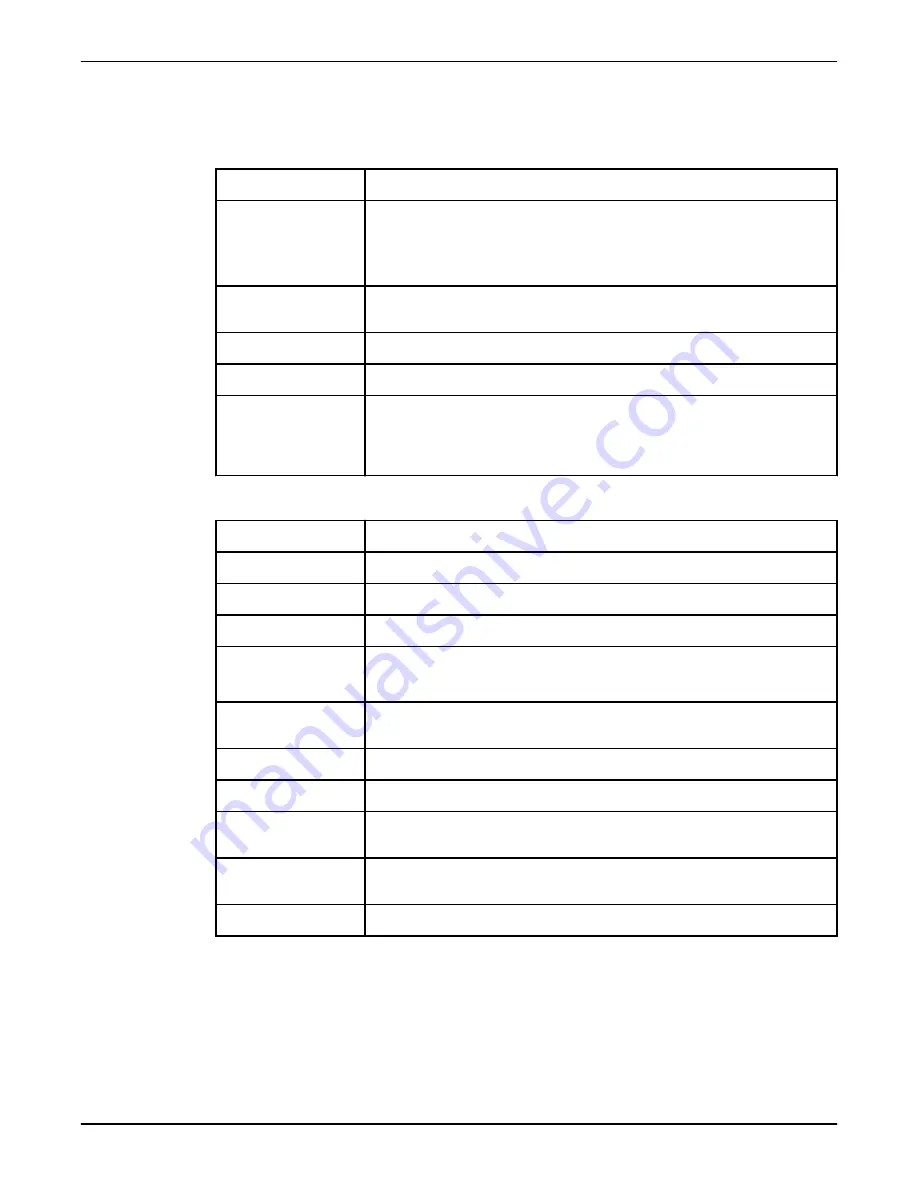
Technical Reference
Application limits
Data
Description
Media (liquid)
temperature
Standard temperature version: Maximum temperature 40°C (104°F)
Warm media (liquid) version: Maximum temperature 70°C (158°F)
Warm liquid has certain operational limitations, which are stated on a plate on the
pump.
pH of the pumped media
(liquid)
5–8
Media (liquid) density
Maximum density: 1100 kg/m
3
(9.2 lb. per US gal.)
Depth of immersion
20 m (65 ft.)
Other
For specific weight, current, voltage, power rating, and speed of the pump, see the data
plate on the pump. For starting current, see
For other applications, contact the local sales and service representative for
information.
Motor data
Feature
Description
Motor type
Squirrel-cage induction motor
Frequency
50 or 60 Hz
Supply
1-phase or 3-phase
Starting method
• Direct on-line
• Star-delta
Maximum starts per
hour
30 evenly spaced starts per hour
Code compliance
IEC 60034-1
Rated output variation
±10%
Voltage variation without
overheating
±10%, provided that it does not run continuously at full load
Voltage imbalance
tolerance
2%
Stator insulation class
F (155°C [310°F])
Specific motor data
1-phase, 60 Hz
Motor type:
• 3,430 rpm
• Rated output 3.1 kW (4.1 hp)
Technical Reference
Flygt 2071 Installation, Operation, and Maintenance Manual
39
Summary of Contents for FLYGT Flygt 2071
Page 1: ...Flygt 2071 Installation Operation and Maintenance Manual...
Page 2: ......
Page 45: ......