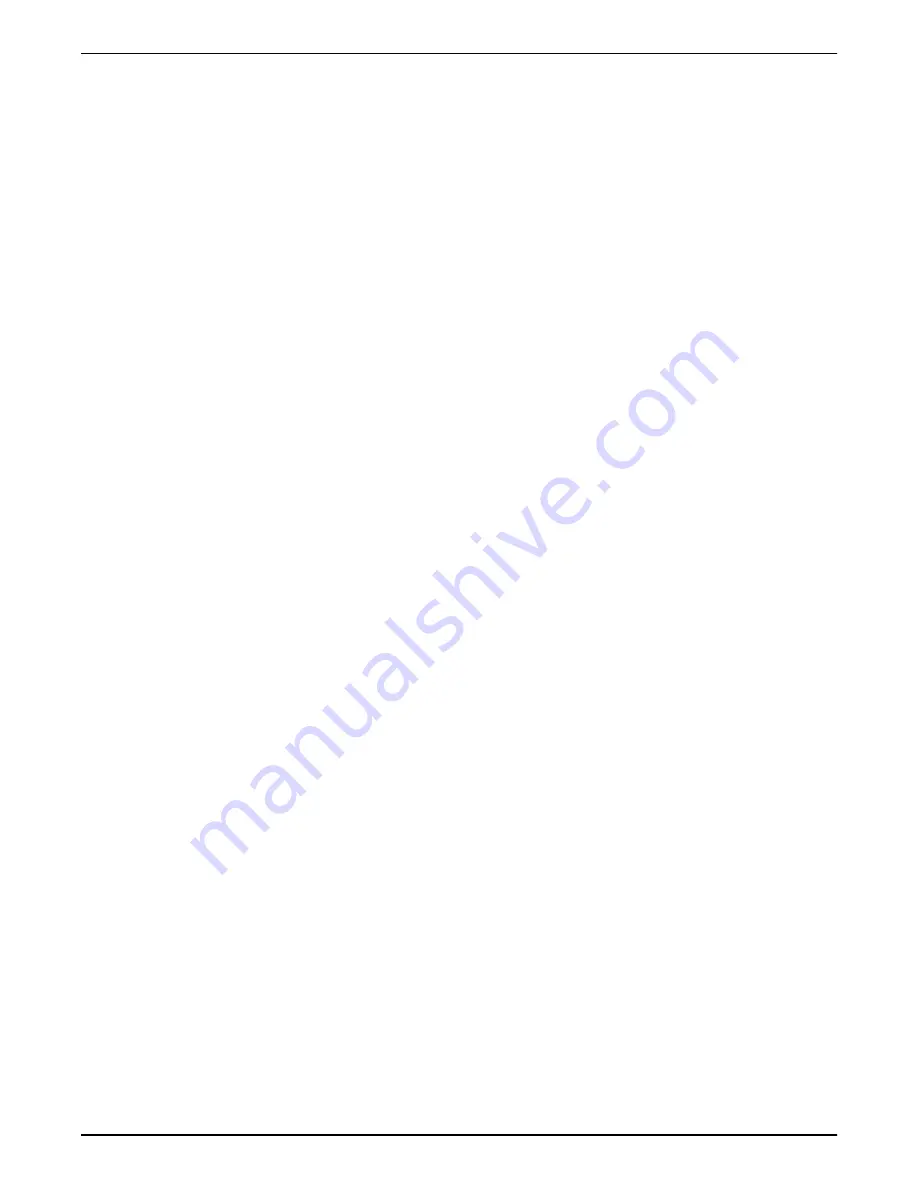
4. Assemble the stiffener clips [13] onto the bearing gland of the pump if they are not
already installed. Install one clip at a time. Remove one of the top two bearing gland
bolts and secure the long end of the stiffener clip to the bearing gland.
5. Attach the two motor side guard support brackets [5] and [6] to the lower guard
support [7] with a serrated hex bolt [9]. The hex bolt should pass through all three
parts and thread into a weld nut located at the bottom of one of the guard support
brackets.
– Note: The guard supports [5] and [6] should be identical in shape and size and hug
the outside profile of the outer hex guard [2]. Ensure the correct parts are being
used; otherwise, the guard support brackets will not align correctly with the outer
guard assembly.
– Note: The height of the guard support brackets may be adjusted after attaching the
outer guard assembly [2].
6. Place the lower half of the outer guard assembly [2] beneath the coupling with the
closed end of the outer guard facing the motor. Rest the flanges of the outer guard on
the guard support brackets [5] and [6].
– Repeat steps 2, 3, 5, and 6 for the inner guard assembly [1] using the pump-side
components.
– Note: The closed end of the inner guard assembly should face the pump.
7. Couple the bottom half of the outer [2] and inner [1] guard assemblies together by
fastening two serrated hex bolts [9] through the bottom face of the outer guard [2] and
into the weld nuts located inside the inner guard [1].
8. Place the upper half of the inner guard assembly [1] over the coupling with the closed
end of the inner guard facing the pump. Align the flanges and faces of the upper and
lower guard halves [1].
9. Secure the sides of the top half of the inner guard assembly [1] to the stiffener clips
[13]. Thread in a serrated hex bolt [9] through the short end of the stiffener clip [13]
and into the weld nut located on the inside of the guard assembly [1].
10.Secure the inner guard assembly [1] to the pump side guard supports, [3] and [4], with
a hex bolt [9]. Pass the bolt through the flanges of the inner guard halves and thread
them into the weld nuts located on the guard supports, [3] and [4].
11.Place the top half of the outer guard assembly [2] over the inner guard assembly [1].
Align the top and bottom halves of the outer guard [2] with one another. Fasten the
outer guard [2] to the inner guard [1] by threading two serrated hex bolts [9] through
the top face of the outer guard [2] into the weld nuts located along the inside of the
inner guard [1].
12.Secure the top and bottom halves of the outer guard [2] to the motor side guard
supports with two serrated hex bolts. Pass the bolt through the flanges of the outer
guard halves and thread them into the weld nuts located on the guard supports, [5]
and [6].
6 Maintenance
94
e-XC INSTRUCTION MANUAL
Summary of Contents for e-XC
Page 1: ...INSTRUCTION MANUAL P6019152 e XC Single Stage Double Suction Centrifugal Pumps ...
Page 2: ......
Page 109: ......
Page 110: ......
Page 111: ......