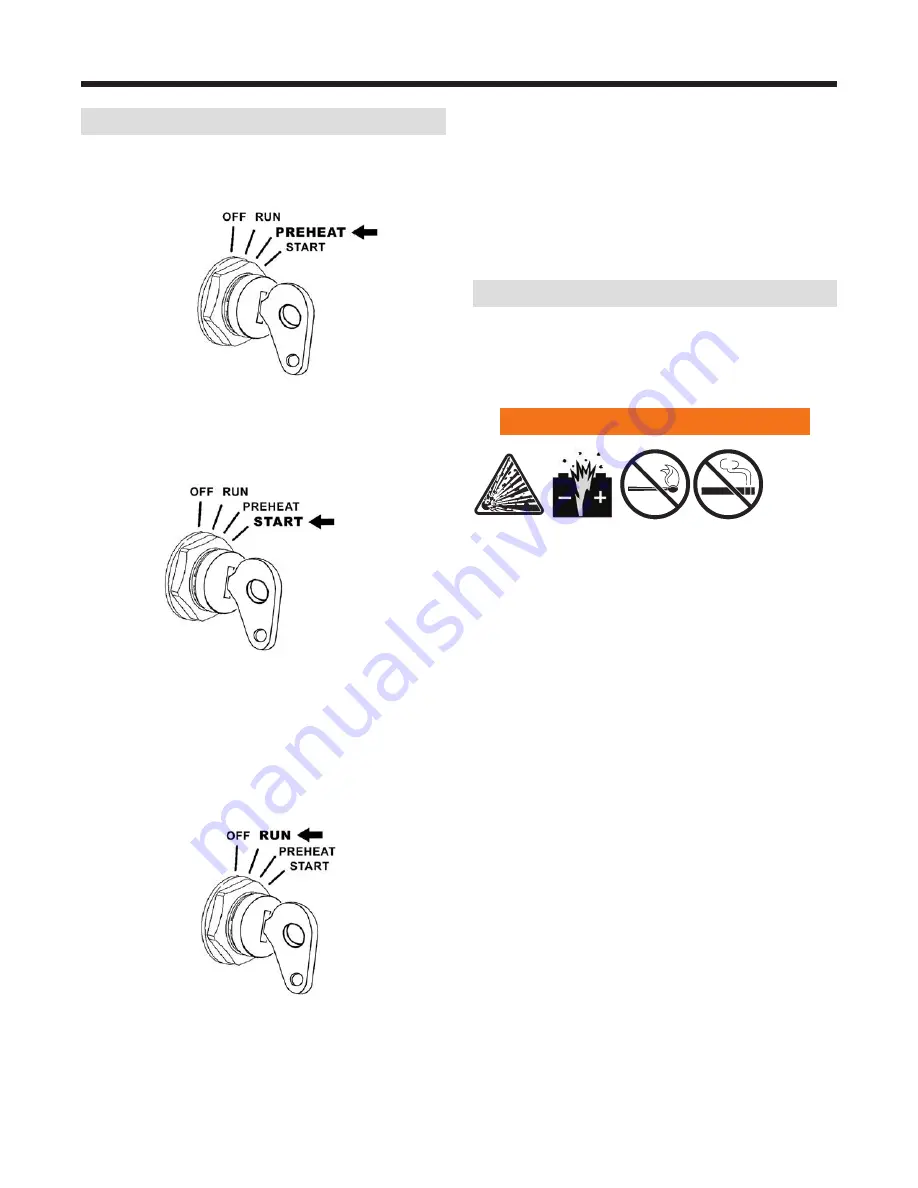
Page 52
Xtreme Manufacturing, LLC
Operation
XR1045
Cold Starting
2.
Turn key in Ignition switch clockwise to the
PREHEAT position and hold the key at PREHEAT for
approximately one (1) minute
Figure 7-10. Hold Key At PREHEAT.
3.
Turn key in Ignition switch clockwise to the
START position
Figure 7-11. Turn Key In Ignition Switch To START.
4.
Release the key immediately after the engine starts
The Ignition switch will automatically return to RUN
NOTE:
The PREHEAT and START positions are spring-
loaded When the key is released, the Ignition switch
will automatically return to the RUN position
Figure 7-12. Ignition Switch Automatically Returns To RUN.
NOTE:
If the engine fails to start on the first try, wait
until the engine and starter come to a complete stop
before cranking the engine again
5.
After the engine starts, allow the engine to idle for
approximately 60 seconds
6.
Apply the service brake pedal and disengage the
Parking Brake switch
Jump Starting
Jump start or replace the battery of the reach forklift when
the battery is discharged to the point that it will not crank
the starter
Warning
Lead-acid batteries produce flammable and
potentially explosive gases. To avoid death or serious
injury when checking, testing, or charging batteries:
• DO NOT use smoking materials near batteries.
• Keep arcs, sparks, and open flames away from
batteries.
• Provide ventilation for flammable vapors
• Wear proper personal protective equipment,
including safety glasses.
Fluid in electric storage batteries contains sulfuric
acid, which is poison and can cause severe chemical
burns. Avoid all contact of fluid with eyes, skin,
or clothing. Use protective gear when handling
batteries. DO NOT tip a battery beyond a 45° angle
in any direction.
If contact does occur, follow these First Aid
suggestions:
• External contact - Flush with water.
• Eyes - Flush with water (including under the eyelids)
for at least 15 minutes and get medical attention
immediately. Flushing must begin immediately to
avoid permanent eye tissue damage.
• Internal contact - Drink large quantities of water
or milk to dilute stomach contents. Do not induce
vomiting. Get medical attention immediately.
Important - In case of internal contact, do not give
fluids that induce vomiting.