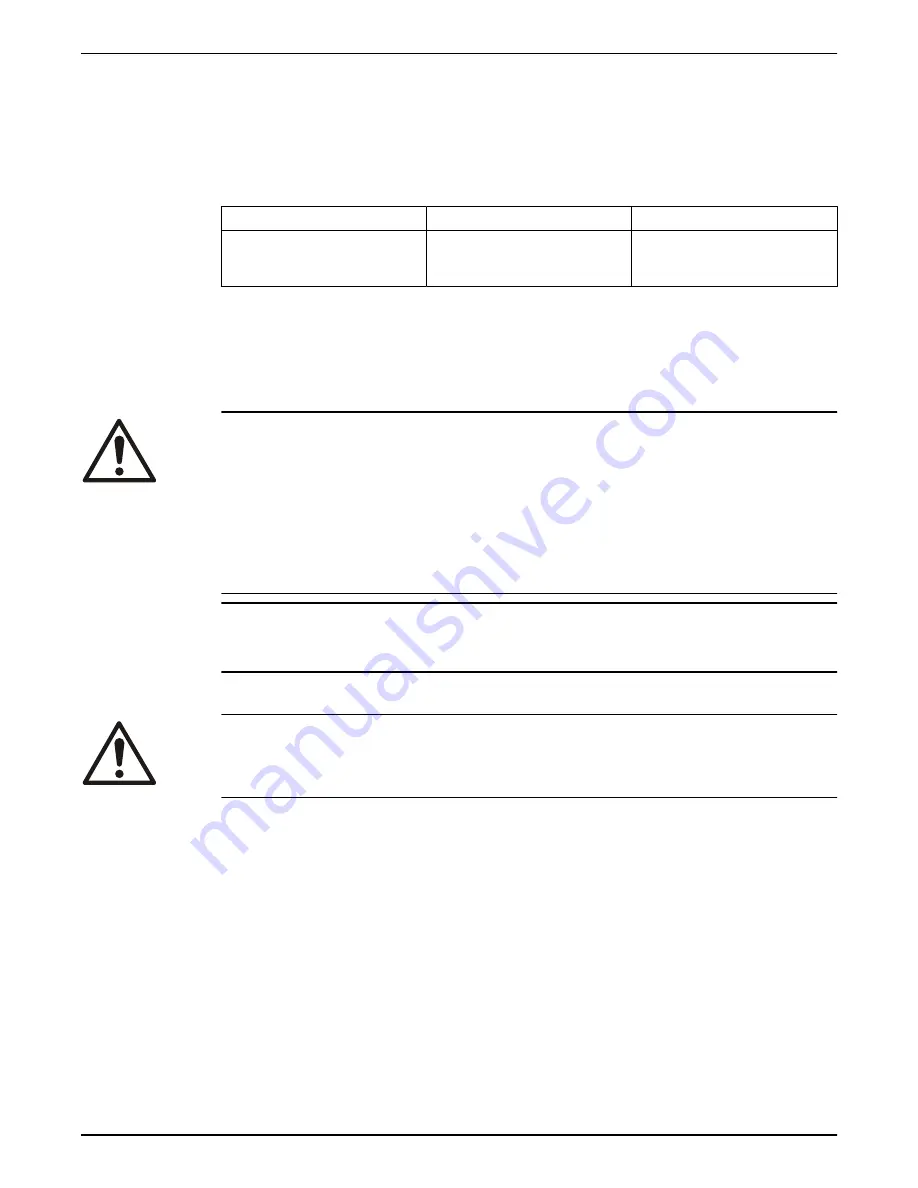
6 Maintenance
6.1 Bearing maintenance
Bearing lubrication schedule
Type of bearing
First lubrication
Lubrication intervals
Motor bearings
No initial lubrication. The motor was
lubricated at the factory.
Refer to the motor manufacturer's
recommendations for lubrication
intervals.
6.2 Disassembly
6.2.1 Disassembly precautions
This manual clearly identifies accepted methods for disassembling units. These methods
must be adhered to.
WARNING:
• Make sure that the pump is isolated from the system and that pressure is relieved
before you disassemble the pump, remove plugs, open vent or drain valves, or
disconnect the piping.
• Always disconnect and lock out power to the driver before you perform any installation
or maintenance tasks. Failure to disconnect and lock out driver power will result in
serious physical injury.
• Crush hazard. The unit and the components can be heavy. Use proper lifting methods
and wear steel-toed shoes at all times.
NOTICE:
Make sure that all replacement parts are available before you disassemble the pump for
overhaul.
6.2.2 Drain the pump
CAUTION:
• Allow all system and pump components to cool before you handle them to prevent
physical injury.
1. Close the isolation valves on the suction and discharge sides of the pump.
You must drain the system if no valves are installed.
2. Open the drain valve.
Do not proceed until liquid stops coming out of the drain valve. If liquid continues to
flow from the drain valve, the isolation valves are not sealing properly and you must
repair them before you proceed.
3. Leave the drain valve open and remove the drain plug located on the bottom of the
pump housing.
Do not reinstall the plug or close the drain valve until the reassembly is complete.
4. Drain the liquid from the piping and flush the pump if it is necessary.
5. Disconnect all auxiliary piping and tubing.
6.2.3 Remove the rotating assembly and motor
1. Remove the motor foot capscrews.
2. Loosen the volute capscrews but do not remove them.
6 Maintenance
Series e-1531 and e-1532 INSTRUCTION MANUAL
21
Summary of Contents for e-1531 Series
Page 1: ...INSTRUCTION MANUAL P2001409 Rev D e 1531 e 1532 Series e 1531 and e 1532...
Page 2: ......
Page 33: ......
Page 34: ......
Page 35: ......