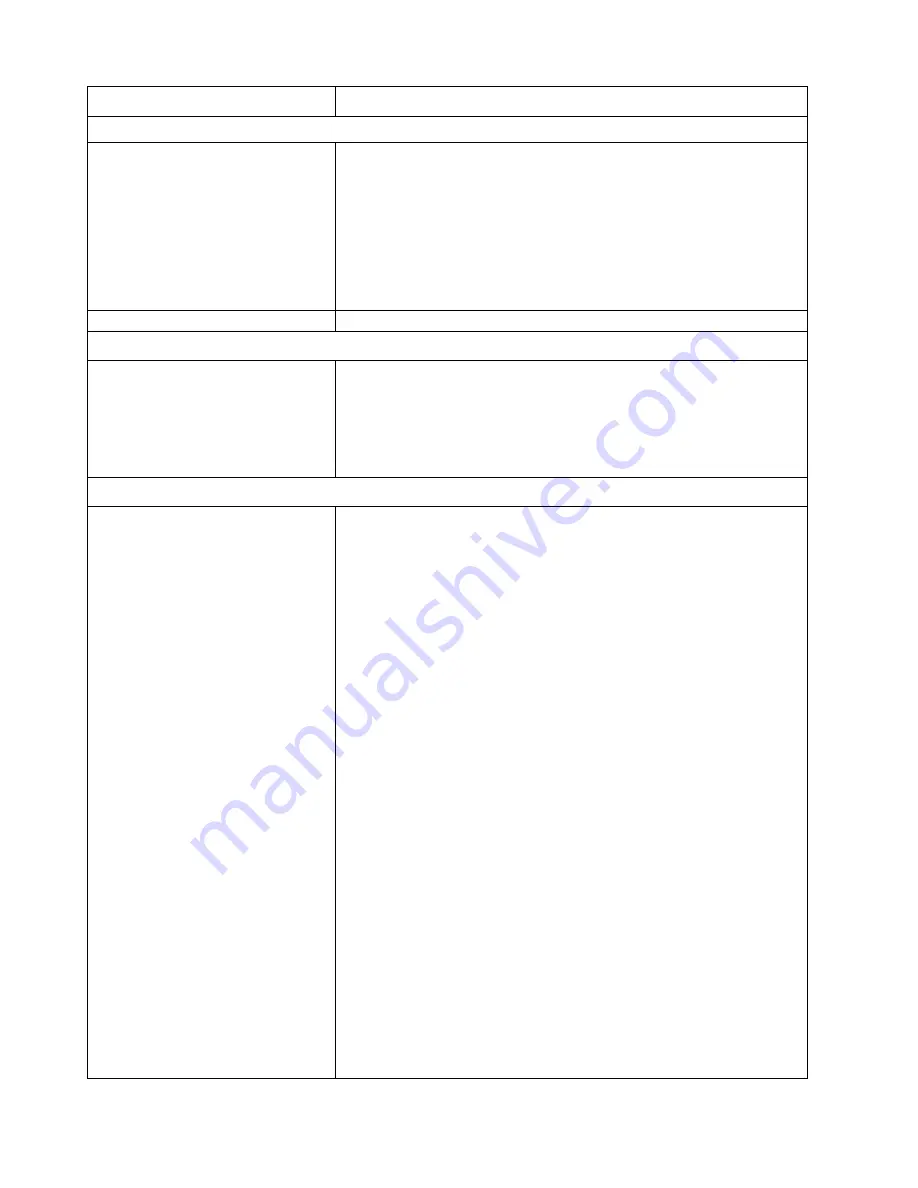
17
CAUSES
CURES
Not Enough Pressure
20. Mechanical defects
See items 14 and 15.
21. Obstruction in liquid passages Dismantle pump and inspect passages of impeller and casing.
Remove obstruction.
22. Air or gases in liquid (Test in
laboratory, reducing pressure on
liquid to pressure in suction line.
Watch for bubble formation.)
May be possible to overrate pump to the point where it will provide
adequate pressure despite condition. Better to provide gas
separation chamber on suction line near pump, and periodically
exhaust accumulated gas. See item 13.
23. Too small impeller diameter
(Probable cause if none above)
See item 18.
24. Speed too low
See item 5.
Pump Operates For Short Time, Then Stops
25. Incomplete priming
Free pump, piping and valves of all air. If high points in suction line
prevent this, they need correcting. See the section entitled Suction
Piping.
26. Suction lift too high
See item 3.
27. Air leaks in suction piping
See item 8.
28. Air or gases in liquid
See item 22.
Pump Takes Too Much Power
29. Head lower than rating;
thereby pumping too much liquid
Machine impeller’s OD to size advised by factory.
30. Cavitation
See item 13.
31. Mechanical defects.
See items 14 and 15.
32. Suction inlet not immersed
enough
See item 16.
33. Liquid heavier (in either
viscosity or specific gravity) than
allowed for
Use larger driver. Consult factory for recommended size. Test liquid
for viscosity and specific gravity.
34. Wrong direction of rotation
See item 6.
35. Casing distorted by excessive
strains from suction or discharge
piping
Check alignment. Examine pump for friction between impeller and
casing. Replace damaged parts.
36. Shaft bent due to damage –
through shipment, operation, or
overhaul
Check deflection of rotor by turning on bearing journals. Total
indicator run-out should not exceed 0.002” on shaft and 0.004” on
impeller wearing surface.
37. Mechanical failure of critical
pump parts
Check bearings and impeller for damage. Any irregularity in these
parts will cause a drag on shaft.
38. Misalignment
Realign pump and driver.
39. Speed may be too high (brake
hp of pump varies as the cube of
the speed; therefore, any increase
in speed means considerable
increase in power demand.)
Check voltage on motor.
40. Electrical defects
The voltage and frequency of the electrical current may be lower
than that for which the motor was built; or there may be defects in
motor. The motor may not be ventilated properly due to a poor
location.
41. Mechanical defects in turbine,
engine or other type of drive
exclusive of motor
If trouble cannot be located, consult factory.