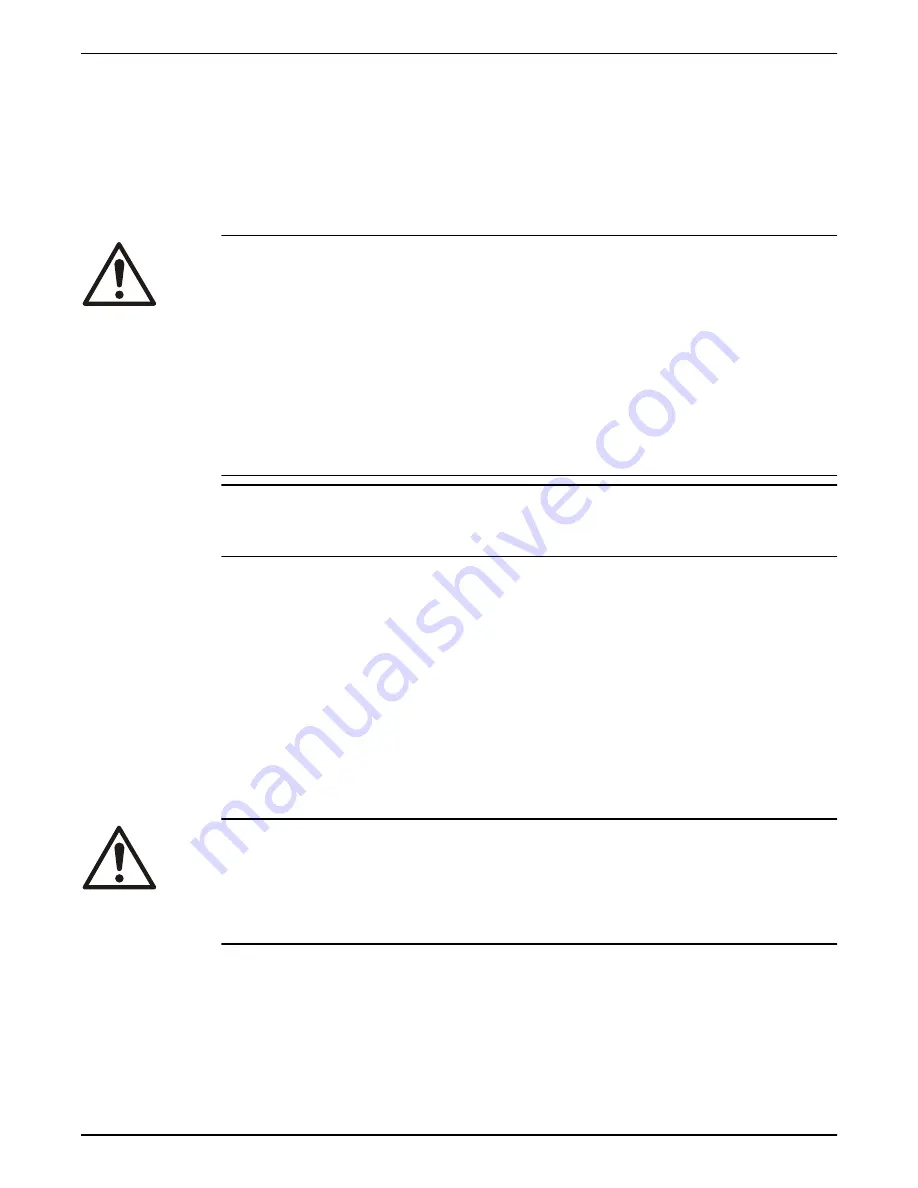
5 Commissioning, Startup,
Operation, and Shutdown
5.1 Preparation for startup
WARNING:
• Failure to follow these precautions before you start the unit will lead to serious
personal injury and equipment failure.
• Do not run the pump dry.
• Do NOT operate the pump at zero flow or with suction and discharge valves closed.
These conditions can create an explosive hazard due to vaporization of pumped fluid
and can quickly lead to pump failure and physical injury.
• Always disconnect and lock out power to the driver before you perform any installation
or maintenance tasks. Failure to disconnect and lock out driver power will result in
serious physical injury.
• Operating the pump in reverse rotation can result in the contact of metal parts, heat
generation, and breach of containment.
NOTICE:
• Verify the driver settings before you start any pump.
• Make sure that the warm-up rate does not exceed 2.5°F (1.4°C) per minute.
You must follow these precautions before you start the pump:
• Flush and clear the system thoroughly to remove dirt or debris in the pipe system in
order to prevent premature failure at initial startup.
• Bring variable-speed drivers to the rated speed as quickly as possible.
• If temperatures of the pumped fluid will exceed 200°F (93°C), then warm up the pump
prior to operation. Circulate a small amount of fluid through the pump until the casing
temperature is within 100°F (38°C) of the fluid temperature.
At initial startup, do not adjust the variable-speed drivers or check for speed governor or
over-speed trip settings while the variable-speed driver is coupled to the pump. If the
settings have not been verified, then uncouple the unit and refer to instructions supplied
by the driver manufacturer.
5.1.1 Check the rotation
WARNING:
• Operating the pump in reverse rotation can result in the contact of metal parts, heat
generation, and breach of containment.
• Always disconnect and lock out power to the driver before you perform any installation
or maintenance tasks. Failure to disconnect and lock out driver power will result in
serious physical injury.
1. Lock out power to the driver.
2. Make sure that the coupling hubs are fastened securely to the shafts.
3. Unlock power to the driver.
4. Make sure that everyone is clear, and then jog the driver long enough to determine
that the direction of rotation corresponds to the arrow on the pump.
5. Lock out power to the driver.
5 Commissioning, Startup, Operation, and Shutdown
20
Series e-1510 INSTRUCTION MANUAL
Summary of Contents for Bell & Gossett e-1510 Series
Page 1: ...INSTRUCTION MANUAL P2001406 Rev E Series e 1510...
Page 2: ......