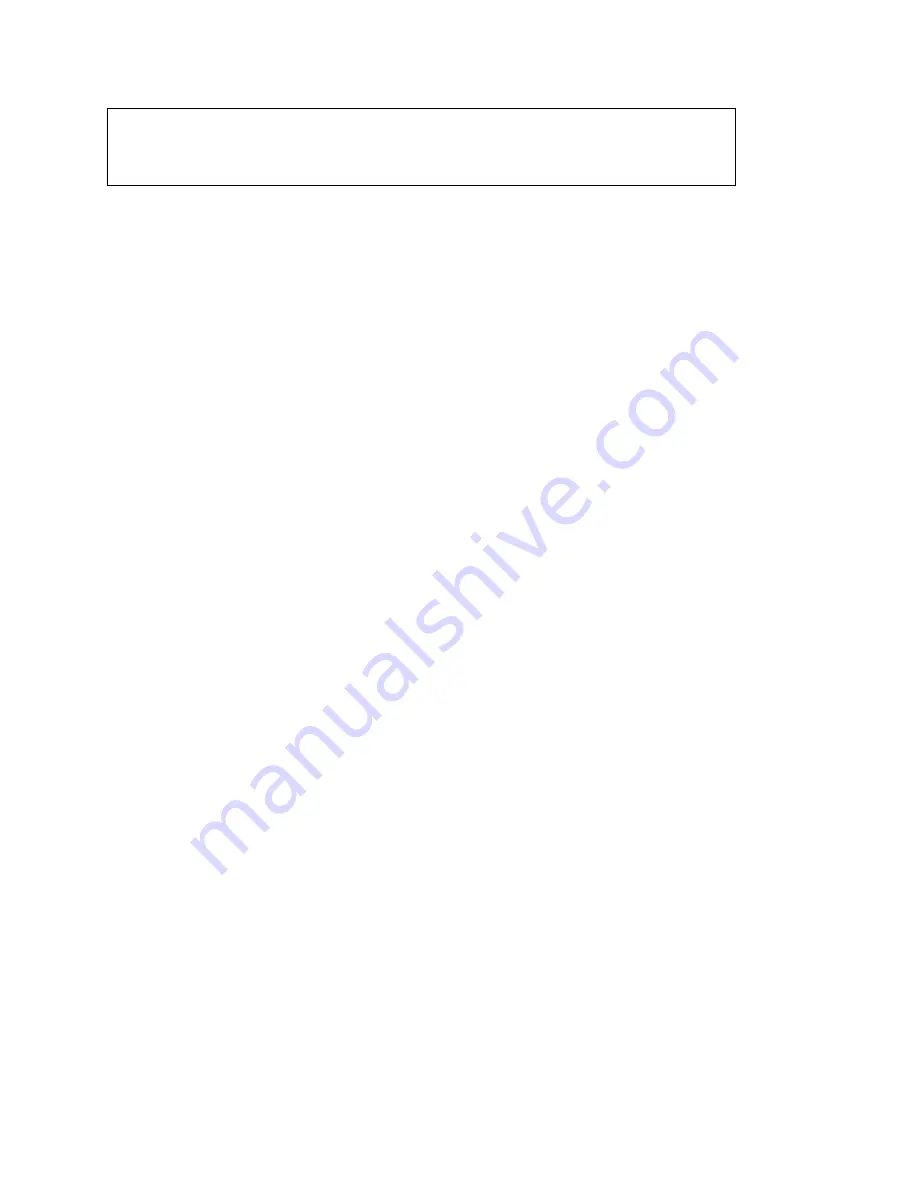
Revision
A
B
C
Description
Manual released
Preliminary revision released for new controller board
Manual updated
Date
12/01
06/02
06/02
Xycom Automation Part Number 141284(C)
Trademark Information
Xycom Automation is a trademark of Xycom Automation, Inc. Brand or product names may be
registered trademarks of their respective owners. Windows is a registered trademark of
Microsoft Corporation in the United States and other countries.
Copyright Information
This document is copyrighted by Xycom Automation Incorporated (Xycom Automation) and shall
not be reproduced or copied without expressed written authorization from Xycom Automation.
The information contained within this document is subject to change without notice. Xycom
Automation does not guarantee the accuracy of the information.
United States FCC Part 15, Subpart B, Class A EMI Compliance Statement:
NOTE: This equipment has been tested and found to comply with the limits for a Class A digital
device, pursuant to part 15 of the FCC Rules. These limits are designed to provide reasonable
protection against harmful interference when the equipment is operated in a commercial
environment. This equipment generates, uses, and can radiate radio frequency energy and, if
not installed and used in accordance with the instruction manual, may cause harmful
interference to radio communications. Operation of this equipment in a residential area is likely
to cause harmful interference in which case the user will be required to correct the interference
at his own expense.
For European Users: WARNING
This is a Class A product. In a domestic environment this product may cause radio interference
in which case the user may be required to take adequate measures.
INSTALLATION: Electromagnetic Compatibility WARNING
The connection of non-shielded equipment interface cables to this equipment will invalidate
FCC EMI and European Union EMC compliance and may result in electromagnetic interference
and/or susceptibility levels which are in violation of regulations which apply to the legal
operation of this device. It is the responsibility of the system integrator and/or user to apply the
following directions which relate to installation and configuration:
All interface cables must include shielded cables. Braid/foil type shields are recommended.
Communication cable connectors must be metal, ideally zinc die-cast backshell types, and
provide 360 degree protection about the interface wires. The cable shield braid must be
terminated directly to the metal connector shell, ground drain wires alone are not adequate.
Protective measures for power and interface cables as described within this manual must be
applied. Do not leave cables connected to unused interfaces or disconnected at one end.
Changes or modifications to this device not expressly approved by the manufacturer could void
the user's authority to operate the equipment.